Nilpeter digitalizes flexo at open house
A repurposed Technology and Educational Center highlights Nilpeter’s educational focus.

Nilpeter hosted an open house in April at its repurposed large-scale Technology and Educational Center in Cincinnati, Ohio. Apart from spotlighting the company’s entire fleet from its legacy FBs to the latest FAs, Nilpeter also showcased how it is digitalizing flexo.
The one-day event, themed ‘Expanded Color Gamut’, drew 150 guests and 25 tabletop exhibitors alongside presenters from Catapult Print, Flexografi x, Techkon USA and Clemson University.
Nilpeter will launch the new FB-14 fl exo press, which will also be showcased at Labelexpo Americas 2024 in September alongside an FA-26, emphasizing the efficiency gains of the conventional technology.
‘We’ve digitalized flexo,’ says Lenny DeGirolmo, president of Nilpeter USA. ‘Flexo is very comparable now with digital in regard to the setups, the wastes and the runs.’
Digitalizing flexo is 80 percent about automating the pre-press process, DeGirolmo explains: ‘We’ve automated all the moving parts within the printing process of these presses. From plate cylinders to chill rolls, side-to-side, front-to-back movement, it’s all been automated.’
Expanded color gamut
In particular, the open house aimed to emphasize efficiencies to be gained by running jobs with an expanded color gamut (ECG).
Printing with expanded gamut process colors allows for a broader color gamut and typically includes CMYK plus orange, green and violet. By adding these three additional base inks into the process, converters can achieve a much closer match to traditional formulated spot ink colors as well as eliminate the need to wash up the press between jobs.
Ken Pavett, CEO and chief technical officer of Flexografix in Carol Stream, Illinois, in his presentation ‘Understanding expanded color gamut: a scientific perspective’, referenced the 2021 dissertation of Dr Kai Lankinen, a renowned ECG expert.
“We’ve digitalized flexo. Flexo is very compatible now with digital in regard to the setups, the wastes and the runs”
Lankinen, who previously conducted a feature on ECG at Labelexpo Europe 2023, says on his website that with ECG, converters can increase their efficiency by 30 percent and reduce their carbon footprint by 20 percent.
Minimizing or eliminating solvent use in the plate production process is a key step for many flexo printers in reducing their carbon footprint by offering a more sustainable operation and a cleaner working environment.
In his ‘Evaluation of expanded gamut printing in flexography’, Lankinen ‘evaluates the transition from spot color printing to Expanded Gamut Printing, EGP, i.e., a multicolor process in solvent-based wide web fl exography, which reduces the complexity of the printing process and produces spot color simulations in a simpler, more effective and more sustainable way.’
Despite such potential gains, however, there are some challenges to ECG acceptance, which Pavett addressed. For instance, some barriers to ECG adoption include limited reference information available, uncertainty about how to sell, or fears of reproduction and process control problems.
In his ‘Printing by the numbers: maintaining perfect expanded gamut color at full press production speeds’, George Adam, president of Techkon USA touched on the importance of pressroom color control with ECG and highlighted the benefits of Techkon’s SpectroVision in-line color measurement system. ‘It provides real-time feedback during make-ready and production to remove the guesswork for press operators with clear actional feedback regarding color press adjustments,’ he says.
Thus, ECG means fewer changeovers and more savings. ‘The most important piece in production is to reduce make-ready,’ Adam adds. ‘Make-ready is losing money.’
Other presenters at the open house included Lewis Cook, co-founder and CEO at Catapult Print and Chip Tonkin, chair of the Department of Graphic Communications at Clemson University, who presented ‘What is expanded color gamut and its benefits’.
Unparalleled transparency
At the open house, Cook’s presentation, ‘How catapult print uses expanded color gamut’, struck a chord with the converters in the crowd. After the session, multiple printers handpicked his presentation as their key takeaway.
Cook talked about using a scientifi c, data-driven approach to cut lead times and maximize output.
Crystal, Catapult’s purpose-built platform, serves as an in-house system and is utilized internally and externally by a majority of its clients. The client portal provides real-time data on all aspects of its projects, artworks, orders and inventory, providing full visibility of each job.
‘As a data-driven company, Crystal empowers us to utilize this wealth of information to create key performance indicators (KPIs) for our clients,’ Cook says. ‘We can track metrics such as on-time delivery percentages and order fulfillment rates, all of which consistently exceed industry standards. Crystal is integral to our commitment to efficiency, transparency, and exceptional service.’
Armed with the latest technologies, such as automation tools, the Orlando, Florida-based converter has sold over 513 million labels since January, up 45.8 percent from the same period last year. That’s 52 million feet of labels in the first three months of the year, also up 16.6 percent from Q1 2023.
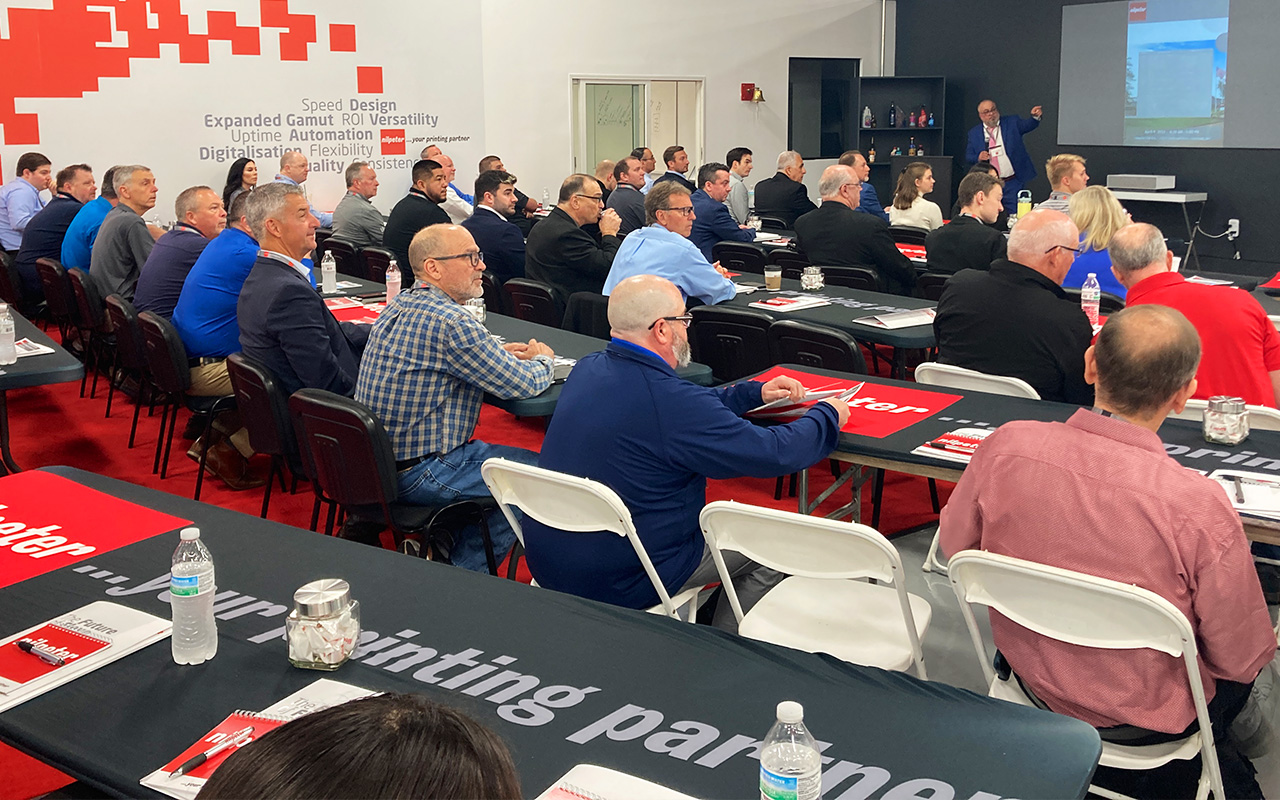
Catapult hit a sales increase of 32.4 percent with a total of 8,300 SKUs dispatched this past quarter, 1,800 across the US and Canada within two days of order. In Q1 2024, Catapult fulfilled 99 percent of orders on time with an average lead time of 5.3 days and 21 percent of orders within just two days.
With Nilpeter, Catapult has found its partner for growth: ‘This is the most automated flexo on the market,’ Cook says. ‘We believe in these presses.’
Catapult installed the first Nilpeter FA-26 press with a die station in the US, its eighth FA-line press but the first in 26in web width that will take production wider and faster.
Kevin Kollman, president and owner of Prime Packaging based in Wood Dale, Illinois, also bought an FA-26 in December and was among the guests.
Prime Packaging, which specializes in flexible packaging, invested in the Nilpeter FA-26, a 10-color flexo to enhance the company’s production capabilities and expand into new markets, such as the health and beauty sectors.
Over the years, the converter has pivoted to focus on flexible packaging, with about 70 percent of its customer base coming from the food and beverage sector servicing products such as dry seasoning pouches, roll-fed labels and shrink sleeves.
The press, running two shifts to meet increased demand since December, represents Prime Packaging’s first venture with Nilpeter,driven by a need to stay competitive in a fast-evolving market.
‘Our older presses couldn’t keep up with our increased customer demand and the desire to implement expanded color gamut printing capabilities,’ Kollman says.
Since it went into operation, the press has been making significant strides for Prime Packaging by allowing the production of more complex images and vibrant flesh tones, comparable to that of digital and offset printing platforms.
‘It’s not just about meeting demand, it’s about exceeding it. With features, such as sleeve-based tooling, job memory and advanced-register control, we’re not just keeping pace; we’re setting the pace,’ Kollman adds. ‘We knew that stepping up our capabilities would be good, but the performance of this new press has exceeded our expectations. We have been able to secure new business and offer a greater quality of product to our customers.’
“This is the most automated flexo on the market. We believe in these presses”
Kollman came to the open house in April to learn about the manufacturer’s new presses and industry trends, noting a key benefit of ECG is a fewer number of changeovers. ‘ECG saves our customers money by reducing our setup times, number of make-readies and our overall waste,’ he says.
DeGirolmo adds: ‘Our FA-26 flexo press is truly making its mark in the US, where it’s highly sought after due to its performance capabilities in flexible packaging, expanded color gamut, automation and digitalization features, all of which are essential for a modern printing facility. These were exactly the attributes Prime Packaging was looking for, and it’s gratifying to see the press proving its worth from day one at their location.’
Educational focus
The repurposed 75,000sqft facility, now the company’s largest technological center worldwide complete with a machine shop, has broadened its focus beyond manufacturing to include a demo floor to showcase its revamped ‘Future of flexo’ portfolio.
The move comes as the company pivots to spotlight its education component.
‘Nilpeter is focusing more on educating customers and teaching them different ways to do things than just worrying about selling a piece of steel,’ DeGirolmo says. ‘Because if customers are not successful, we’re not successful.’
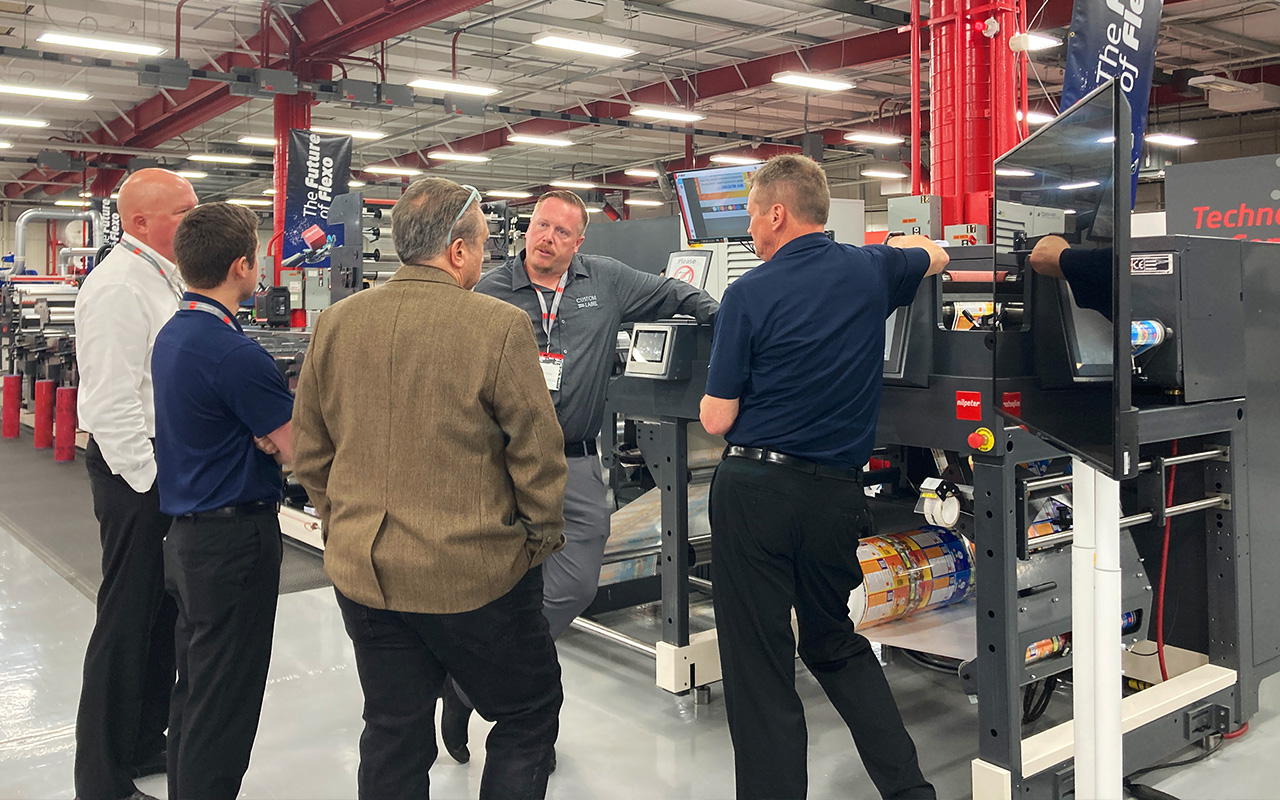
At the open house, attendees got a first tour of the Ohio facility. The demo floor includes the company’s FA-17, FA-26, FB-350, digital rewinders and a hybrid, and the new FB-14.
‘With three production sites across Denmark, US and India, the first question clients often ask is: where is this press manufactured,’ says Tom Clawson, Nilpeter senior sales consultant. According to Clawson, FA-26s are manufactured in Denmark, FBs in India and FA-17s in Europe or the US, depending on production and configuration.
‘There is a lot of talk in the flexo industry today about automation,’ Clawson says. At the forefront of the pack are the Nilpeter FAs, he says, calling the presses ‘the most advanced flexo in the world.’
What makes the Nilpeter FAs so advanced? ‘The secret is in the chill rolls,’ he says. ‘We make it ourselves for a reason.’
Behind the scenes on the shop floor in Ohio, lights-out manufacturing is further automating the process with programmed robots finishing making parts after the workers go home.
Exhibitors included Actega North America, BST North America, CTS Industries, Daetwyler USA, Danko Industries, Flexo Wash, Flexographic Technical Association, GEW, Label Traxx, Lundberg Tech, Provident, RotoMetrics, Siegwerk and Univacco Foils.
‘The open house was a great success,’ DeGirolmo says. ‘People are saying it was one of the best events they attended and walking away with new knowledge
Click here to see how industry disruptor Catapult Print is maximizing efficiency with Nilpeter.
Stay up to date
Subscribe to the free Label News newsletter and receive the latest content every week. We'll never share your email address.