ArcLED enables Label Design's measured transition to UV LED
Label Design faced strict food packaging regulations, so UV LED had to be tested thoroughly.

L to R: Frank Oudesluys, Chris Glazier and Manuel Garces at Label Design's HQ in Guelph, Ontario.
Label Design is a fully SQF (Safe Quality Food) Certified manufacturing operation located in Guelph, Ontario. The company specializes in supplying pressure-sensitive labels to customers across Canada. By continuously renewing its technology and focusing on quality and customer needs, Label Design has grown steadily since its foundation in 1990.
Frank Oudesluys is owner and president of the company. After having worked for CCL and Avery Dennison for a number of years, he decided to venture out on his own and form Label Design, which has since become one of the most successful printing businesses in the Toronto area.
Oudesluys describes those early days: ‘In 1990, I decided to follow my dream and start a label business, selling labels by day and running them by night, and with my wife as a part-time bookkeeper, we opened up a small shop in the corner of a huge plant with a little 3-color central impression Mark Andy... and that's how we began... Label Design was born.’
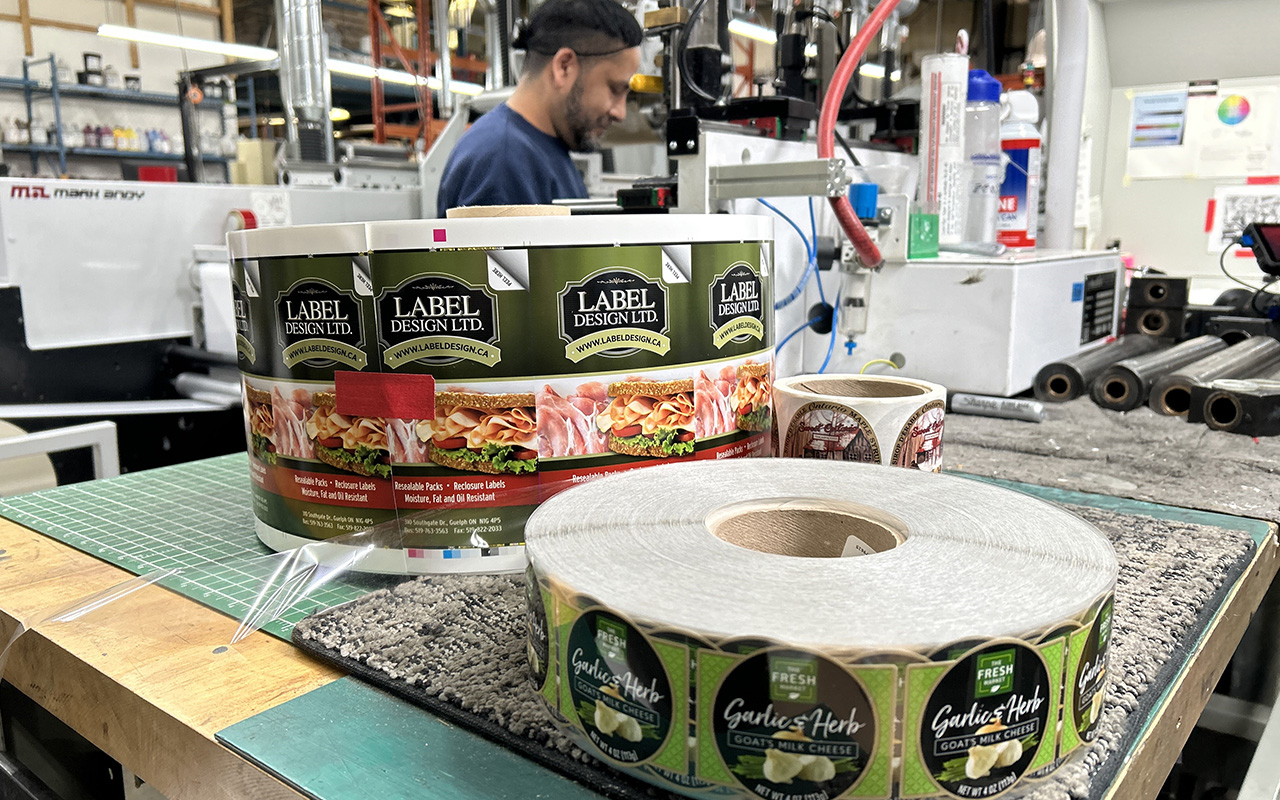
He continues: ‘The large majority of our customer base were mostly in that area, but we did obtain one large food processor which really grew the business. They called us on a Thursday afternoon with a very urgent need... we received the plates on a Friday night, we ran the product on Saturday and delivered them to their gate on Sunday morning, and from there this client grew to be very big. So it was one of those stories where you get an opportunity and you take it.
‘And from there we continued to grow until we built our own plant and moved into this location... better equipment, faster, more clients, larger clients, and we really started to focus on the food processing business and that's been our key to success.’
Manuel Garces, general manager VP at the company, runs the day-to-day activities at Label Design. He is a graduate of Queen’s University with an M.Sc. in chemical engineering and has spent his 20-year career alternating between flexible packaging and pressure-sensitive labels. Here, he echoes the point about Label Design’s broad client base: ‘We have customers in pretty much every space—household items, industrial applications, pharma applications. We have a heavy presence in the food markets; that is our core strength.’
Garces goes on to explain what he believes are the key reasons for his company’s success in this highly regulated field: ‘We have a very clean facility, we're the only company in Ontario that have the SQF Certification, which is the highest food certification a label company can get. Our process controls are second to none, we have an ERP system that controls the raw materials from the point they enter the building all the way through the customers, so excellent tracking, excellent quality checking, vision systems on every piece of equipment that we own.’
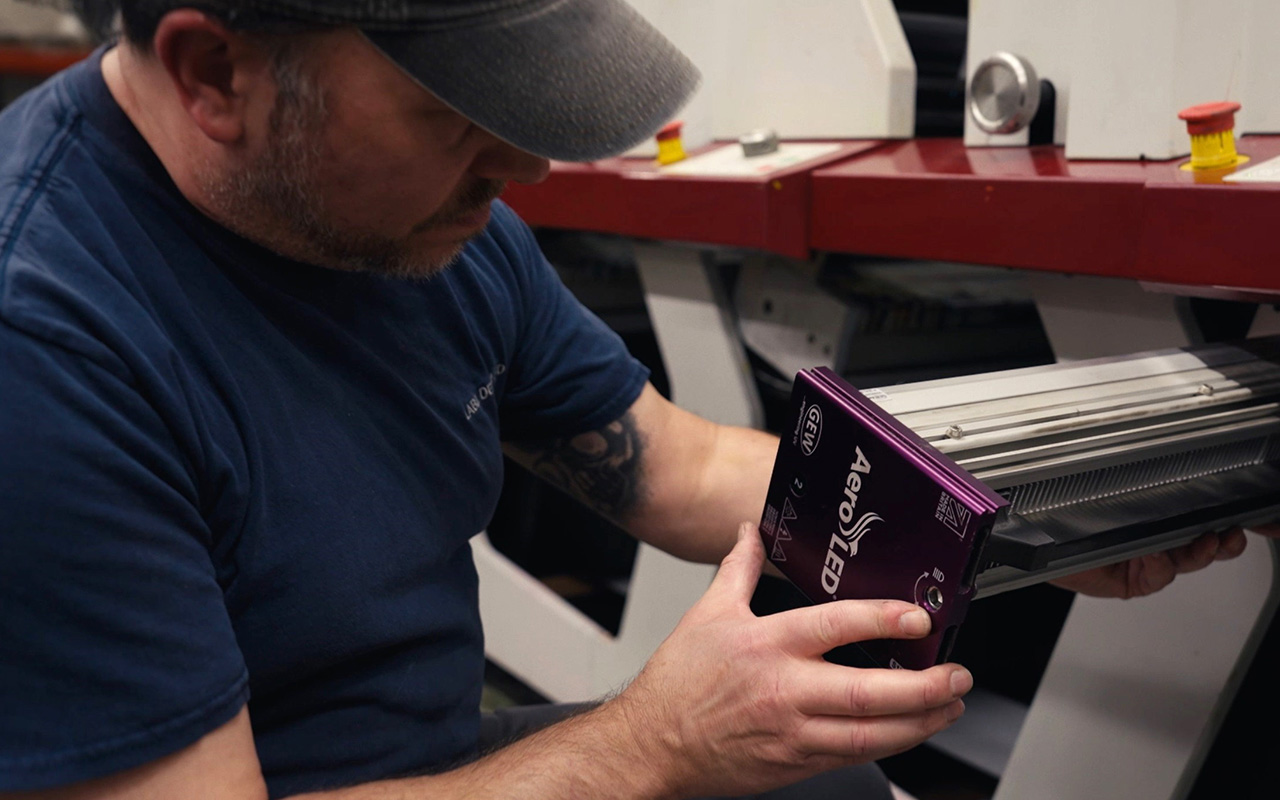
Oudesluys has been a driving force behind the company’s continual investment in the latest printing technology, which he considers to be critical to business success. He explains how this led to Label Design’s original investment in UV LED curing systems: ‘Several years ago we updated one of our presses and we added four or five stations with a UV system for curing inks. It greatly improved our quality especially on 4-colour process. At the time LED inks were up and coming, however when I did my research they were not meeting the requirements, especially on high-speed label presses, so we ended up staying with the conventional UV systems and within a year these ink suppliers had fixed the problems and LED was the way to go.’
Chris Glazier began with the company back in 2001 as a helping hand in the finishing rewind area. In 2007, he embraced a full-time position as a flexo press operator, marking the beginning of his connection with the production process. In 2022, he was appointed as plant manager, and his diverse experience has made him a great asset to the management team.
When UV LED curing was first trialed at Label Design, Glazier was not convinced of its worth to the business: ‘I was not completely sold into the LED when we upgraded into it; I wanted to do our testing. We're 90 percent food, so I really wanted to make sure that everything is curing and anchoring properly when it gets out to the market and our customers are very happy and satisfied. We also use a lot of different coatings, so I wanted to make sure a lot of the coatings that we use are also compatible. That's why we started with three systems to work with the LED, to make sure all our R&D is done properly and everything's working.’
By using GEW’s ArcLED technology, whereby lamphead cassettes can quickly be interchanged between UV Arc or LED on any print station, Glazier’s team were able to introduce LED to their production process in a risk-free, measured fashion. This also means that any print or coating station can be reverted to conventional UV in a matter of minutes, as he explains: ‘It gives me the versatility between LED and UV, so if there's a product they don't have in LED right now, I can still use my UV system and it gives me my security within that market to stay with UV until we're confident 100 percent. Because we were already a UV shop, the transition to LED was seamless... color, anchoring, everything... you would never know; it's been that close.
‘I wanted to make sure both of my presses were compatible and that was a big part when we upgraded with GEW and that was another thing I liked, that their parts were very interchangeable, so I use both presses and both LEDs so I have three on each press and I interchange, so sometimes when we're doing R&D I can put six LEDs on one press to make sure it's doing everything that we expect, if not more. So I can do LED UV at any time, in any station.’
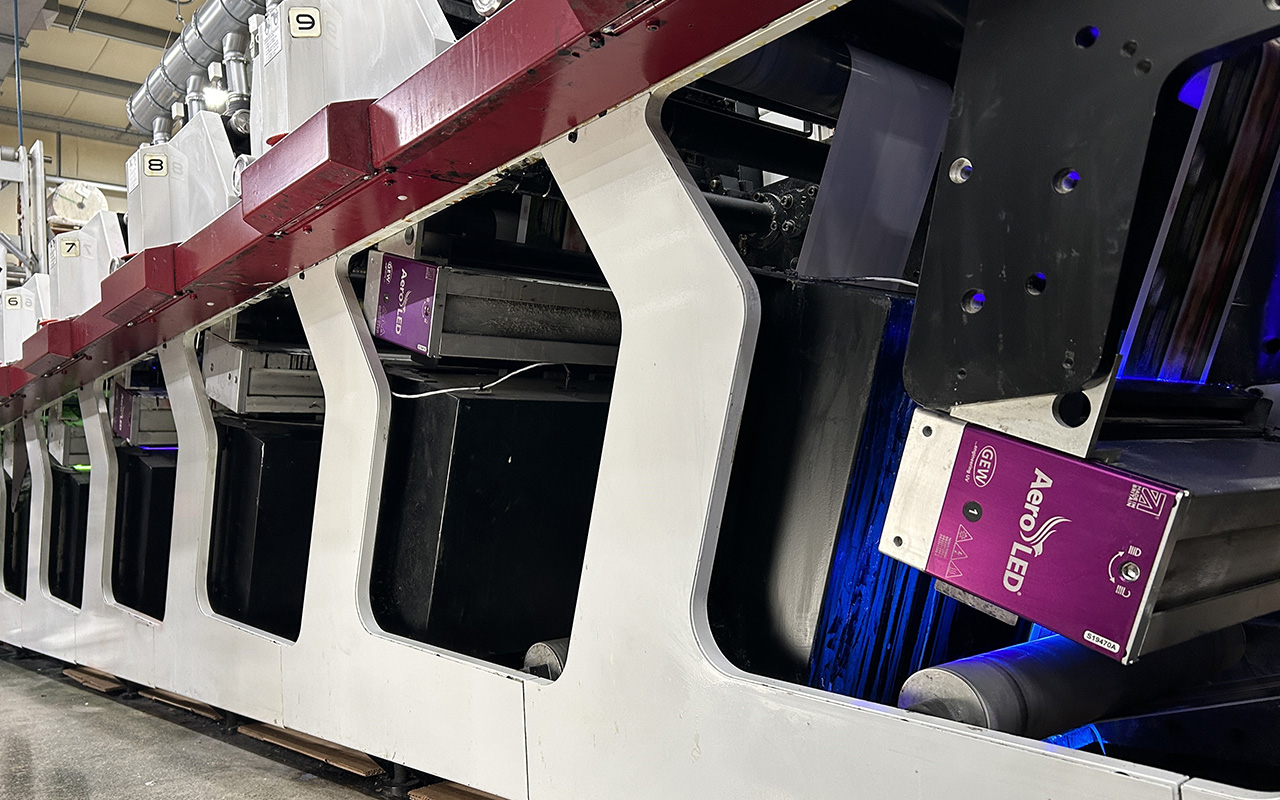
Glazier goes on to extol the benefits of ArcLED: ‘The great thing about this system is the quick change, it's within minutes. When we had our old system, when the operators had to switch over from product to product, they could be hours changing the system depending on where the coatings need to be, or the adhesives had to be. With the new upgrade with the LED, they're up and running within minutes with the quick changeover system. It's been nothing but fantastic, and we've seen a large production increase.’
LED is known for curing effectively with opaque whites and stronger colors, as Glazier has also found: ‘One thing I do like about the LEDs is it does cure deeper colors than the UV, which before when we really needed to get that strong color in the UV, we sometimes had to drop down to a water base to pull that strength because we just couldn't get it to cure properly, where LED is hitting that marker for us.’
Glazier also addresses the subject of the cost of LED-curable inks: ‘A year ago when I was looking into it, LED was a little more expensive but I think as LED is starting to become more and more available, more people are using it, it's rating competitive with UV. Ultimately, we want to save costs so we can be competitive within the market, and that goes down to maintenance and energy, and ultimately, you have the benefit of helping the environment and doing a lot of good things on that side of things.’
Garces highlights how these energy savings are not only a benefit to Label Design; they are also a marketable entity to his clients: ‘Sustainability is one of our core commitments. I'm out there talking to customers, and that's always important to me to make sure that the customers know that we are continuously improving our operations; we can actually bring a technology that allows us to use less energy.
‘All of my major customers are asking us to be more sustainable, to provide evidence that we are sustainable, to use sustainable label technology, so I think this really helps build the case for our customers and to help them with their goals.’
Garces concludes: ‘Customers know and appreciate the fact that we have that technology in-house and they see that as a factor in their decision-making process when they give business to Label Design... absolutely.’
GEW promote the fact that they offer ‘turnkey solutions’ to customers, meaning that the design and subsequent installation of every UV curing system are carefully planned and executed to minimize disruption and press downtime for the customer. Glazier outlines his experience of this: ‘Installation day, it was seamless, they said it was going to be eight hours each press, they beat that time and it was probably around six. They stuck around and made sure it was running to optimal and then they worked on the next press. It was an add-on, where they're just attaching to it. Again, the system uses very little power so I didn't have to bring any more power into the press, they just tapped into it and did a few little add-ons, and it was up and going in six hours, so my afternoon shift was up and running... we didn't even know we switched things over.’
Glazier rounds up with his thoughts on whether UV LED was the right move for the company: ‘Being hooked into GEW for 10 years, they were a front runner when we were looking at other suppliers and getting this system done. Their service has been fantastic, it's been remarkable. I don't know why we didn't do it earlier, it has made such a huge change to our company. If we would have done this two years ago, we would be talking that I have a full LED shop now. Do it, get into it... there's nothing better than saving money and helping the environment at the same time.’
For further information on GEW’s latest air-cooled UV LED system, AeroLED2, click here.
For more about Label Design, visit www.labeldesign.ca
Stay up to date
Subscribe to the free Label News newsletter and receive the latest content every week. We'll never share your email address.