Rotary die cutting for the future
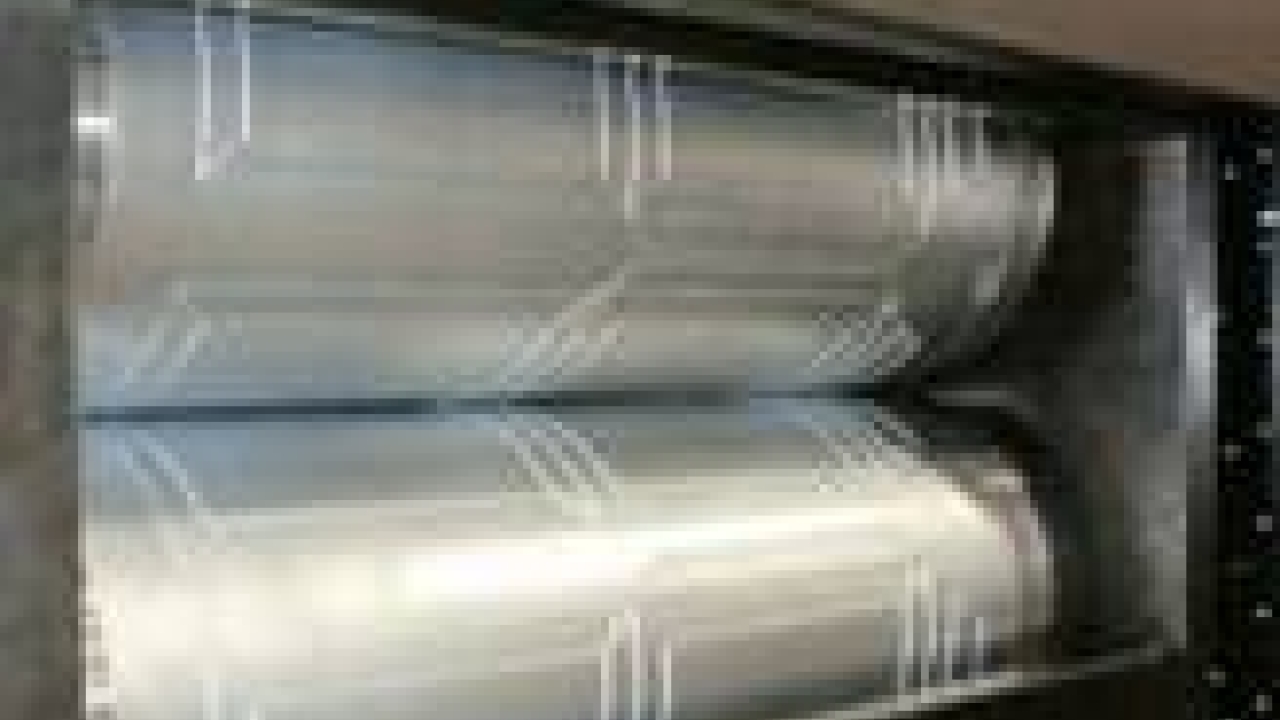
Steve Lee, vice president of technology at RotoMetrics, and James Wellsbury, the rotary tooling specialist’s packaging business development director, discuss rotary die cutting innovations to meet new consumer goods packaging challenges
Global markets for converted carton and flexible packaging continue to drive technology development across the supply chain. Forecasts of strong demand for more convenient packaging solutions for processed food, fast-moving consumer goods (FMCG) and pharmaceutical and medical products are driving moves to new rotary converting solutions, including innovation in die cutting technology.
While overall growth rates for carton and flexible packaging in the mature markets of North America and Europe will be modest at 2.5-3 percent year over year through 2015, new rotary converting technology will quickly emerge with cost-effective solutions for niche applications with much more rapid market growth. Technology development is already focused on applications such as resealable packaging, flexible carton packaging for liquids and improved barrier packaging for extended shelf life.
Consumer driven demand for more convenient food packaging will lead to the use of more costly films for extended shelf life.
Demographic trends towards more single person and empty nest households will also accelerate demand for smaller serving sizes and more on-the-run meal and drink packaging, The fastest growing markets for converted flexible packaging will be beverage, meat and related products, and snack foods. Today’s consumer is also looking for more environmentally friendly packaging solutions as opposed to traditional rigid plastics.
Good examples of the trend in individual serving food packaging are the growing markets for sandwich and salad packaging. In the UK, for example, prepared sandwiches represent a large and growing market. In 2010, 11.5 billion sandwiches were consumed and the market forecast to grow at four percent per year. Nearly a third of that market, and the most rapidly growing segment, is the sealed sandwich to go, often packaged for vending delivery. Along with sandwiches, refrigerated salads, pasta and noodle trays are rapidly filling retail shelves and represent a significant market to migrate from plastic to carton packaging.
In the medical and pharmaceutical markets, companion trends toward unit-of-use packaging, greater product visibility and higher barrier requirements also demand new converting solutions.
Rotary technology vs flatbed converting
For many years carton packaging has been converted using flatbed die cutters with steel rule dies. This process utilizes between three and five steps to convert a folding carton. One can recognize a box that has been cut using flatbed tooling, as there will be visible ties on the edge of the box, which function to control the box during the converting process.
With higher volume demands, e.g. production runs of 500,000 to one million boxes, solid rotary male/female creasing dies offered a viable solution. The high unit volume was the driver to achieve a reasonable payback on the sometimes expensive solid tooling.
The development of magnetic cylinders and flexible cutting dies in the early to mid-1980s offered a leap in technology from reciprocating flatbed die station and steel rule dies. The quality of flexible dies has continued to improve while at the same time flexographic and UV flexo technology has advanced to rival the print quality of offset methods. Today, rotary pressure cutting with squared blades squeezing material from the top and bottom, causing paper fibers to burst, is available for long run production of liquid packaging and other high-volume carton applications.
Rotary die stations and in-line processing with flexible dies combine to deliver dramatic improvements in converting speed, material throughput and process efficiency.
Rotary die cutting for sandwich and food packaging
The new requirements for quicker delivery of innovative barrier packaging for sandwiches and other food items play to the strength of rotary converting. Flatbed production is now replaced with one-pass, raw material to finished product manufacturing at speeds of 150m/min.
Manufacturing savings are measured in reduced man hours, quicker processing times and reduction of make-ready costs. Rotary processing generates significant material savings compared with sheet-fed lithography. The ability to nest and stagger product on rolled stock allows up to 95 percent material usage, a 15-20 percent waste reduction versus traditional flatbed processing.
Rotary converting reduces a prior value chain of up to six manufacturing processes to just one. Let’s take the example of sandwich packaging. Once the web/card is printed, it will travel into a first die station in reverse where the window is cut and waste removed by vacuum. The die cutting can be accomplished by either solid or flexible die technology. Both solid and flexible dies are cutting in these applications against core-hardened anvils. For longer run applications, solid dies provide the best value. New deep blade flexible dies combined with high-strength magnetic cylinders have narrowed the performance gap and can offer value when shorter runs and quicker changeover are required. Flexible dies used in this first window station also allow a converter to quickly customize packaging in response to new customer requirements.
Subsequent to the first die cutting operation, the card stock is laminated and UV cured, and travels conventionally into a second die station where the reverse crease or conventional male/female creasing is done to give the pack its folding ability. Again, both solid and flexible dies can be used for this operation. The laminated stock next travels to a third die station for the outer or final cut. Solid or flexible cutting die technology is applied to this final operation. After final cutting the finished product is shingle stacked.
Rotary converting and the related cutting die technology enable the proliferation of retail options for customized packaging of sandwiches and individual serving food portions.
Rotary pressure cutting flexible dies
RotoMetrics has introduced a further innovation in flexible die technology for carton converting applications; rotary pressure cutting (RPC). RPC is an alternative to crush cutting that is being run today for folding carton, drinking cup walls and new liquid packaging applications.
The development of RPC flexible die technology responds to customer demand for more flexibility in production, reduced set up times and cost savings in tooling. Typical segmented solid dies can take 8-12 hours to make ready for cutting, while RPC flexible dies can be loaded and made production-ready in 1-1.5 hours.
RPC technology is different from traditional crush cutting where a sharp blade crushes through the material against a solid anvil. In RPC, the dies have flat cutting edges and burst the material as they squeeze from both the top and bottom.
In addition to reduced make-ready times, converters achieve significantly longer die life with rotary pressure cut technology. In traditional crush cutting, wear on the sharp cutting edge is the limiting factor in die life. Without the edge wear seen in crush cutting, RPC dies run for millions of revolutions before needing to be replaced.
With greater pressures being applied in the RPC process, a robust die station design is also required.
The modular die stations developed by RotoMetrics feature thicker side frames, larger rolls, heavy-duty pressure systems as well as mounting devices for quick die changeover.
Customers are running RPC flexible dies today on the full spectrum of carton applications, including the new liquid packaging formats. The combination of reduced tooling costs, faster changeover times and longer die life confirms the real world value equation of the new technology.
Die cutting technology will continue to provide solutions as global brand owners respond to the demands of new generations of consumers with innovative technologies (e.g. programmable LED, luminescent and temperature responsive labels) and more customized product packaging solutions.
Stay up to date
Subscribe to the free Label News newsletter and receive the latest content every week. We'll never share your email address.