HP raises speed bar with new in-line technology
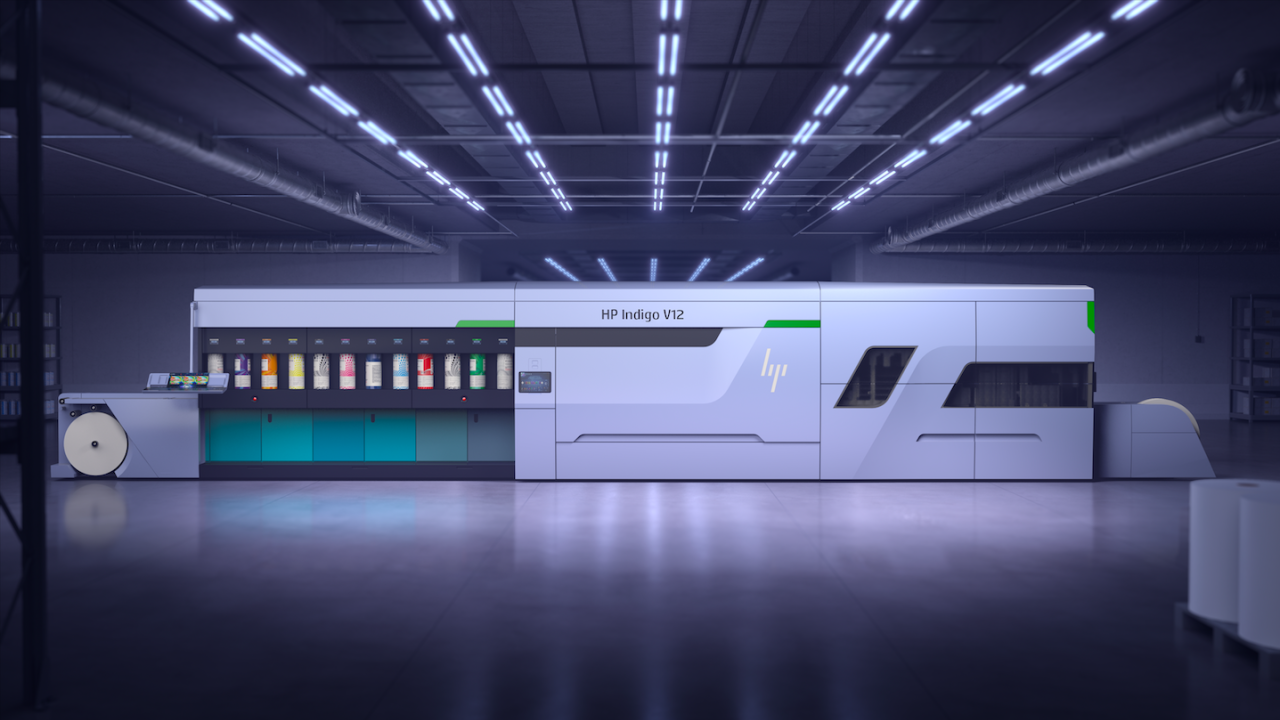
The new HP Indigo V12 digital press will print at 120m/min (400ft/min) without requiring the dual engine format of the 8000 series. It is the first time HP Indigo has implemented its new LEPX in-line technology platform, which replaces the intermittent central drum design which powers all other HP Indigo label presses.
‘This is a complete departure from our existing architecture and unleashes the speed inherent in the LEP process,’ says Yogev Barak, head of strategy and business management at HP Indigo. ‘Everything customers are used to working with is built into this technology, but now they can do it in a more productive way.’
The HP Indigo V12 press has six color stations running simultaneously, each of which has access to two color channels for a total of 12 colors accessible. The 12-color capability would allow a converter to load up, for example, with a 7-color extended gamut ink set plus white, silver and three specialty security and special effect inks.
The HP Indigo V12 press also incorporates HP Indigo’s High Definition (HD) imaging technology, with a new LED writing head doubling print resolution to 1600 DPI. This improves smoothness, and enables finer vignettes and security features and more accurate Pantones to be achieved.
The HP Indigo V12 will print on a wide range of substrates from 12 micron film to 450 micron (18pt) board, supporting pressure-sensitive labels, shrink sleeve labels, flexible packaging, tubes and IMLs. Workflow automation is a key focus, including HP Indigo’s new Spot Master automated color management system (see information box right).
Looking in more detail at the new LEPX in-line press configuration, we can see how different it is from – and the similarities to – the existing central drum LEP platform.
Each of the six print stations is fully self-contained in terms of imaging laser, dual BID ink dispensers and PID (photo imaging drum). Rather than being wrapped around a central drum, the blanket is now a continuous web which moves between the print units picking up 6 colors in one rotation or up to 12 colors in two rotations. When the image is fully built up on the blanket, it is transferred to the substrate. In that sense it remains the same ‘one shot’ process as the existing LEP technology.
A technical challenge has been to maintain perfect registration between the print units and the moving blanket. This has required development of specialist algorithms and control mechanisms which formed a key part of the 5-6 year long LEPX development program.
The HP Indigo V12 press will not replace the current HP 6900 narrow web press. Rather, says Alon Bar-Shany, general manager, HP Indigo, the HP Indigo V12 is targeted at mid-to-long run jobs, and the click charge model will be adjusted to take account of this. The HP Indigo WS6900, and its successor the 6K will continue to be sold for short-to mid-run lengths. Bar-Shany sees the combination of the 6K and HP Indigo V12 as freeing up flexo presses for really long runs, increasing press uptime.
HP is working with its OEM partners to develop finishing systems for the HP Indigo V12, which shares the same 13in/330mm format as the existing 6000/8000-series. First out of the gate is HP Indigo’s long-time partner AB Graphic, which has developed a non-stop high-speed finishing line for near- and in-line operation.
Yogev Barak says HP Indigo currently has a list of label converters waiting to take the HP Indigo V12 press for beta trials, which should begin to take place next year. The press is expected to be commercially available in 2022.
‘We have really focused on the label market with the HP Indigo V12 in terms of width, number of colors, media versatility, automation and finishing,’ says Alon Bar-Shany. ‘We will see at a later stage where the technology will go next.’
‘K’ series introduced
As well as introducing the HP Indigo V12 press, HP announced new model names and configurations for its existing labels and packaging production presses.
The new press range is designated ‘K’ and includes the HP Indigo 6K and 8K digital presses for labels, the HP Indigo 25K for flexible packaging and labels, and the sheet-fed HP Indigo 35K and roll-to-B1 sheet HP Indigo 90K for folding cartons. ‘Value packs’ with various upgrade options will allow the existing customer base to benefit from the new features and capabilities introduced on the new presses.
The HP Indigo 6K digital press is the new model of the highly successful HP Indigo 6x00 series. Like all the new ‘K’ series presses, it comes fitted as standard with a range of new capabilities including Spot Master color automation.
The press will have access to the full range of new HP Indigo ElectroInks including higher opacity white for shrink sleeves, silver, fluorescents, invisible yellow, orange and green for brand protection applications and new high-durability varnishes. The 6K is also fully compatible with HP Indigo’s emerging suite of digital embellishment equipment, now including the in-line Kurz DM-Jetliner digital metallization, ElectroInk Silver for metalizing the color gamut and the GEM single-pass digital embellishment unit.
The HP Indigo 25K digital press replaces the mid-web 20000. It can be fitted with a new label slitter which allows converters printing PS labels to slit to the width of their existing narrow web finishing equipment. The press is fitted with Spot Master color automation, two white ink stations and a bigger print frame – 737mm compared to 729mm for the 20000.
Along with the Karlville Pack Ready thermal laminator, HP Indigo has expanded the range of flexible packaging finishing options with the new 800mm-wide SuperSimplex e800 solventless laminator designed and built by Nordmeccanica. HP says this offers ‘low waste and reduced energy consumption’ for on-demand pouch production.
‘The Nordmeccanica system is targeted more at flexible packaging converters looking to introduce digital print operations and wanting to leverage their existing expertise in water-base and solventless lamination,’ explains Yogev Barak. ‘The Karlville Pack Ready thermal laminator with Pack Ready requires less of a learning curve, and has therefore proved popular with label converters moving into flexible packaging for the first time.’
With the increasing focus on sustainability, HP Indigo’s ElectroInks have now been certified with the ‘OK Compost’ Green Leaf mark from TUV Austria, which verifies they can be used as printing inks for packaging which is recoverable through composting and biodegradation.
The HP Indigo 6K, HP Indigo 8K and HP Indigo 25K presses will be commercially available towards the end of 2020.
Stay up to date
Subscribe to the free Label News newsletter and receive the latest content every week. We'll never share your email address.