Ink systems
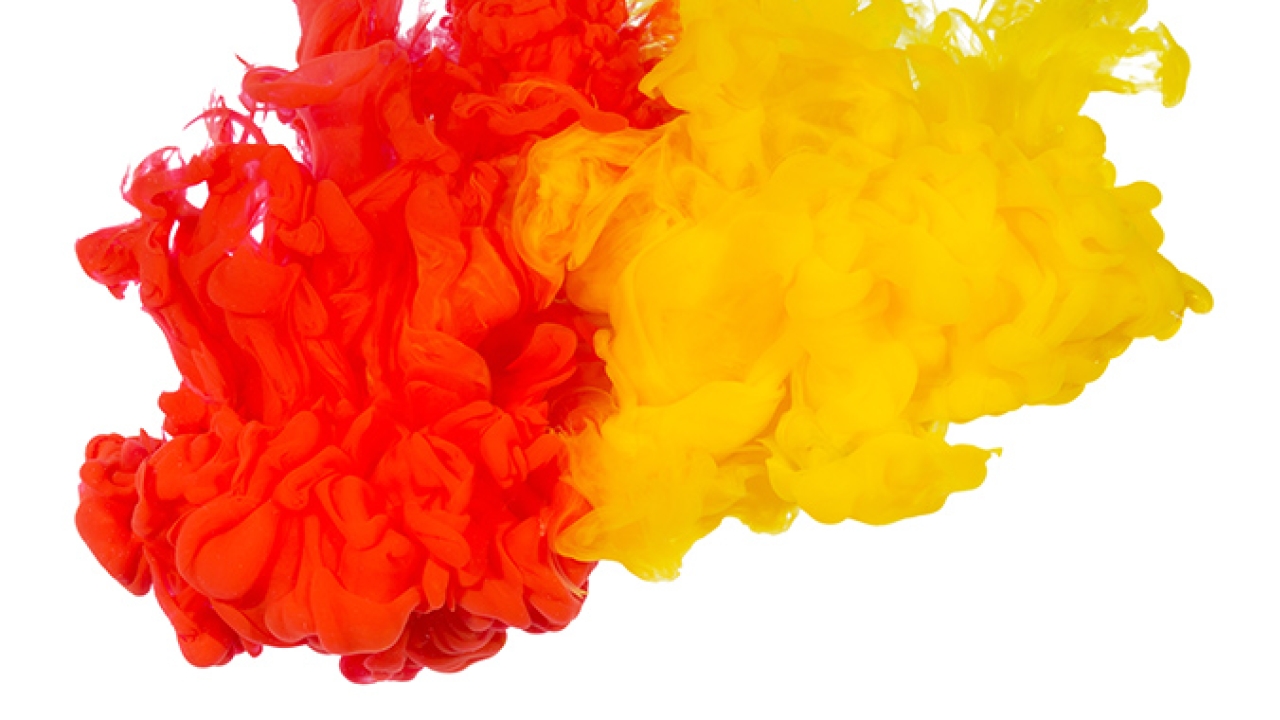
Inks can be classified by the diluting media used, which creates the ink’s viscosity characteristics. There are four types of diluents: solvents, water, oil and acrylic monomers. The respective ink’s drying mechanism is closely linked to the solubilizing media used.
Solvent-based inks contain highly flammable solvents. When ink is heated in a drying tunnel, the inks release the solvent (up to 60-70 percent) through evaporation.
Water-based ink contains around 40-50 percent dry content which is not water soluble, which is why the ink film can be made water resistant. When the ink is heated, the solution of water/amine/ammonia – and a small amount of solvent – is evaporated as the ink dries.
Oil is used mostly in offset and letterpress inks, and this type of ink dries using a combination of evaporation and oxidation.
The other major class of inks are UV curable, which cure via a polymerization process that results in a 100 percent solid. The main diluting agent here is acrylic monomer, used in different proportions in different types of UV inks. No solvents evaporate in the drying process, which means, for example, that a flexo UV ink uses approximately 20 percent less ink with the same anilox as water-based or solvent-based inks.
Offset
In offset, the inks start as a paste which is broken down into a film via a series of rollers. A second set of rollers bring in a water solution and both ink and water are applied to the printing plate. The plate surface is either water repellent (phobic) or water accepting (philic). The ink is transferred to a rubber blanket and then to the substrate.
Letterpress
The letterpress principle is similar to offset, in that a paste ink is broken down by a series of rollers to make a consistent film which can be used to ink a plate. The difference is there is no water solution involved. The ink is applied directly to raised dots on the plate, from where the ink is transferred directly to the substrate.
Flatbed and rotary screen
In flatbed screen, a thinner, more liquid ink is forced through holes in a mesh relating to the image to be printed. With a rotary screen the mesh rotates around a fixed squeegee, but the principle is the same.
Flexo
Flexo starts with a liquid ink, which is poured or pumped into an ink pan. A metering roller transfers a film of ink to the anilox roller, which is engraved with a cell structure designed to hold a defined volume of ink. These cells transfer the ink to raised dots on a flexible plate, which transfers the ink directly to the substrate. An angled doctor blade in contact with the anilox surface removes excess ink outside the cells, allowing a precise amount of ink to be transferred to the plate.
In modern presses a trend is to use a chambered doctor blade unit. This eliminates the need for an open ink pan. The ink is pumped into a sealed chamber which incorporates two doctor blades.
Gravure
The gravure process produces a print from an engraved cylinder and has traditionally been the higher quality process for flexible packaging and shrink sleeve labels. It lays down more ink than flexo, and not only inks but also metallics, release lacquers and cold seal can be applied. Printing speeds are typically between 120m/min to up to 300m/min and the usual configuration is printing stations in-line.
Solid vs evaporation
Inks dry either by evaporation or curing to a solid film. Where solvent or a water-based solution is used as the pigment carrier, up to 80 percent of the ink evaporates during the application and drying process. UV ink by contrast, cures to a 100 percent solid and there is no evaporation.
In solvent inks a resin or binder is dissolved in the solvent. The function of the binder is to grind and wet the pigment and form it into a homogenous mixture. Additives may be used to enhance the properties of the ink. When the ink is dried on the press using IR or hot air blowers, the solvent evaporates, leaving a dry ink on the substrate.
In water-based ink the resin is not water soluble. It is made water soluble through use of amine or ammonia. When that resin is dissolved the pigment can be ground in to form a film. Once again, different additives can be used to enhance the performance. When the ink dries, both the resin and the amine evaporate – otherwise the print would never be water resistant.
In oil offset-based inks a mineral oil or vegetable oil is used as a diluent and then different types of resins are used. When the ink is heated, the water and ammonia mixture evaporates, the binder particles soften and a dry film is formed. In fact, oil-based inks dry in a combination of ways, not only with heat but also by reaction with oxygen, which is a chemical process.
Pigment-based UV inks contain high viscosity pre- polymers or low viscosity monomers. There are no solvents, and the monomer acts as the diluent.
The ratio of diluent will vary depending on whether it is, for example, a flexo, screen or offset ink because each has a different viscosity.
UV curing process
UV inks are available for the offset, flexo, letterpress, inkjet and screen processes. The principle additive in a UV ink is a photoinitiator. When activated, this monomer starts a cross-linking process which turns the ink from a liquid into a solid film. The cross-inking process is activated by exposure to a UV light source.
Unlike water- or solvent-based inks, UV inks can be left in the ink pan without evaporating, though care must be taken to ensure they are not exposed to a UV light source.
Inside the UV lamp is an elliptical or a parabolic reflector which directs the light to the surface of the ink (see Figure 2). The photoinitiators react to the UV light, which starts the polymerization process and dries the ink.
Oxygen at the substrate surface inhibits the cross linking and curing process. This effect can be minimized by introducing an inert gas, typically nitrogen, into the area where curing takes place.
UV LED
The light source for a conventional UV lamp is a mercury-doped lamp which emits radiation across a broad spectrum. With UV LED, the inks are sensitive only to a very narrow wavelength of UV light. While a conventional mercury UV lamp will radiate energy from 220 nanometers (nm) to 400nm, UV LED lamps emit a narrow range of peaks at 385, 395 or 365nm.
Electron beam
Electron Beam (EB) curing inks are similar to UV inks. They use similar resins and binders and cure from a liquid to a 100 percent solid. The key difference is that EB inks do not require photoinitiators. They cure by bombarding the substrate with electrons, which starts the polymerization process. EB involves printing wet-on-wet with final cure at the end of the press line, whereas UV is wet-on-dry, with inter-station UV curing required.
Combination print requirements
As we noted earlier, narrow web printing is defined by the ability to combine multiple processes in-line. This makes it critical to ensure that subsequent inks will key to the previous decoration or ink layer.
A particular challenge is printing on top of an oil-based ink with a UV ink or coating. Converters also need to be aware of different types of reactive agent or additive used in different ink types. Trying to mix another resin type or water-based ink or coating over UV also adds to the complexity.
Digital inks
The rise of digital label printing over the last four decades, accelerating rapidly over the last four to five years, now makes digital a mainstream narrow web print technology.
There are three main technology streams: dry toner, liquid toner and inkjet, with inkjet in turn sub-divided into the standard ink categories of water-based, solvent-based, UV/UV LED-based, and most recently EB.
Ink adhesion
The most challenging substrates to achieve ink adhesion are synthetics. There is a delicate balance to getting an ink that has both enough possibility to flow out, or whet out, on different types of surfaces, but also create a strong bond to the substrate.
Films are comprised of several layers, depending on the application, and it is crucial to understand the properties of the surface layer to ensure there is correct ink anchorage. For filmic substrates corona treatment is usually required. The substrate is exposed to an electrode which increases surface tension by changing the polarity of the substrate surface, making it easier for the ink resin to adhere and creating a better bond strength.
Without this the ink will tend to stay in a ‘bubble’ on the surface.
For converters printing on films it is important to have corona treatment in-line, despite the fact the material has already been corona treated by the supplier. The problem is that corona treatment starts to deteriorate – so lose surface tension – over time, due to the ‘memory’ characteristics of film.
Surface tension is measured in dyne levels, and converters should ideally invest in measuring equipment, which can range from a handheld pen to laboratory scale devices. Achieving surface tension levels recommended by the ink supplier is a critical QA check, but note it is not a guarantee that perfect adhesion will be achieved every time.
Inkjet
Inkjet accounts for a growing percentage of digital press installations. The chemical composition of inkjet inks is similar to conventional inks, in that the main components are the colorant and carrier fluid. The colorant, again, can be a pigment or a dye and the carrier fluid may be aqueous, solvent or oil-based.
Digital inkjet inks include the same broad categories as conventional inks:
- Aqueous inks, where the carrier fluid is water. These inks are used in printing onto coated substrates where the water is absorbed quickly into the coating and the dye or pigment is fixed to the surface of the coating to give a sharp defined image. Printing onto label films requires a specialist coating which can be applied by the substrate manufacturer or in- or off-line by the label converter.
- UV inks represent the fastest-growing segment of the narrow web label printing ink market. The curing chemistry is exactly the same as in conventional UV, with ink cured into a solid when photoinitiators interact with a high intensity source of ultraviolet light. Ink chemists have recently made progress in low migration (LM) UV inkjet inks in conjunction with nitrogen-inerted curing systems, where oxygen is excluded from inhibiting the reactive ink components by a nitrogen blanket.
- UV LED inks are also making an impact. LED lamps were used originally for inter-station pinning, to stop the ink drops spreading before final arc-lamp curing to improve print quality. We are now seeing the introduction of fully UV LED cured digital presses. Hybrid digital/flexo presses allow the use of both arc and LED lamps in the same press line. Typically UV LED is used to cure the more opaque conventional inks, such as White and Black.
- Solvent inks use a solvent as their carrier fluid and dry very quickly through evaporation. They are considered environmentally unfriendly but the durability of the final product means they are still used for printing some outside label/POS applications on wide web inkjet printers.
- Electron Beam engines have recently been miniaturized to allow fitting onto a narrow web inkjet press. The EB inks do not require a photoinitiator and so are considered food safe.
Another class of inkjet liquid media are the so-called ‘functional fluids’, for example where metallic or conductive fluids are printed to form electronic components and circuits. In this case the functional fluid consists of nanometer-size particles of conductive metals such as silver and copper held in suspension in a carrier fluid. Once printed these inks are then sintered, enabling the printing of conductive tracks for electronic components and circuits.
Other functional fluids include coatings such as spot gloss and matte varnishes, which are now available both as in-line and off-line alternatives to flexo plate varnishing.
Performance requirements
Although inkjet inks are broadly similar chemically to their conventional counterparts, the physical characteristics and performance requirements are totally different.
Inkjet is a non-contact print method where inks are jetted through ultra-fine nozzles which must not become blocked. The ink drops must be controlled at the nozzle, during its flight trajectory and then during landing on the substrate.
With drop-on-demand inkjet systems the printhead works by using a small amount of energy in each nozzle to eject a drop of ink. This breaks the ‘meniscus’ at each nozzle (the curved surface of the ink formed at the nozzle orifice by surface tension). The drop is held back in the nozzle by a slight negative pressure until the energy pulse is applied.
The ink supply system ensures that the correct negative pressure in the system is maintained, while ensuring that the printhead does not get starved of ink when printing. Too little ink, and gaps will appear in the printing; too much ink, and the nozzle plate might get flooded, causing irregular jetting, again compromising print quality.
The ink supply also filters the ink to minimize the chance of particles clogging the nozzles; it might also de-gas the ink to remove air bubbles, and heat the ink to ensure that it is at the right operating temperature. Ink recirculation printheads will continuously circulate the ink through the printhead to help avoid clogging.
Ink additives provide the specific performance qualities required for non-contact printing, and will include:
- Surfactants to control the surface tension of the ink drop
- Binders formulated to improve the elasticity of the ink
- Dispersants to aid the dispersion of the colourant in the carrier fluid.
Formulation challenges
Challenges which have to be overcome in manufacturing UV inkjet inks include:
- Low viscosity, which limits the use of oligomeric, resinous or multi-functional species in the formulation
- High stability – for example no settlement on storage. Effective dispersion and stabilization technology is of critical importance, because in a low viscosity liquid there is a tendency for the particles to agglomerate, or stick back together. Pigments are also subject to gravitational settlement
- Small particle size (generally less than 1mm), which puts further restrictions on usage of certain pigment classes including metallics and special effects pigments such as thermochromics and piezochromics.
Strict demands are also placed on surface tension values; these should be sufficient to allow appropriate wetting on the print-head face-plate material, while helping meet print quality specifications through ink spread on the media. As the volume of each drop ejected from a piezo DOD print-head is typically under 100 nanograms, these drops are strongly affected by the chemistry of the ink’s components.
The sensitivity is such that even additives at low level, such as surfactant, can influence how the drop breaks up, its length of tail (ligament) and its likelihood to form satellites (smaller drops that form from the break-up of the initial drop). In turn, the latter can have a major impact on print quality.
Formulating stable low viscosity white UV inkjet inks can be difficult due to the high density of typical titanium oxide and zinc sulphide pigments.
To achieve good application of inkjet onto a substrate the surface energy is very important. This needs to be achieved either by pre-coating or by corona treatment, in which cases adherence has been demonstrated to be as good as with conventional inks when using rub resistance tests on most substrates used for labels
Because inkjet inks are chemically similar to conventional inks it should be possible to print on broadly similar substrates without providing additional top coatings. Substrate suppliers are working with inkjet head suppliers to optimize an ever-growing range of inkjet qualified substrates. In practice, however, to maintain a color-managed workflow, pre-coating of UV inkjet substrates can be beneficial.
Electrophotograhic inks
The largest installed base of digital presses use the electrophotographic imaging principle, printing with toners, either ‘dry’ and bonded by heat, or suspended in a liquid carrier. The pioneers of this technology for the narrow web market in the 1990s were Xeikon for dry toner and Indigo for liquid toner. While dry toner-based systems are not strictly ‘inks’ (having no vehicle/carrier), the Indigo system displays many of the key characteristics of an ink while still being based around the principle of charged particles.
Called by the company ‘ElectroInk’, the HP Indigo technology involves suspending electrically charged pigment in a mineral oil-based liquid. The particles, 1-2 micron in size, are attracted to the charged areas on a photo-imaging plate (PIP), imaged by laser.
Each color separation is transferred to a blanket, as in litho offset, ensuring the final print maps to the natural contours of the substrate, preserving texture and gloss uniformity. The ink is dried on the thermal blanket, and not on the substrate. This removes heat stress from the substrate, enabling a wide media range to be employed.
The full color image is built up on the blanket before being transferred in one hit onto the substrate, so there are no issues with dot gain or registration.
In order for the ElectroInk to key to the substrate a special primer is required. This can either be pre-coated by the substrate manufacturer or applied off-line or in-line by the converter.
For more information about the Label Academy, and to order book, go to www.label-academy.com
Stay up to date
Subscribe to the free Label News newsletter and receive the latest content every week. We'll never share your email address.