One world, one Bobst
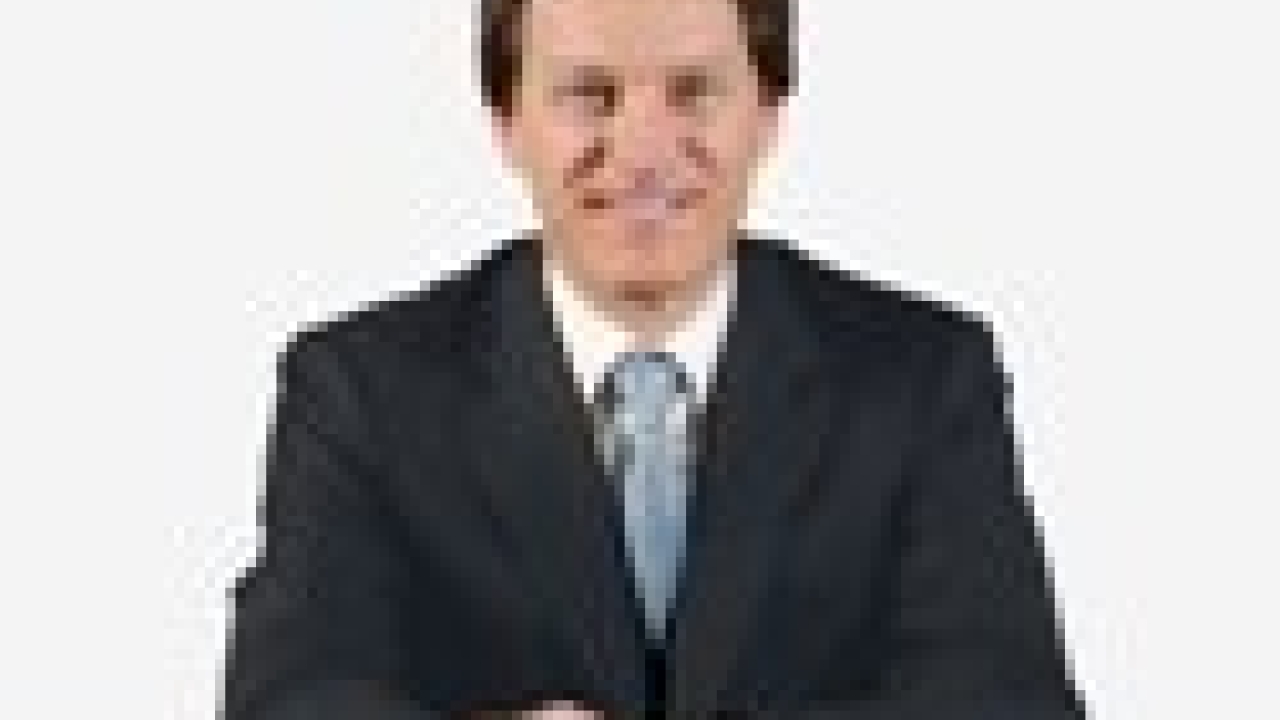
Stating that all products will now come under the one brand name, Bobst says developing new technologies for the benefit of customers remains the main driver of the Group
Stating that all products will now come under the one brand name, developing new technologies for the benefit of customers remains the main driver of the Bobst Group, according to chief executive officer Jean-Pascal Bobst (pictured, top).
Drupa 2012 will see the company showcase unique technology advances including:
- quality control devices that check 100 percent of customers’ production, whether it is the print on a carton or the density of a metalized film
- color matching systems that make setting a press an off-line process
- and new approaches for existing systems which reduce process waste, improve net production, or cut make-ready times by 10 percent or more.
Flexo presses
Drupa will see the new Fischer & Krecke 20SIX flexo press equipped with the latest smartGPS version. It can be customized to meet all flexible packaging requirements and scale of production from long to very short jobs. A 10-color 20SIX flexo press will be on working demonstration for the duration of the show at Bobst’s Technology Center in nearby Bielefeld.
Bobst will also show the new smartCOL, a revolutionary color matching system that continues the philosophy of “smart” off-line set-up approaches for CI flexo presses. Combined with smartGPS, it enables a variety of flexo print designs to be prepared off-line to avoid set-up waste and increase press up-time.
Gravure presses
Two Rotomec units will be on display: the Minimum Waste (MW) press in a new configuration with internal washing dedicated to ultra short-run production; and the well-established high-speed Rotomec 4003HS press.
A brand new configuration of the Rotomec 4003HS, for shaftless cylinders, will be on working demonstration at the Rotomec Technology centre in S. Giorgio Monferrato, in Italy for the duration of the show. This machine is equipped with the twin trolley system that improves the logistics of inks, and reduces make-ready time and waste. The integrated Performance D LEL also reduces maintenance operations.
Digital presses
Bobst will share with customers its vision for digital solutions in packaging: from digital printing to converting.
Die cutters
To maximize die cutter productivity, new automated solutions will reduce the tasks required to perform a job changeover. Among the new developments is Smart Feeder II, and a one-touch setting feature for the non-stop grid, shown on the new ExpertCut 106 PER (pictured, above) die-cutter. Other developments include waste reduction and increased operational tool life that allows high-quality cutting to be maintained and the cost per box to be reduced.
Foil blockers
Bobst will unveil details of its new ExpertFoil 142, the only dedicated foil stamping press available in the size VI format, and for the duration of the show, a MasterFoil 106 PR will be on working display at FSEA Gold Leaf Award winners Köch & Glasder GmbH, located just 20 minutes from the exhibition. Fitted with Power Register II, it is the only foil blocker to deliver perfect foil-to-print registration, and has the Foil Touch System, which requires lower heat and less pressure.
Folder gluers
The company has a new approach to processing cartons after glue application, which reduces waste and improves the quality of the final product. Constant monitoring of the output of the folder-gluer line and upstream processes allows customers to move towards “zero-fault” packaging.
New advances for food packaging improve the performance on complex cartons such as crash-locks and 4/6 corner boxes, including shorter set-up times, higher run speeds and reduced waste. For pharma packaging, new developments extend the capabilities of in-line Braille application.
Read more on Bobst here
Read more on Drupa here
Read more PPW features here
Stay up to date
Subscribe to the free Label News newsletter and receive the latest content every week. We'll never share your email address.