Q&A: G P Pathak
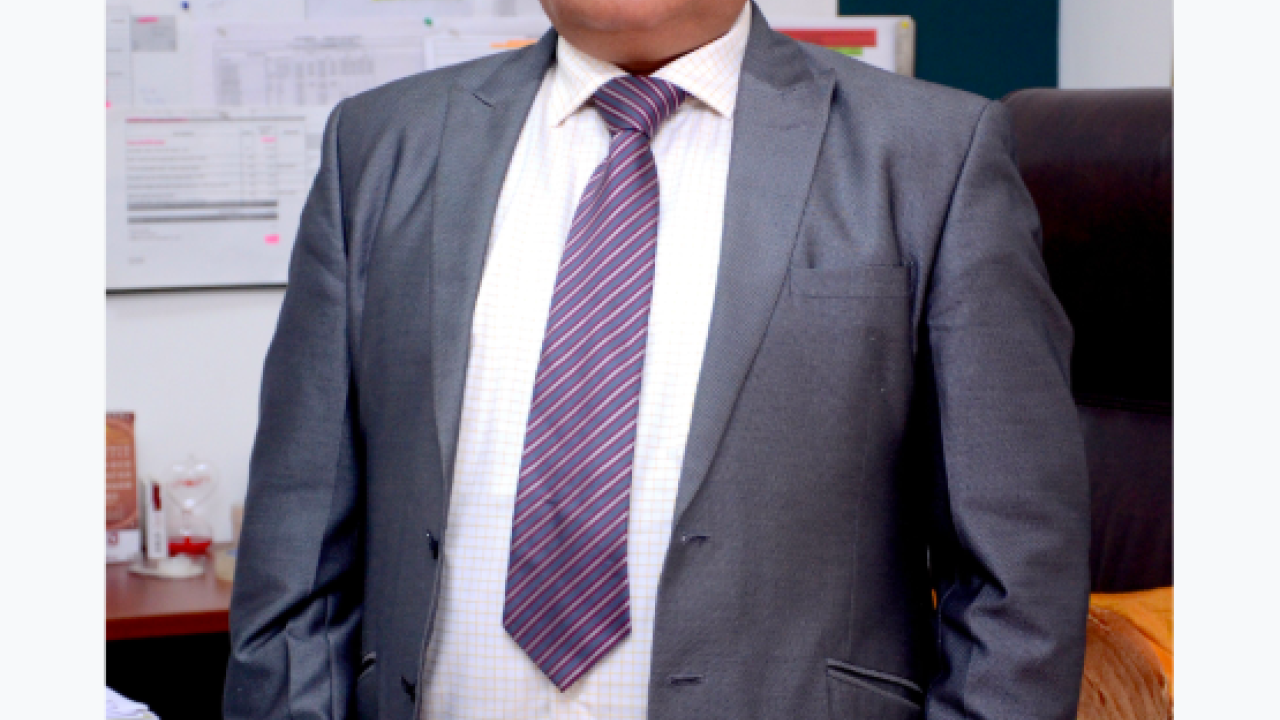
L&L: When and how did the holography business of Uflex start?
GP Pathak: We started doing holograms in the year 2004 with an intent to provide anti-counterfeiting products to the industry across various business verticals. However, it was only in 2010 that we invested in the first flexo press. This was followed by our first Gallus press in 2011 and then by an Orthotec intermittent letterpress.
Our innovative and hybrid labeled products with features got a fabulous response which forced us to think aggressively in increasing our production capacity. We have added another Edale and Gallus presses this year to double our capacity from 200,000sqm to 500,000sqm of labelstock every month. With this set-up, the business unit is supplying to most industries including cosmetics, liquor, tobacco, pharmaceuticals, FMCG, lubricants and electronics, among others, and exporting to Bangladesh, Sri Lanka, Turkey, Egypt and Tunisia.
L&L: What is the turnover of the holography business unit?
GP Pathak: The turnover of our business unit for the financial year 2017-18 was 525 crore INR (74 million USD). Thirty-five percent of this has been contributed by holographic labels printed on narrow web presses and standalone holograms. Sixty percent was contributed by products made on wide web presses with security features for carton packaging as well as flexible films, and the remaining five percent was contributed by value-added textile products.
Our label printing business has had an exponential growth from five crore INR (less than one million USD) three years back to 25 crore INR (almost 3.5 million USD) in the last financial year. We are geared up as a business unit to double our current revenue from label printing in 12 to 18 months.
L&L: How many factories does Uflex have for this business?
GP Pathak: There are a total of seven factories with 775 employees dedicated to holography and label printing business at Uflex. While three factories are in Jammu, two are in Noida and one each is in Bhopal and Hyderabad. We also have a manufacturing set-up in Mexico and Poland, dedicated to holograms and fresnel lens respectively.
Furthermore, a new holography plant in Russia is expected to start commercial production by May 2020, where the focus will be on holography.
To facilitate product development and innovation, Uflex has a research and development center in Noida and Jammu with a work force of 30 highly qualified personnel.
L&L: How do you identify new locations for your factories?
GP Pathak: Market research is conducted in various geographies to establish the business potential in that area along with customer needs. Based on the opportunity available, the necessary set-up is put in place to capture the market. Our mantra is to break even in three years’ time.
In some cases, we set up manufacturing units for specific government projects which are highly sensitive from a security perspective. We have such project-based manufacturing set-ups in Madhya Pradesh and Andhra Pradesh.
L&L: Please elaborate on the operations at the holography division.
GP Pathak: We are a certified security printer for financial and legal documentation as well. The premises are highly secure and conform to international norms.
Our anti-counterfeiting solutions are embedded with fresnel lens, sterling lens, latent image, QR coding, cast and cure along with various mastering and non-mastering features. These solutions can be affixed on the products as well as packaging. Our mastering machines can develop solutions up to 150,000 DPI. Thus, using different permutations and combinations, we develop highly secure products at a competitive price which are very difficult to imitate.
L&L: What patents have been granted to the holography business?
GP Pathak: Uflex’s founder and CMD Ashok Chaturvedi has two patents granted that have aided our holography business. The first is for the method and apparatus for producing flexible polymeric packaging film or fibrous substrate or laminate using e-beam curing. It was granted for a period of 20 years in October 2012.
The second was awarded in September 2011, again for a period of 20 years, for his invention of a transparent substrate for providing security against counterfeiting.
L&L: How do you react to price pressure from brands?
GP Pathak: Quality and security come at a price. There is a tremendous resistance from customers to price and we are confident that customers are realizing the cost benefit of using our products. A small increase in procuring a secure label increases the top line as well as the bottom line of any company, along with the brand value.
We have seen a steep increase in our customers’ understanding of using a secure product and we have many success stories, especially in pharmaceutical, FMCG, automobiles and many business verticals where pricing is not a deterrent.
L&L: What recycling initiatives have been taken at Uflex?
GP Pathak: Most of the plastic waste that includes multi-layered plastic (MLP) is being landfilled across the world, thus posing a serious threat to the environment. India generates 25,940 tonnes of plastic waste daily, of which at least 40 percent remains uncollected. There is a dire need to segregate and collect plastic waste systematically, and make sure it is used efficiently.
Uflex has stayed committed to the cause of green environment for many years and has undertaken waste management efforts to reduce the MLP waste that gets dumped into landfill and oceans.
Foreseeing the increasing per capita consumption of packaging, Uflex’s CMD Ashok Chaturvedi set up a recycling plant inside the Noida factory. This infrastructure for waste handling earned Uflex the Best Paper Award in 1995 at the Davos Global Forum. Furthering these efforts, the company established similar MLP waste recycling unit in Jammu plant as well.
The method of recycling involves collecting about two tonnes of discarded waste, generated during the manufacturing process at the plant. The collected waste is pre-washed, made compatible and passed through heated screw and barrel before being converted into tiny granules or pellets. These pellets are used for making useful domestic and industrial products like flower pots, paver tiles, plastic cupboards, washbasins, outdoor furniture, plastic road, traffic cones, trash bins, manhole covers, pipes, signboards and many such essential items.
Reaffirming its commitment towards a greener future, Uflex recently commissioned its new pyrolysis plant at its Noida unit in October 2018, earning it the distinction of first such plant in north India.
Pyrolysis is a process of chemically decomposing organic materials at elevated temperatures in the absence of oxygen. The pyrolysis plant’s two reactors at Uflex Noida can convert six tonnes of discarded waste material that’s generated every day from printing, unused trim, laminates, tubes and other unprocessed material into liquid fuel, hydrocarbon gas and carbon black. Thus, at the end of the process, the entire waste is converted into three forms of fuel, which is further utilized in manufacturing processes. Carbon black powder is cooled and packed into bags for further use as a solid fuel. A mixture of pyrolysis oil vapor and hydrocarbon gas exits the pyrolysis reactor and is subjected to fractional condensation to get separate fractions of hydrocarbon gas, pyrolysis wax and pyrolysis oil. Hydrocarbon gas is used in the pyrolysis hot air generator and energy generated is fed to the pyrolysis reactor for heating the plastic waste.
Pyrolysis oil or light distillate oil is used as a liquid fuel in industrial boilers or diesel engines to produce electricity.
The pyrolysis process works as a sustainable waste-to-energy technology which is not environmentally harmful, unlike incineration of plastic waste. Through pyrolysis and recycling of MLP waste, one has the option to eliminate a large chunk of plastic waste from our planet.
L&L: What activities do you enjoy outside of work?
GP Pathak: Apart from launching new products in the market, I enjoy listening to old Hindi music, especially songs by Mohammed Rafi.
Stay up to date
Subscribe to the free Label News newsletter and receive the latest content every week. We'll never share your email address.