Zebra adds capacity with Nilpeter FA-4*
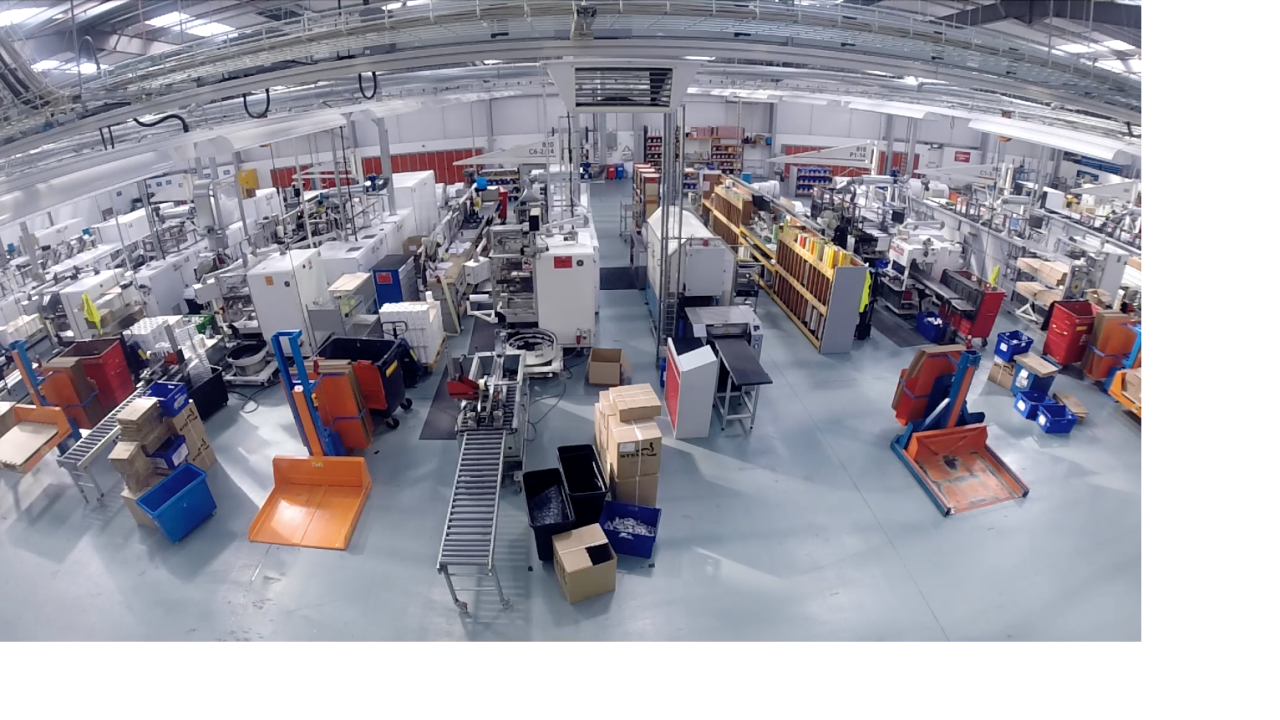
Zebra Technologies Europe’s site in Preston – one of two facilities in the UK, alongside its head office in Bourne End – supplies the EMEA region with Zebra Certified Supplies, and is supported by further label printing at its site in Heerenveen, the Netherlands. There are 11 presses in Preston; five in Heerenveen.
The US-headquartered parent company Zebra Technologies – which has four label production sites in the US, mainly equipped with Mark Andy presses – entered the UK market in 1993 through the acquisition of Preston-based Brook Labels. The premises was relocated five years later, and it is at this site that Zebra Technologies Europe has installed a Nilpeter FA-4* – its first press in Europe not built in-house – as it seeks to increase its market share of supplies for its thermal printers.
‘We want to attach more label sales to our printer sales in order to increase market share,’ says Elaine Wilkinson, senior manager, supplies product marketing, at Zebra Technologies Europe. ‘We are growing quickly and need to produce more complex products locally, such as wristbands, rather than import them from our sites in the US. We want to be flexible in our production. Our business is growing too quickly for us to continue manufacturing presses internally, hence the installation of the Nilpeter FA-4*.’
Zebra Technologies Europe sold 56 million EUR (66 million USD) of supplies – labels, ribbons, wristbands and tags – during 2016 in EMEA. It’s an impressive figure, though it doesn’t reach the 40 percent market share enjoyed by its printers. However, a renewed focus in this area is already reaping benefits. Zebra Technologies Europe has made a number of investments including appointing a new sales team in charge of supplies in specific territories across EMEA, and the Nilpeter press, which has brought additional capacity since its installation late last year.
Zebra exhibited for the first time at Labelexpo this year, where it showcased Zebra Certified Supplies and met with a number of potential new partners – Zebra has some 120 specialist partners currently focused on selling supplies.
On the day of L&L’s visit, staff at the Preston site were celebrating a record first quarter of supplies sales. The figures of 15.2 million EUR in barcode supplies, more than 3m EUR in wristband sales, and more than 4.5m EUR of ZipShip (stocked label) sales areall records. Custom-made labels also had a strong quarter – the 3.3m EUR of sales in this area, though not a record, was higher than in any quarter in 2016. According to Elaine Wilkinson, the company’s average annual growth has been around 10 percent for the last three years.
In-house expertise
The Nilpeter FA-4* joins a fleet of presses designed and built in-house by engineering manager Mark Richmond and his team since 1998. ‘We convert complicated synthetic materials, which require a very high degree of web tension control throughout the machine,’ says Richmond. ‘There were no machines on the market that fitted our exact needs for the production of high quality plain labels, so we developed our own, incorporating operator feedback.’
Richmond and his team have designed and built eight plain label presses, as well as three 2-color machines, one 3-color, two 4-color and one 7-color. The first 4-color press was sent to the Heerenveen site with the arrival of the Nilpeter FA-4*. ‘The machines are designed to high specifications and focus on ease of use. They are tailor-made for our specific business needs. All the presses built in the last 10 years have full servo control technology,’ says Richmond. ‘We keep a wide range of spare parts, so we don’t have to wait for third party suppliers.’
The seven flexo presses built in-house have a 14in web width. Two of them are equipped with Tamarack insertion units for the production of wristbands, and all have integrated Meech web cleaning equipment.
Finishing takes place on thirteen turret rewinders from AB Graphic and Zebra has recently installed a Martin Automatic butt splicer enabling continuous reel-to-reel production. Plate mounting equipment comes from JM Heaford; plate cleaners from Flexowash; and anilox cleaners from Alphasonics. Tooling is supplied by RotoMetrics and Wink.
Fifty-five people are employed in manufacturing at the Preston site – which is certified to ISO 9001 quality and ISO 14001 environment standards – with 140 staff in total. Production runs 24 hours a day, five days a week in a 24,000sq ft (2,200sqm) manufacturing area. Factory floor space was doubled in 2013. A further 20,000sq ft (1,850sqm) is dedicated to warehousing and distribution, and 12,000sq ft (1,100sqm) to office space.
Nilpeter installation
As Zebra Technologies Europe’s first outsourced press, the 8-color Nilpeter FA-4* represents something of a departure for the company, and brings additional capabilities. The water-based UV press features a Tamarack insertion unit, rail system, turnbar, reverse printing units, relam/delam and lamination. It has three die stations, including a Quick Change die-cutting station developed by Nilpeter in cooperation with Kocher+Beck, which allows a die to be changed in just 10 seconds. A 100 percent inspection system will shortly be added.
‘It has more functionality than our existing presses,’ says Elaine Wilkinson. ‘The quick-change die, job save function, ink station and sleeve system are all different, so we have been focused on getting the operators up to speed. They love the additional functionality, while the reduced changeover times increase throughput.’ Wilkinson reports that in-house production of plain label presses will continue, but for color presses, Nilpeter is likely to be Zebra Technologies Europe’s preferred partner in the future.
The Zebra team studied presses from rival manufacturers at Labelexpo before opting for the Nilpeter. ‘Its build quality had a slight edge over the competition,’ reveals Richmond. ‘Its ease of use and storing and retention of set-up info were big advantages. The print engines are phenomenal. The other machines we looked at were all good – but the Nilpeter press just goes that little bit further. It was designed as a quick-change machine, and is as good as you will get in the flexo industry.’
Shift team leader Andrew Shuttleworth, who operates the Nilpeter FA-4*, is similarly enthused. ‘In 17 years, it’s the best machine I’ve operated,’ he reports. ‘Its print quality and registration accuracy are excellent. Jobs can be recalled at a click of a button on an iPad. It’s a Rolls-Royce of a press.’
Stay up to date
Subscribe to the free Label News newsletter and receive the latest content every week. We'll never share your email address.