Closing the loop on release liner
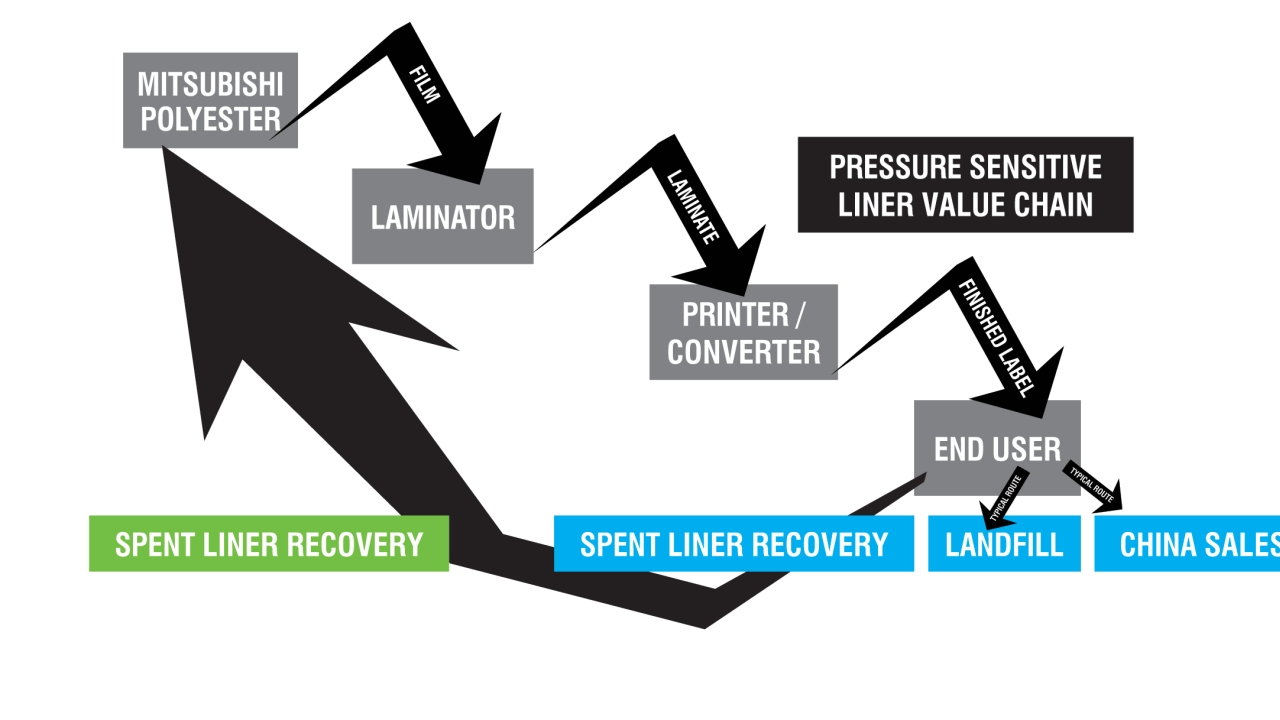
Mitsubishi Polyester Films is claiming a world first with a new technology which closes the recycling loop for PET release liners. Danielle Jerschefske reports
The world consumes 1.4 million tons of pressure sensitive labels each year, and the volume is increasing. Release liner, paper and film, makes up as much as half of that volume, but less than 12 percent is recycled annually. With the packaging industry being pushed by legislators and consumers towards zero landfill waste, this situation is not sustainable.
Mitsubishi Polyester Films, an Americas affiliate of Mitsubishi Plastics, with headquarters in Greer, South Carolina, has now developed a PET filmic liner recycling technology called Reprocess that will allow spent liner to be reused to produce first quality liner. The supplier has tested the quality of Reprocess liner in high-speed application lines with Spear for beer bottle labeling, and CCL for high-volume health and beauty products. It works – reliably, and it costs the same as virgin PET liner, according to the company.
The parent of Mitsubishi Plastics, Mitsubishi Chemical Holdings Company, follows Kaiteki, a Japanese term meaning ‘comfort’, in an effort to bring more corporate social responsibility to the various markets in which the company operates. In 2009, MCHC president Yoshimitsu Kobayashi took Kaiteki a step further with the establishment of the Kaiteki Institute, which produces research to help develop more sustainable products.
‘We believe the need for sustainable solutions is a long term trend,’ says Dennis Trice, Mitsubishi Plastics COO. ‘The label market is strategic for us and the investment in Reprocess is an indication of our commitment to the industry and toward growing pressure sensitive technology utilizing PET liners.’
The one million sq ft Mitsubishi plant in South Carolina houses multiple film lines manufacturing 150-200 million pounds of PET liner annually. It is one of the few release liner suppliers that makes its own polymer, specializing in in-line coating of filmic materials from 48–1000gauge (12u to 250u). The advantage is that the plant can produce several polyesters with different characteristics dependent on application and process. Also at the site is a full R&D center with a pilot facility operating 24/7, dedicated to new product and process innovations where the Reprocess technology was developed.
In the late 1980s the group shifted its focus from adhesion coating to release properties. It now produces release liners on multiple lines and has invested over 200 million dollars at its Greer site in the last 10 years. Its most recent major capital expansion was Line 9, a 100 million dollar investment installed in 2003. Today Mitsubishi claims to be the world’s largest PET film release producer and plans further multi-million dollar investment to support the Reprocess technology.
Closing the loop
Completing the cradle-to cradle recycling loop relies heavily on buy-in from multiple stakeholders through the value chain. The Greer plant already has a fully functioning, integrated waste material recovery system. ‘We need to have a good internal recycling system to recover waste in our own production,’ says Dr Marshall Ledbetter, Reprocess project director. ‘However, externally the cycle is much more difficult to trace and brings more challenges.’
Mitsubishi is working hard on building a PET liner waste collection system and has enlisted the help of professional ‘waste’ collectors for this purpose. It has distributed Reprocess-labeled containers to participating CPG facilities and packagers to create awareness about the scheme and to try and get the liner viewed as a valuable resource as opposed
to waste. After collection, the next step is a visual separation by material clarity and color, and removal of any labels still attached. Because of the difficulties in educating collectors on how to separate Mitsubishi liner from other sources, this is done in-house. If Mitsubishi is not able to tell visually whether a liner is theirs, the material is sent to the lab for examination. Ledbetter explains, ‘This is a critical step in the process because we must be able to take the material back to its original state.’ The purity of the material is essential. Competitor material will be accepted only if its purity can be guaranteed.
Recovery challenges
CPGs must support the collection of release liner in order for the closed-loop system to work. There must be adequate material recovered, consistently, to meet the minimum reprocessed content required to place Reprocess back into the value chain.
CPGs typically use one waste collection company, for simplicity’s sake, for all of production waste removal. Yet recyclers often find it difficult to compete with the price of sending the material to landfill. Higher removal costs are a deterrent to value recovery options because, typically, the plant manager, who has ultimate say in waste removal, is reviewed solely on their bottom line.
Mitsubishi is encouraging CPGs to work with firms that can divert various waste streams from landfill. Bill Wells, director of marketing for the label sector explains, ‘It’s imperative that we get the right names within the companies, to reach the person that has the power to make change.’ Many times it’s the regional manager of multiple sites who is more closely involved in meeting company-wide sustainability goals and has the ear of the board.
Disposal options for release material, particularly film, in the US and Europe are bleak. If the material is not land-filled, many thousands of tons are downcycled in China or in other emerging markets to produce low value items like toothbrush bristles and other commodity items. Mitsubishi estimates that more than 60 percent of North America’s release liner is shipped overseas.
Wells explains, ‘We found that many labelers believe their product is being recycled because their waste is sold, but they have little idea what the “grave” or re-use potential is for their materials.’
The collection project has been active for one year and is looking to expand its sources of spent or used liner. In addition to CPG buy-in, another barrier to recovery is the ability to consolidate a truck load of material to ensure that the recovery footprint and costs are kept to a minimum.
LCA
A viable closed loop system must provide ‘re-products’ with the same performance characteristics as virgin; the re-product must be cost neutral and have a reliable supply chain, in addition to reducing carbon footprint. Life cycle analysis (LCA) is a means of assessing the environmental impact of a product by looking at all stages from resource extraction, materials processing and manufacture, distribution, use, and disposal or recovery.
Mitsubishi procured a third-party auditor for an LCA of Reprocess as compared to virgin PET chip production. Variables were restricted to spent liner collection through to new material leaving the plant. The audit found that PET chip produced with the Reprocess system delivers a 91 percent reduction in cumulative energy demand and a 74 percent reduction in global warming potential when evaluated across Transportation, Process and Embodied Energy consumption compared to virgin PET chip.
Ledbetter says, ‘No matter which type of polyester liner we want to create with reprocessed film, it will have the same qualities as virgin material.’ Every property spec – stress, tensile strength, elongation, and modulus – have been tested across multiple platforms. The company believes the introduction of a closed loop recycling process and recycle content liners will help support the continued growth of pressure sensitive labeling applications utilizing PET. Wells says, ‘As laminators, converters, retailers, and ultimately consumers, all ask for more environmentally conscious solutions, we believe the Reprocess concept combined with the inherent performance benefits of PET liners will bring value to the entire chain.’
Sustainable revolution
Release liner is today under intense pressure, from Sustainability Scorecards and legislation such as Brazil’s National Policy on Solid Waste (PNRS) enacted in August 2010. Mitsubishi Polyester Films’ vision is for the various stakeholders to work together to retain value within the pressure sensitive supply chain. Ledbetter says, ’Eventually, we’d like to see Reprocess as an industry standard.’
For the future, Mitsubishi is looking to grow the Reprocess product line and expand capacity, while increasing the percentage of recovered content used in construction from five percent to 25 percent over the next 18 months. It has plans to invest in the capital equipment necessary to keep Reprocess cost neutral, but it must get the economics, particularly recovery participation and collection volumes, in place to keep it this way and continue moving forward.
This article was published in L&L issue 4, 2011
Pictured: Closed loop solution for PET film release liner
Stay up to date
Subscribe to the free Label News newsletter and receive the latest content every week. We'll never share your email address.