ETI Partners with Enercon to Simplify Label Stock Production
ETI Converting offers fully integrated printing, coating and converting lines that enable production of pressure sensitive adhesive materials and labels, from A to Z, in a single pass, says ETI. The company’s approach eliminates the need to outsource label stock procurement with a fully integrated label printing, adhesive/silicone coating, laminating & finishing machine. A partnership with Enercon Industries ensures reliable corona treating, which is key to enabling coating adhesion.
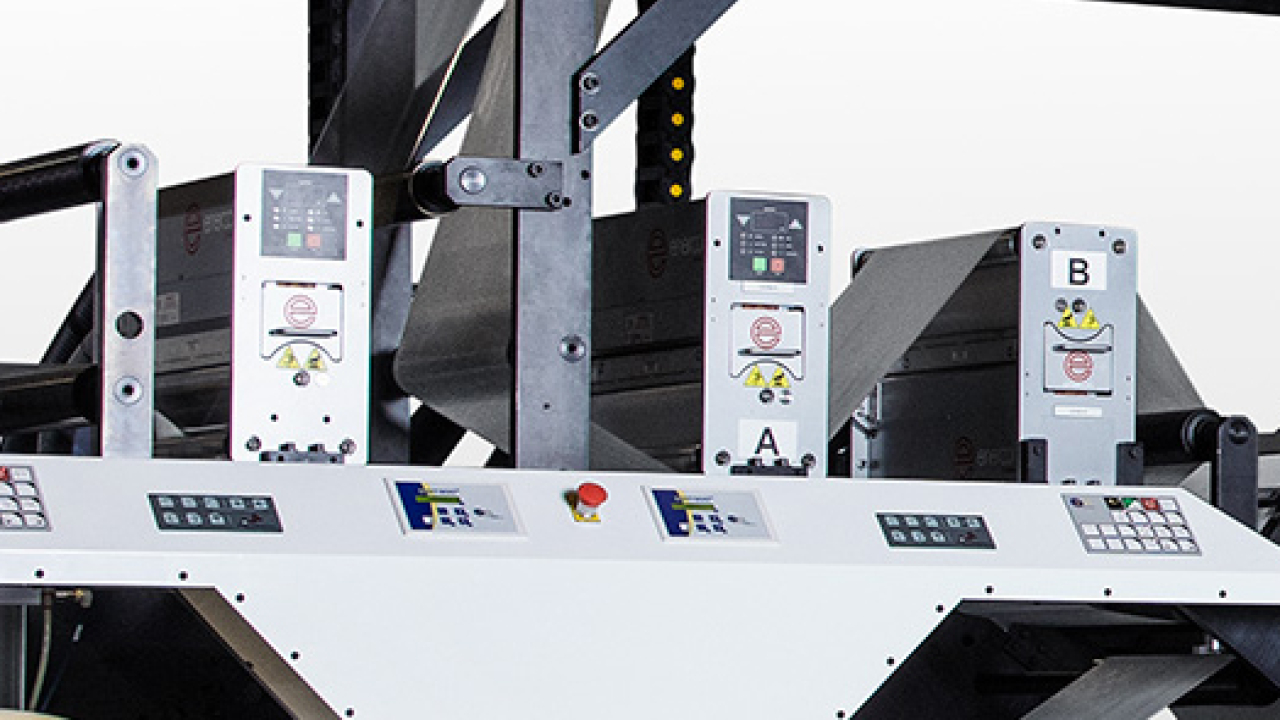
Enercon Corona Treatment enables adhesion
Users of ETI’s COHESIO system most often produce labels from BOPP and PET. However, the system is so versatile it can handle other materials including paper substrates. Corona treatment is used prior to the siliconizing step in the inline process. It creates the ideal anchorage for the silicone to adhere properly to the substrate, for perfect release properties on the liner.
Enercon’s CoronaFlex corona treater offers powerful surface treatment from a compact footprint. Treatment increases the wettability and surface energy of substrates to enable bonding with required coatings. The corona treater is powered by Enercon’s Compak power supply series. When new applications for treatment arise, ETI reaches out to Enercon to tap into the company’s vast surface treating application expertise, says the company.
According to ETI president Maxime Bayzelon, ETI uses Enercon because, 'the equipment is highly reliable in challenging environments, integrates easily into our systems, and the company always provides prompt and knowledgeable support.
In addition to support from Enercon’s factory, Enercon’s local representative Webconvert also plays a key role. Maxime adds, 'The Webconvert Team is very proactive, and their collaborative approach is of tremendous value.'
Growth in linerless labels
ETI offers proven technology, however they do not follow a one-size-fits-all approach. Their multidisciplinary teams take time to understand their customer’s unique needs and requirements while taking in consideration the tangible end product. After the conception and configuration phases, ETI’s specialists make sure to pass along all the knowledge needed to the client to make educated choices about raw materials and production recipes
This approach is particularly advantageous in serving the growing demand for the production of linerless labels. Over the last several years, ETI has developed significant expertise with PSA linerless label manufacturing. They are able to support clients looking to produce both standard and specialty products such as direct thermal labels, wrap/sleeve food packaging labels, and pre-glued wraparound labels.
For customers dedicated to linerless label production, ETI offers their LinerO system. For operations requiring both linerless and traditional PSA labels, the COHESIO offers the flexibility and performance. This made-to-measure, result-driven approach ensures maximum ROI for ETI customers and fosters their self-reliance as they grow their business with new technology, according to the company.
Stay up to date
Subscribe to the free Label News newsletter and receive the latest content every week. We'll never share your email address.