First Windmöller & Hölscher Miraflex S CI flexo press running in North America
Canada’s Flexstar Packaging is now operating the first Windmöller & Hölscher Miraflex S CI flexo press in North America.
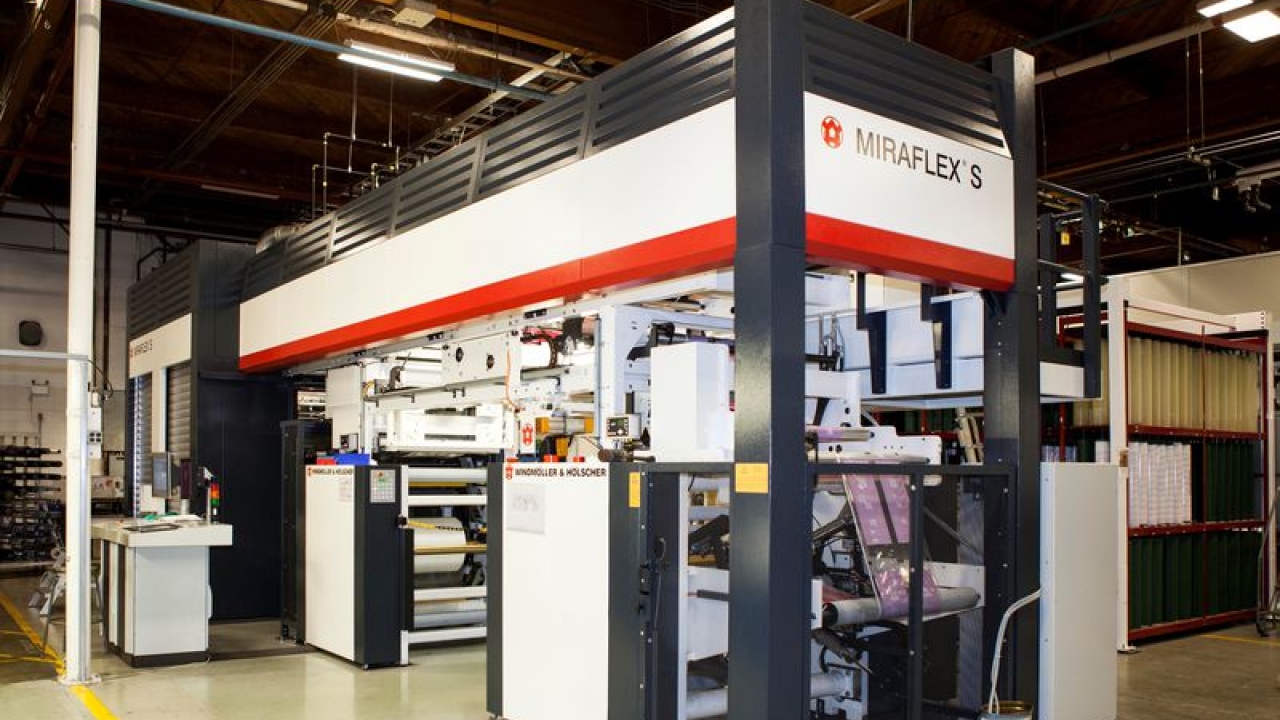
Based in Richmond, British Columbia, Flexstar Packaging manufactures custom printed, laminated, flexible rollstock and specialty films for the consumer and industrial markets in North America. Its products include: barrier laminations for food products; plain and printed films; cold seal rollstock; foil laminations; boilable, microwavable and retortable laminates; pre-made bags and pouches; and unprinted industrial/converter film.
Its capabilities include film extrusion, printing, coating and laminating, and slitting. It offers flexographic printing with in-line lamination in both mid and wide web formats, and its equipment portfolio includes gearless technology, automatic viscosity controls, web inspection, defect detection, video plate mounting, sleeve technology, automatic ink dispensing and X-Rite color control systems.
The Miraflex S platform has been developed by Windmöller & Hölscher to allow fast job changes for narrow to mid web widths. The cleaning system, Turbo Clean, cleans all printing units in just 3.5 minutes, so exchange for new orders only last a few minutes. Another advantage is the avoidance of waste material with loss of only 23m from unwinder to rewinder. The printing length is 250-800mm (9.8-31.5in).
The Miraflex S, installed in November last year, has added narrow and mid web width printing capacity to Flexstar Packaging’s capabilities, and complements the company’s existing machinery ‘perfectly’, according to Flexstar managing director Marc Bray. ‘The Miraflex S mastered reliably each pending job, whether PET, OPP or thin PE films. We especially benefit from the flexo control insetter module, which has increased our productivity in applications with matte surfaces.’
The Miraflex S installation is part of a larger expansion package at Flexstar Packaging. The company has expanded its building space by about 3,000 sq m, including an expanded warehouse and area for special processing. The building also features an innovation center. Other investments include a third laminator, another pouch making machine and a laser machining system for wide web applications.
Flexstar Packaging is further working to improve its environmental footprint by means of a regenerative thermal exhaust air purification plant to eliminate VOC emissions. A heat exchanger collects energy for heating the works and for special lamination applications which require curing in the drying chamber. After completion of the project in autumn 2016, Flexstar will be the first manufacturer of flexible packaging with this technology in western Canada.
Stay up to date
Subscribe to the free Label News newsletter and receive the latest content every week. We'll never share your email address.