Joining the dots
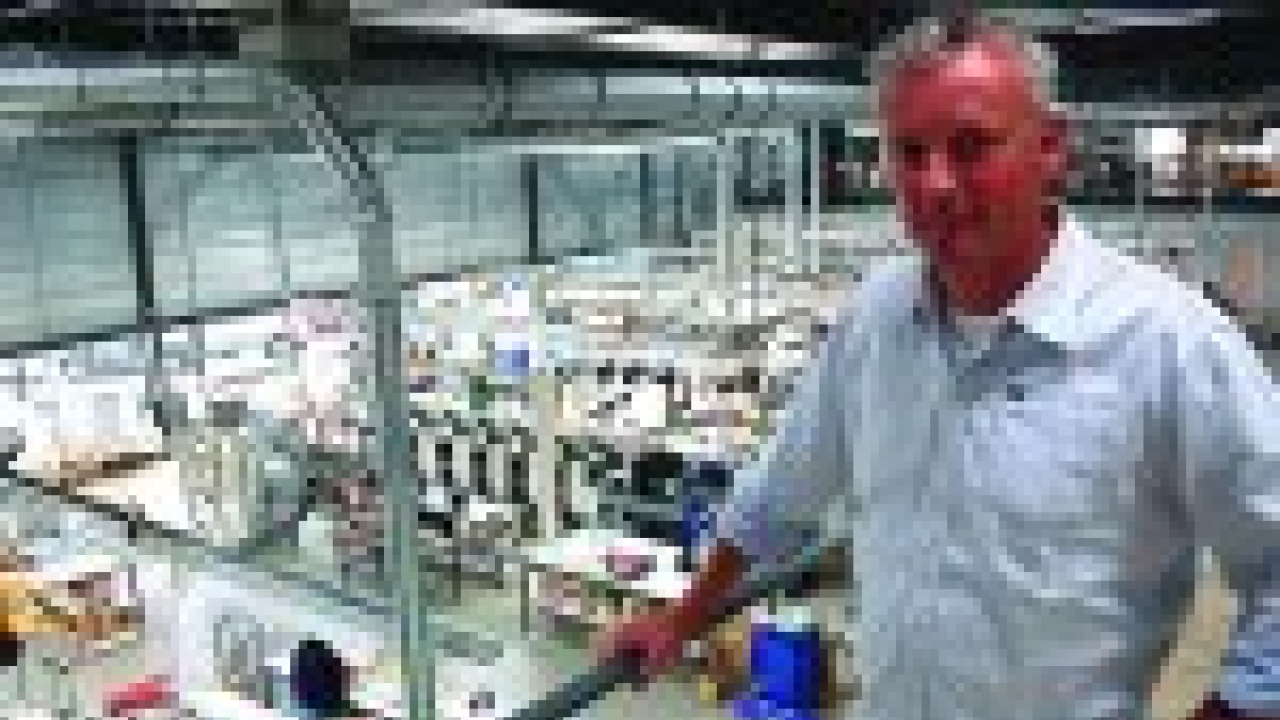
Xeikon, EskoArtwork and Cerm have created a unique end-to-end JDF solution for digital label printing at Dutch converter W&R Etiketten. Andy Thomas reports
Dutch label printer W&R Etiketten is combining its Xeikon 3300 digital label press with EskoArtwork automated workflow solutions and a Cerm Management Information System (MIS) to create a streamlined and JDF-connected production process. Further automation will re-shape the company when its conventional presses and entire product warehousing are integrated into the solution, along with new internet based services.
W&R Etiketten is located in
In 1999, looking to move the business to a higher level in terms of quality and productivity, W&R Etiketten made a major investment in UV flexo technology in partnership with MPS, acquiring four presses. In 2002 W&R Etiketten expanded into a bigger factory with more than 4,500 sqm of floor space, allowing Willemsz to design a workflow based around Lean manufacturing principles.
In the following years, Willemsz noticed a shift in the market. ‘Internationalization has spurred an increase in the variety of products. For example, you now have more than 40 flavors of shampoo, all requiring a different label. However, clients don’t want to keep stock of all these labels. In the past, we used to stock them for one or two years for our clients. Today, orders come in one at a time, and the responsibility for availability rests with suppliers like us.’
With the number of jobs going up and the number of labels per job going down, Willemsz expects growing pressure on the high end of the market: ‘Capacity is still growing, while demand for small and medium-sized run lengths is increasing. This is not an ideal situation.’ W&R Etiketten decided to join the digital print revolution to escape this negative spiral: ‘Digital print has been around for some years now, but we decided early on to wait and see what would happen with this technology. It was only when Xeikon re-entered the label market and offered a serious alternative to existing systems that we saw real possibilities to re-invent our business.’
Bigger picture
‘Getting a digital press is not the only issue,’ explains Willemsz. ‘You have to take a look at the trends for greater variety and smaller run lengths to see the bigger picture. We needed to seriously increase the number of jobs we produced to keep our turnover at the same level. However, our account managers would still need the same amount of time to manage each order. So we either needed to hire more account managers, or bring down our cost per order in another way – and that meant automating and standardizing our processes as much as possible.’
And that is where Cerm got involved. W&R Etiketten had been working with the Cerm MIS solution since 1998 and needed to connect it directly to pre-press to handle the increasing number of jobs on the Xeikon 3300 press.
‘This was when we, almost automatically, decided to work with EskoArtwork,’ recalls Willemsz. ‘Cerm and EskoArtwork have developed a pre-press automated workflow featuring an intelligent JDF connection for the label industry. The solution ensures all job information is entered once and is used throughout the whole production process. So there is no more need for two separate systems that both have to be updated every time new information is added.’
W&R Etiketten also opted for the EskoArtwork RIP, as this means they can now manage color and quality for both the digital and conventional production processes from one source.
Networked business
Information from the Cerm MIS is now supporting the EskoArtwork prepress workflow and gives the Xeikon 3300 press production process directions, including pre and post calculation and job status. Meanwhile, thanks to a true JDF/JMF connection, real-time information on order status and time registrations from the Xeikon 3300 is automatically being sent back to Cerm, enabling the system and its users to track jobs and monitor the uptime of the digital press.
‘By the end of the year, we will also be able to send information to, and retrieve data from, the conventional presses via the Cerm press counters and the Shop Floor Data Collection module from Cerm,’ says Willemsz. ‘This will enable us to get even tighter control of production and increase efficiency.’
Willemsz expects additional internet services to play a key role in the company’s development: ‘The internet will prove very important to us and our clients. It will enable them to submit orders, upload data and track job progress. Cerm has already developed excellent applications for this purpose, which combined with our EskoArtwork and Xeikon solutions means we’re ideally placed to exploit new commercial opportunities.’
To the max
W&R Etiketten underlines the many benefits of the JDF integrated workflow solution. ‘Automation and standardization at first take some time for people to get used to,’ concludes Willemsz. ‘But once everyone gets into the new routine, it will increasingly save us time and money.’
Looking to the future, Willemsz has a clear vision of what W&R Etiketten will look like: ‘We will be a bigger and more professional company. There will be two Xeikon digital presses running next to each other, and our conventional presses will be more efficient than ever before. The internet will have become a major sales channel for us, and clients will be increasingly involved in managing jobs themselves.’
Unified workflow solution
W&R Etiketten’s unified workflow solution is one of the first in the label industry to bring together administration, pre-press, workflow automation and digital printing systems using JDF integration. All job specifications, such as format, quantity, material, colors, finishing requirements and date of delivery, are entered into the Cerm MIS solution. And because there’s no need for double entries, the risk of errors is minimized. The Cerm MIS database then provides all the necessary information to the EskoArtwork Automation Engine workflow.
The EskoArtwork Color Engine handles color management for all jobs. At the same time, Cerm’s MIS system passes job information to the X-800, Xeikon’s digital front-end, through a JDF connection. Based on this information, the X-800 will pull the relevant PDF file from the central server and start processing according to the settings specified by the MIS. During production, Xeikon sends status information back to the Cerm MIS using JDF and JMF. CERM uses this information to keep track of production status and costs, and can monitor the uptime of the digital press.
In a second phase of fully automated JDF workflow integration planned for later this year, W&R Etiketten will add Cerm’s web storefront application, Web4Labels, so customers can submit jobs via the internet. Also, the Cerm MIS and the EskoArtwork Automation Engine will together plan and control the job information to and from the conventional UV flexo label presses, next to the Xeikon 3300 digital label press.
Jack Willemsz believes that this highly advanced, automated JDF workflow solution will enable W&R Etiketten to increase the speed of its order intake and job preparation, make planning and production more efficient, and significantly reduce the risk for errors. And because the solution will keep track of every aspect of a job's lifecycle, invoicing and cost analysis will be much more accurate.
Pictured: W&R Etiketten managing director Jack Willemsz
This article was published in L&L issue 4, 2010
Click here for more stories about Xeikon on L&L.com.
Click here for more stories about Cerm on L&L.com.
Click here for more stories about EskoArtwork on L&L.com.
Stay up to date
Subscribe to the free Label News newsletter and receive the latest content every week. We'll never share your email address.