Laser die-cutting a value-added technology
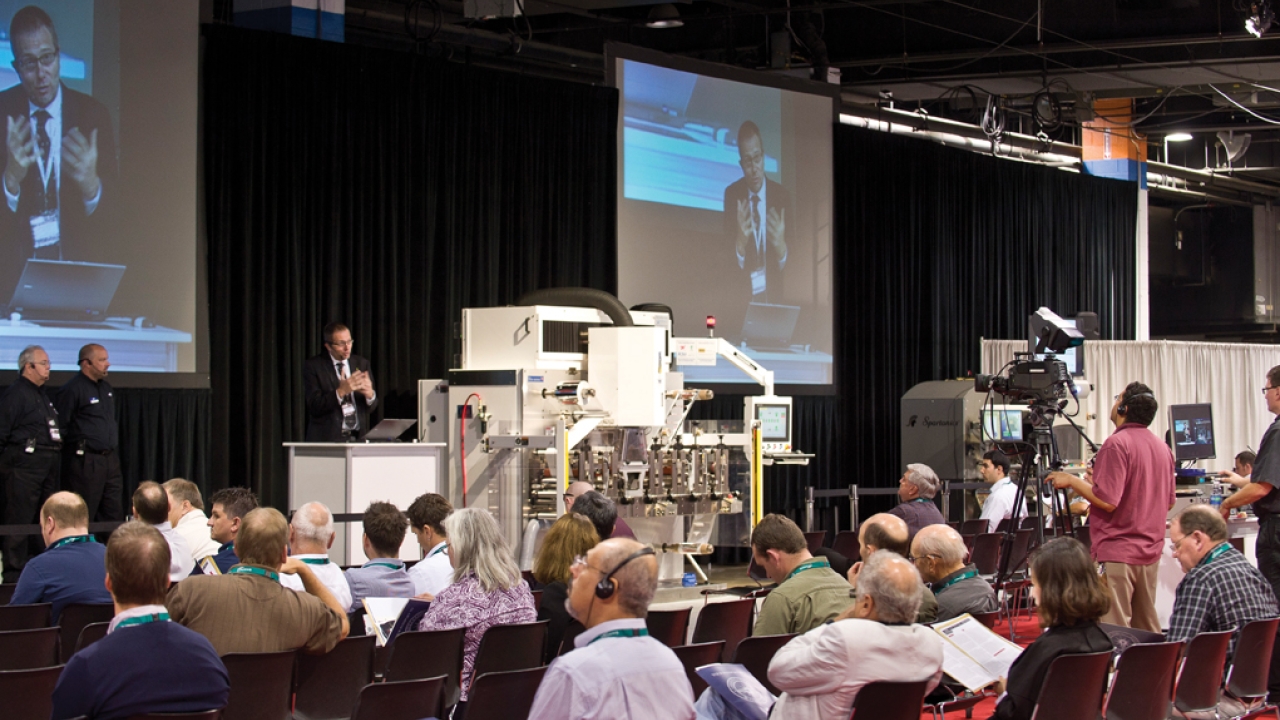
Mike Fairley reviews the Laser Die-Cutting Workshops held alongside Labelexpo Americas and summarizes what the technology can bring to today’s label converting plants
Laser die-cutting of self-adhesive labels is not new. The first machines showing the technology at Labelexpo exhibitions goes back to the mid-1990s. These were not only cutting the label to shape, but laser etching and also cutting windows out of the release liner. They certainly attracted a lot of interest, but were seen as rather slow and expensive at that time, as well as prone to causing brown edges to the die-cut face material, and not always waste stripping effectively.
How things have changed. Laser die-cutting technology for labels today is far superior to that of 16/17 years ago. It’s faster, more efficient, has a higher cut quality and, if used for the right kinds of applications and markets can certainly both reduce a converter’s costs and create value-added opportunities. Yet laser label cutting has still been somewhat slow to gain mass adoption in label converting plants – perhaps because of its early perceptions.
It was to address these issues and better highlight what laser cutting technology can offer converters that Labelexpo introduced its Laser Die Cutting Technology Workshops at the 2012 show held at the Donald E Stephens Convention and Conference Centre, Rosemont, Chicago from September 11 to 13.
Developed over a period of six months or so in the run up to the show, the challenge was to bring a number of laser cutter manufacturers together to set-up and run the same cutter profiles on the same substrates, from the same files and MIS, so that label converters could compare and assess the resulting samples from each machine. Indeed, see just what modern laser cutter technology can achieve, what materials can be converted, how pre-printed reels can be re-registered, what kind of complex shapes can be cut, and how this impacts on cutter speed. Certainly the likes of this exercise has never been attempted before.
The laser cutter participants and machines in the Workshop sessions came from: Spartanics with their L1000Finecut High Speed Laser, with a working width of 350 mm; ABG International with the Sabre Extreme Twin laser and a working width of 340 mm; Delta Industrial Services with its Delta Edge Laser Technology and a web width of 330 mm; and SEI Spa with its Spa Label Master, again with a web width of 330 mm.
The aim of the Workshop sessions was fourfold:
• To set-up and run each laser cutting machine to optimize die-cutting performance and register.
• To understand how pre-printed webs and workflow solutions enable re-registration through laser cutters.
• To find out how to maximize value with complex shapes, cut-outs and laser etching capabilities.
• To compare laser die-cutting results from four different laser cutter manufacturers.
On each day of the show, the four laser cutter manufacturers and machines, in workshop sessions run by a neutral moderator, each set-up and ran four different die-cut jobs, covering prime product labels on a UPM Raflatac polypropylene face material with PET liner, industrial labels on a Flexcon metallized film, blank label shapes on a Green Bay Packaging white labelstock and paper liner, as well as a free-style label of their own choice. Not only were there different jobs, but the label shape and size changed during the run of each job.
Origination for all the set label designs and die-cut files was provided by Esko using their Esko Suite 12. For the prime labels a Cerm MIS system supplied information from estimate to order via JDF to Esko and Xeikon – who pre-printed the prime labels on a Xeikon 330 with inline D-Coat, and also provided a software file to each cutter manufacturer to drive cutting and cutting changes, as well as the MIS supplier.
The origination for the industrial labels, pre-printed on metallized film, was again undertaken using Esko Suite 12, this time in association with EFI Radius and with EFI Jetrion. Step-and-repeat of the designs on the web was done by EFI, including creation of eye-marks for cut-to-print registration for the laser cutter machines, information to indicate changes of logo and cutter during the run, as well as sequential number by laser. The labels were pre-printed on a Jetrion 4900 UV inkjet system, with Jetrion providing a laser cutter software file to each cutter manufacturer to drive cutting, cutting changes and sequential numbering.
A range of variations in blank die-cut label shapes to show some of the complex shapes (including a 40-point star) capable of being produced by laser systems, again originated by Esko and including eye-marks for cut-to-sheet registration, text changes to indicate participating companies, and with the MIS workflow undertaken by Cerm, were prepared and pre-printed on a Mark Andy Performance Series press.
Each cutting machine manufacturer also produced their own free-style label to further enhance just what can be produced on sophisticated laser cutters today. These include complex cut-out shapes, label batching across and along the web, sequential laser etching, and much more. In addition, laser cutter participants were asked to complete a questionnaire, with the answers incorporated into a sample and information pack that attendees could take away. Details of the questionnaire answers are reproduced in this article.
Sessions throughout the show were pretty well attended and created much interest. Undoubtedly the profile of laser cutter technology was significantly enhanced and many more converters will look to invest in laser cutters in the future. So what was learned from these Workshops?
Certainly all the participating companies will have benefitted. Substrate suppliers will have a better understanding of what materials can be successfully cut with a laser, the quality of cutting achieved, and had the opportunity to qualify their substrates through a range of different laser cutting machines.
Esko in turn, has been able to work with the MIS companies, and a number of different digital and conventional press manufacturers – as well as the four different cutter manufacturers – to better understand the requirements for eye-marks for cut-to-print and cut-to-sheet registration, the incorporation of information for changes of logos and cutter profiles during running, the inclusion of sequential numbering information, and the provision of the necessary software file for each cutter manufacturer.
Purchasers of laser cutting systems in the future can certainly be assured that the Workshops have created a greater pool of knowledge and information amongst these industry suppliers that will be of benefit to the industry in the years ahead. But what will converters have learnt from the Workshops? Quite a lot if the message from the demonstrations, presentations and discussions during the show are anything to go by.
So let’s summarize some of the understandings and key benefits of laser cutting technology that were demonstrated at the Workshops:
• Firstly, the technology offers 100 percent savings in cutter tooling. No dies are required, whether flat, rotary or flexible. If a converter has enough die and size changes a day then laser cutting very soon starts to become a very viable option.
• Tool-less laser production offers multiple depth cutting possibilities and can include kiss-cutting, thru-cutting and perforation in one pass.
• Converters using laser cutters estimate that the savings in set-up waste can be as high as 60 percent. Undoubtedly a key benefit in today’s challenging sustainability environment.
• Existing converter users also estimate that there can be as much as a 40 to 60 percent saving in labor costs – a significant element of any converters costing.
• Lasers today can be used to cut all shapes and sizes. There are generally no size limitations, except that more complex shapes will lower the web cutting speed.
• With few exceptions, lasers can cut most types of substrates. PVC is not possible due to the toxic gases given off when cutting. Aluminum foil is also not possible as its wavelength is too close to that of a C02 laser. Otherwise, pretty much anything.
• Apart from cutting, laser systems can be used to etch OCR fonts, one and two dimensional bar codes, serial/sequential numbers and codes. The type of information that can be laser-etched is limitless – and all in one pass with the cutting operation.
• Laser cutters can be used offline with re-registering of webs, or linked inline to digital or conventional label presses.
• There are major possibilities to provide added-value solutions with laser that cannot be achieved with conventional die-cutting.
• When using digital printing from inkjet or Xeikon presses there can be an unlimited print and cut length with laser cutting to provide extended label/banner opportunities.
• Again with inkjet/Xeikon technology jobs can be batched across or along the web to maximise short-run production.
Put together, laser cutting can play a valuable part in a modern label converting plant, working with conventional and digital printing outputs to offer materials and cost efficiencies, reduced waste, added-value opportunities, sequential coding and numbering, and more complex shapes and lengths. The technology has a valuable role to play in the future and more label converters should be evaluating the benefits and opportunities when drawing up their investment plans.
Discussions are now in hand to repeat the Laser Die Cutting Workshops at Labelexpo Europe in 2013, bringing the knowledge, expertise and converter benefits seen in Chicago to label converters in not only Europe but also the hundred or so other countries that converters come from to Brussels. Although still a long way off, it’s certainly worth putting a bookmark in your diary now. Here’s a technology that can help to make a converting business more efficient, more cost competitive, and certainly able to benefit from new added-value opportunities and solutions.
Pictured: The Laser Die-Cutting Workshop featured machines from Spartanics, ABG, Delta Industrial and SEI
This article was published in L&L issue 5, 2012
Stay up to date
Subscribe to the free Label News newsletter and receive the latest content every week. We'll never share your email address.