Shrink sleeves: seaming, converting and application
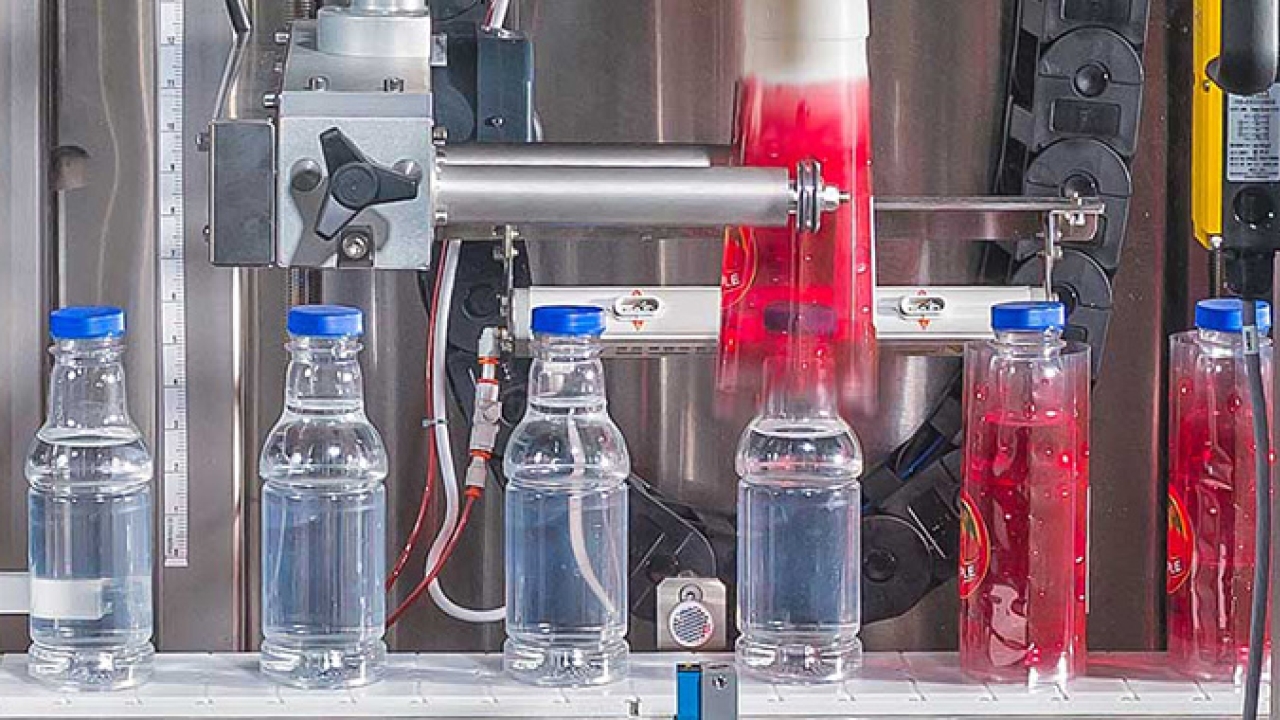
Once the sleeve is printed the secondary converting processes take over. This is arguably the most critical step in converting the printed shrink sleeve stock onto the final product container.
For a best in class shrink sleeve application the converting and the application process need to be aligned and functioning in harmony.
The secondary converting process consists of several steps, the first of which is slitting. The criticality of the slitting process to shrink sleeve converting is important as it has a direct influence on the nature and quality of the slit edges. In shrink sleeve slitting applications the slit edges of the rolls are solvent-welded, which produces an overlapped seam that would ideally be invisible on the finished product. Several factors dictate that shrink sleeve labels be slit using tangential rotary shear technology which is the method that produces the cleanest cut with least impact and stress on the slit edges of the film, thus maximizing the likelihood of a quality, nearly invisible, seam on the finished product.
Having achieved crisp, clean slits without deformation of the roll edges, converters can now progress to the seaming (or welding) step. While the objective is to transform the flat, printed film into a seamed tube, the goal should always be to achieve this with a seam that cannot be seen or felt, while at the same time, maximizing throughput and minimizing waste.
The seaming process requires a stand-alone machine that has several key components. One is the linear perforation section, which is located just before the forming station. The purpose of this perforation is to enable the consumer to remove the sleeve from the container for recycling purposes. Yet another component of the seaming machines is the forming section. This is where the flat web is converted into a sleeve, or tube and where the solvent is delivered to the web. There is typically a ‘nip’ section that is used to control and isolate web tension, while performing an important function of expelling air from the rewinding tube of material. The rewind section on a seamer is also quite unusual in that the unique characteristics of the newly-formed tubular material requires that the rewinding roll oscillates in a very specific and controlled way.
Another critical consideration in the shrink sleeve seaming process is controlling the seaming solvent used to chemically weld the material together. The volume of solvent dispensed must be proportionate to the web speed. This is not only critical to achieving a quality and aesthetically pleasing seam, it is critical to minimizing waste. High-speed seamers require high levels of control to the application of the solvent and are also more demanding as to how the solvent is transferred to the film – with typical options including needle, wick and gravure-wheel designs.
Make-ready or job set-up is always a major focus with print production and converting operations. This is also true in shrink sleeve seaming where the biggest opportunity for efficiency improvement and waste elimination is in setting up the folding area of the seamer. The most advanced approaches on the market leverage fully automatic folding tables, controlled by inputs from a touchscreen HMI.
The seaming process is often followed by a separate finishing step in which a Doctor Machine enables the converter to change the core size (when necessary), change the application rewind direction (when necessary), and remake splices as necessary to ensure that they will pass appropriately through high-speed automatic application equipment.
While converters will be most interested in how to produce a high value shrink sleeve label, it is also necessary that they understand that the application and shrinking process is equally as important in producing a finished product that the brand owner – and ultimately, the consumer – will value.
Converters should always work closely with the manufacturer of the application equipment in-order to understand the specifications and tolerances required of the specific application equipment being used by each of their customers. In other words, there are no onesize-fits-all solutions.
Application technologies
Multiple types of containers, process conditions and film material combinations are experienced in the shrink sleeve marketplace, ultimate success depends on selecting the right combination.
There are three basic styles of shrink sleeve application technologies available:
1. Rotational (carousel) systems
2. Direct apply systems
3. Mandrel systems (sometimes called bullet-style systems).
Carousel systems offer the advantage of facilitating a “squaring” of the sleeves, which allows for better label placement, or rotational accuracy, on non-round containers. A carousel system will often be used to apply shrink sleeve labels to containers such as trigger bottles.
Direct apply systems are used primarily for tamper band applications. The process is simple: the sleeve passes through the tooling, where it is opened into a round formation. As the container being sleeved moves along the conveyor, a guillotine cuts the sleeve, and it is dropped onto the container.
Mandrel (or bullet-style) application systems are the most widely used application systems in the market. They use a mandrel, or cylinder-like tube, over which the sleeve is opened, cut and ultimately driven on to the container moving beneath it.
Bottle shape, the size of the sleeve, and the speed of the line are all variables in selecting the right style of applicator.
Shrink tunnels
Three main types of shrink sleeve tunnels are available:
1. Hot air (Convection)
2. Radiant heat (Infra-Red)
3. Steam (Conduction) Hot air
(Convection) tunnels are versatile and cost effective to use and connect to almost any power source. Hot air tunnels offer directional heat, depending on the type of equipment used, the many different manifolds in these systems enable heat to be focused on those areas of the container that require the most shrinkage. This makes them especially efficient for focused heating on necks, recesses, and grooves.
Hot air tunnels do have some disadvantages. Hot air is not a very efficient medium for transferring heat, therefore temperatures in hot air tunnels are generally higher to enable enough heat to be transferred onto the surface of the film to initiate the shrink process. In hot-air systems too much heat can sometimes affect the leading edge of the container/sleeve, resulting in distortion and producing a poor quality finish. This is particular prevalent with certain container types and process conditions such as a cold filled plastic container, or glass containers. One way to mitigate this issue is to rotate the container as it passes through the tunnel using a ‘spinning’ conveyor.
Radiant heat (infra-red) tunnels are primarily designed for preheating containers – prior to sleeving – in order to mitigate the heat-sink effect of a glass container. However, they can also be very effectively used to shrink sleeves. Radiant systems deliver infrared heat and because the heat remains in the chamber, they create an oven-like shrinking environment.
With the very high temperatures usually found in radiant heat tunnels they create a very harsh shrinking environment with little opportunity to direct heat toward specific areas on a container. Additionally, it can be particularly difficult to get even shrink results. An example is when the leading side of the sleeve entering the tunnel becomes aggressively shrunk before the trailing edge; or, when the sleeve on the two sides of the container are exposed to more intense heat than the leading and trailing sides – resulting in a ‘pulled’ or uneven finished shrink sleeve. A further complication of the high temperatures is the difficulty they can present with empty containers. For example, the task of shrinking a PETG sleeve onto a thin-walled empty PET container can be extremely challenging in a radiant tunnel.
Steam (conduction) tunnels are the most popular medium for most applications as they offer some significant advantages in terms of the process window. They are the most versatile type of tunnel and work well with a wide range of films. Steam distributes heat very evenly to the entire surface of the film as it envelops the container passing through the tunnel. Steam is more than 20 times more efficient in transferring heat than air – which means lower temperatures and the environment in the tunnel is much less harsh.
Despite steam tunnels being the most favored method of shrinking shrink sleeve labels due to their propensity to deliver the most even finished result, their initial installation is likely to be more involved and expensive due to the requirement for a steam generating boiler, as well as the associated piping, extraction, valve gear and drainage. The volume of steam – and hence the boiler requirements – will primarily be dictated by the volume of throughput required of the sleeving line.
There are no one-size-fits-all solutions in the successful application/shrinking of shrink sleeve labels. However, when converting technology and application technology work together seamlessly it is possible to create best in class shrink sleeve labels that meet and exceed brand owners requirements.
Stay up to date
Subscribe to the free Label News newsletter and receive the latest content every week. We'll never share your email address.