Labelexpo Europe 2023 – dies and tooling
At Labelexpo Europe 2023, we saw an increased focus on automation, efficiency and waste reduction on both inline flexo presses and digital press finishing lines.
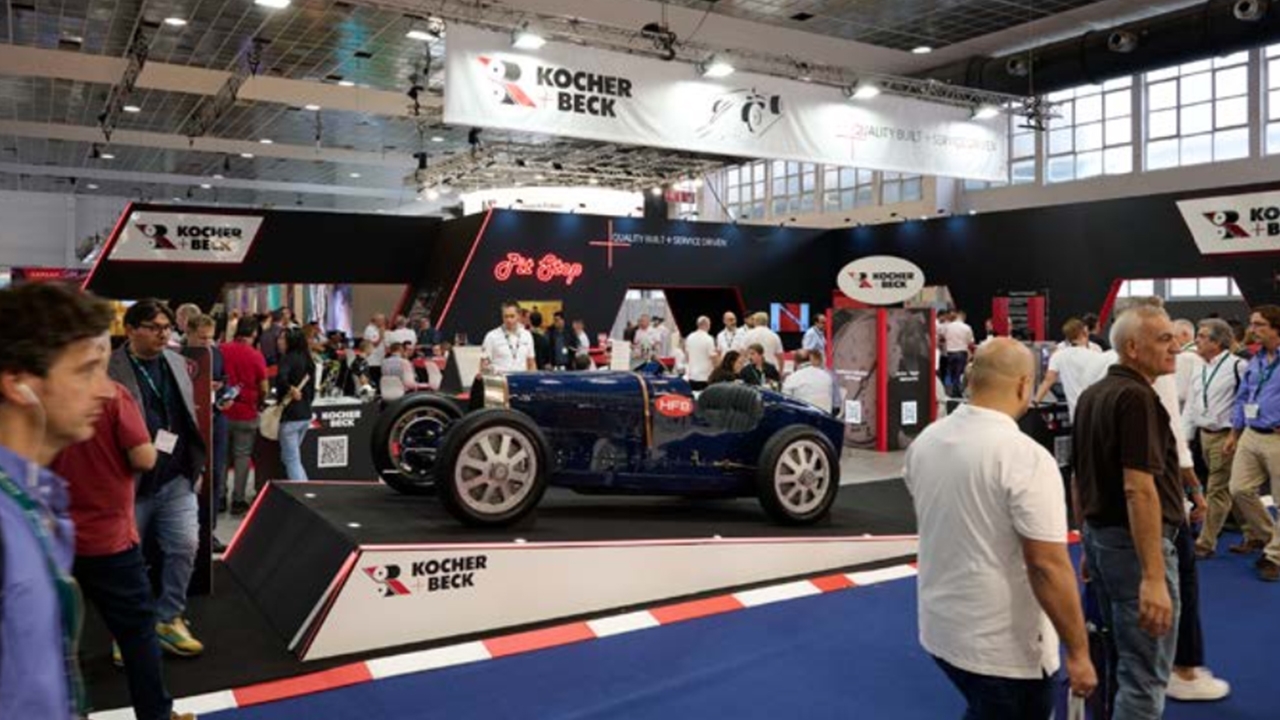
Indeed, there are good reasons to believe that we have reached something of a technology plateau in terms of speed and print resolution of narrow/mid‐web presses, so future productivity gains are likely to come from the increased efficiency and automation of post‐print converting and embellishment operations.
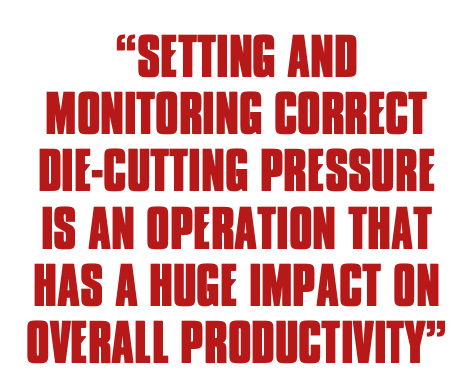
Setting and monitoring correct die‐cutting pressure is an operation that has a huge impact on the overall productivity and waste levels of a flexo or digitally label printing operation. At Labelexpo Europe 2023, visitors saw a continued move towards automation, starting with the introduction of motors to drive pressure settings along with the ability to store and recall jobs.
TECHNOLOGY
Kocher + Beck introduced the Gapmaster EM (Electronic Move), a retrofittable electrical drive unit that replaces the mechanical handle on existing Gapmaster units. Onboard motors allow for easier gap alterations from 0.25 – 10 microns. Adjustments can either be made by touch entry or a rotary dial which provides haptic feedback for the operator while observing the cutting results. Kocher + Beck also displayed its latest KMS digital pressure gauge for detecting changes in cutting pressure.
Maxcess Group, which includes RotoMetrics, showed its AccuAdjust technology designed to solve liner variability issues across all liner material types. AccuAdjust allows for independent or simultaneous bearer adjustment using a digital controller. The system can be adjusted on both sides at a standstill or when the machine is running. Each AccuAdjust unit comes automation‐ready for the upcoming RotoAdjust operator interface upgrade, which will add electronic motors for touchscreen adjustment and Industry 4.0 analytics, along with the ability to store and recall jobs.
Maxcess previewed its next‐generation RotoMetrics Rotoscan adjustable anvil, claimed to be ‘the industry’s first fully automated intelligent die station’ delivering real‐time adjustment for material variation. Proactive monitoring will reduce scrap and waste with Industry 4.0 analytics and one‐touch ordering of new dies. The unit will be commercially available in 2024.
Tecnocut showed its E‐Diffsystem adjustable anvil, designed to control the movement of the anvil roller electronically to +/‐ 1 micron tolerance. It works by replacing the existing anvil roller or any existing die‐cutting unit. The module includes a calibration function to automatically return to zero position and jobs can be stored and recalled.
FLEXIBLE DIES
The main development in flexible dies is more effective coating technologies. Kocher + Beck showed a new FDA‐certified anti‐stick coating that results in less adhesive residue on the cutting edges.
Lartec presented new finishes for flexible dies that provide greater durability and cutting precision. Maxcess introduced a new range of flexible dies, while complete die and rotary tooling systems were also shown by Rotary Sp. z o.o. and Rotary Technology (Guangzhou).
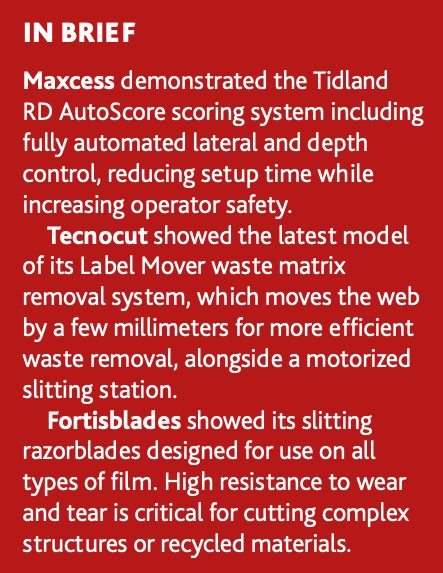
A game‐changer on the converting end of the press and finishing line has been the development of fast semi‐rotary die‐cutting units now installed on both flexo presses and high‐speed digital label converting lines. Omet, for example, demonstrated a semi‐rotary die‐cutting running at 100m/min with fully automated die loading and eject.
Also critical has been quick‐change rotary die‐cutting assemblies. Tecnocut showcased its Pit Stop die‐cutting cylinder system being changed in 30 seconds, while Kocher + Beck demonstrated its quick‐change die‐cutting station.
Stay up to date
Subscribe to the free Label News newsletter and receive the latest content every week. We'll never share your email address.