‘The Label Shop’ is open for business
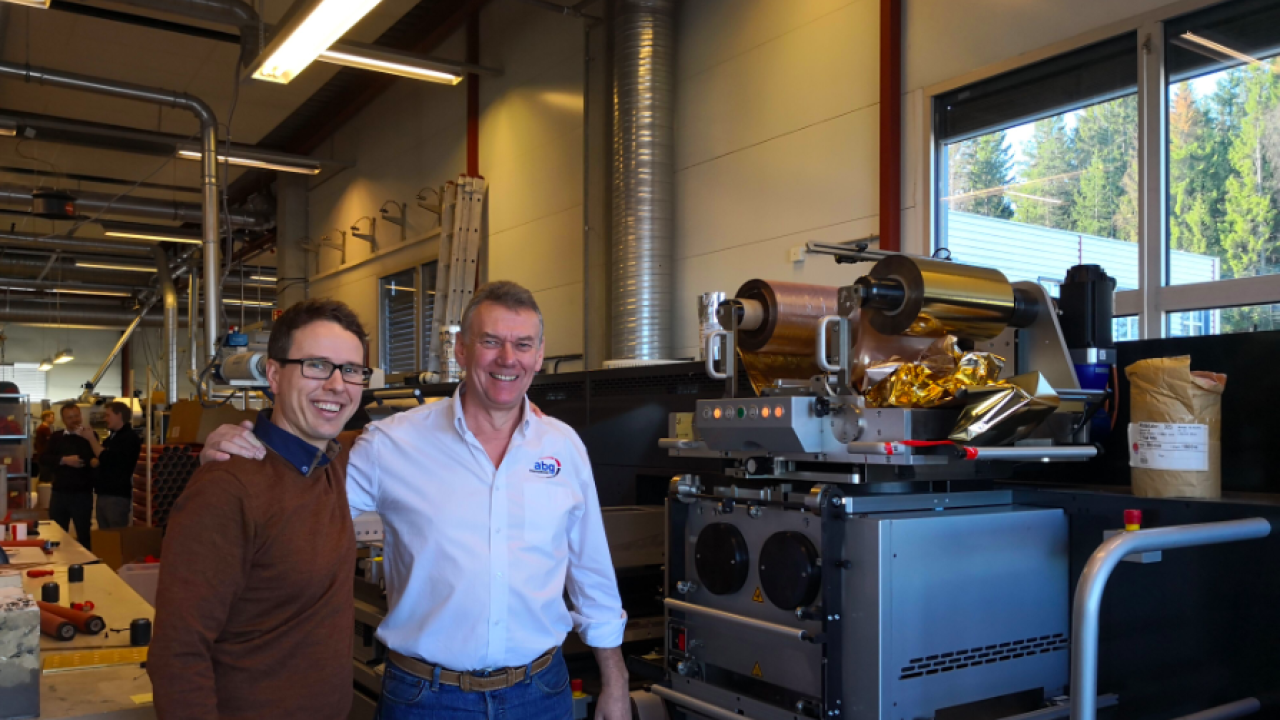
Initially a letterpress specialist, Ellco added digital at the beginning of the 2000s through an HP Indigo ws4050 to augment its production in shorter runs. In 2015, the last of the letterpress machines were retired, with digital taking a prominent place on its shop floor. This sees two HP Indigo Series 3 presses – WS6600 and WS6800 models – supplemented by an EFI Jetrion 4900 inkjet press with in-line laser die-cutting. A 7-color Mark Andy P7 UV flexo press, equipped with hot foiling and screen module, in addition to delam/relam, offers capacity for long runs.
Two AB Graphic Digicon Series 3 finishing lines provide finishing capacity for the presses, while an AB Graphic Omega, installed in 1997, continues to operate. A Daco rewinder is also in action.
Ellco CEO Christian Egedius describes one of the Digicon Series 3 lines as a ‘workhorse’. It includes one flexo station, semi-rotary Fast Track Die module and SGTR turret rewinder with automatic roll labeling. When the converted labels have been rolled up, the machine prints out closing labels with information about the job and attaches them to the rolls, completely automated. This Digicon allows high-speed die-cutting and winding and can produce finished rolls at up to 150m/min. As such, it can be used to produce blank labels as well.
The other Digicon Series 3 features two flexo stations, a Big Foot 50 ton module for hot foil stamping and embossing/debossing, screen printing module and varnishing. This second line is for ‘luxury’ finishing, says Egedius.
Software providing a service
Each major line has been equipped with Lundberg Tech waste handling technology, which serve as a mechanical representation of automation in action at Ellco. These systems capture and remove matrix waste and transport them away from the production environment. This, says Jarl-Andre Skarsten, Ellco quality and development manager, allows press operators to focus on the quality of the output from the presses and generates less downtime.
Label Traxx software provides a more conventional realization of automation through software. This includes Auto Traxx, providing actionable data directly from the machines to the operators. This efficiently captures data on the production floor, including label count, materials used and running press speeds. As well as analysis of a job on the press, this allows jobs to be properly costed, machine performance to be calculated and effective stock management.
Egedius and Skarsten note stock management as a particular pain point for Ellco, especially with its growing number of short runs of digital labels. Production manager Espen Larsen, one of the company’s founders and responsible for one of the Ls in Ellco, identifies that the company stocks around 300-400 types of material. Egedius – son of the founder responsible for the E in Ellco – notes that the company has previously tried to rationalize its stock of materials, but the demands of customers mean it must continue to exploit other ways to manage them.
This is one area where Label Traxx MIS software has been deployed to great success by Ellco. Rolls of material are monitored on press and closing labels are printed by label printers installed at each work station. These provide updated information on the material left on the roll, as well as information for when the roll is returned to the storage area. This area has been reorganized with numbered bays to make finding the required material easier. Quantities of commonly used stocks are even stored near to the presses in order to minimize the time press operators need to spend retrieving rolls from storage.
Ellco has been using Label Traxx since 2015. Since then, the two companies have worked closely to ensure effective implementation of MIS tools. Tim Hollins, business solutions manager at Label Traxx, was present at Ellco during L&L’s visit, where he continued to receive feedback from press operators on how its system could be enhanced. One suggestion includes the ability to queue jobs when loading job data in preparation for printing on the HP Indigo presses.
‘Such features are not native to the software as it was originally designed with conventional printing in mind,’ notes Hollins. ‘It is evolving as more and more printers are using digital presses so require different tools from their MIS.’
Hollins says a ‘superuser’, who serves as a sole point of contact and dedicated resource when looking to integrate MIS into a business, makes the process more manageable and streamlined.
In the case of Ellco, this job fell to Skarsten. He has served as the go-to person within the company when it comes to integrating and evolving Ellco’s use of MIS and data. This extended from the implementation of Auto Traxx to the installation of wireless routers to ensure data is able to be shared around the building.
‘Superusers understand the systems and issues, making it a lot easier to identify and resolve problems before they cause issues in production,’ says Hollins. ‘MIS touches each corner of a business and every member of staff will need to engage with it, so it’s important that it is doing what your business needs it to be doing. A superuser ensures this.’ Skarsten adds: ‘As Label Traxx is an MIS designed for label printers, the support personnel understands our business and the pinch points that might occur, which its software can help us resolve.’
Ellco is now looking to use information to further automate production, with Label Traxx and AB Graphic working together on a project that will see data extracted from the MIS and fed to Ellco’s Digicons to automate finishing. While still in its infancy, this project it set to bring additional benefits to the printer. ‘Through deeper integration, we are looking to future-proof our production,’ says Egedius.
Software providing a platform
Ellco has now started using Label Traxx Siteline software to provide tools to make its front-end processes more efficient and productive.
Siteline is an online self-service system that allows labels and packaging customers to engage directly with a print business. The system allows customers to access their complete order history, access to custom labels and relevant stock labels for easy reordering, and other job-specific data. A new suite of collaboration tools are designed to drive efficiencies in customer interaction and service by allowing direct communication between stakeholders through a single interface.
‘Since we introduced our “Customer Portal” last year we have had a good reaction to the platform,’ notes Egedius, although Skarsten says: ‘More customer should be using it.’
Going a step further, Ellco has launched Etikettbutikken (‘The Label Shop’), a concept that allows new customers to directly order small batches of labels (see boxout). Built on Chili Publisher, the portal provides inspiration and access to simple editing/creation tools so direct customers can quickly and simply place orders to fulfill their printed label needs via the Ellco website, www.ellco.no.
Egedius notes that this has yet to gain much traction as the company has not been pushing it due to the portal requiring further development, but it will provide additional revenue streams for Ellco in the future.
‘We want to be the best label printer in Norway and are investing in our tools and services to make this a reality,’ concludes Egedius.
Stay up to date
Subscribe to the free Label News newsletter and receive the latest content every week. We'll never share your email address.