Andy Thomas-Emans column: Flexography reaches new landmark at Labelexpo Americas
The extraordinary degree of automation seen on mid-web flexo presses at Labelexpo Americas 2024 shows how far the technology has come
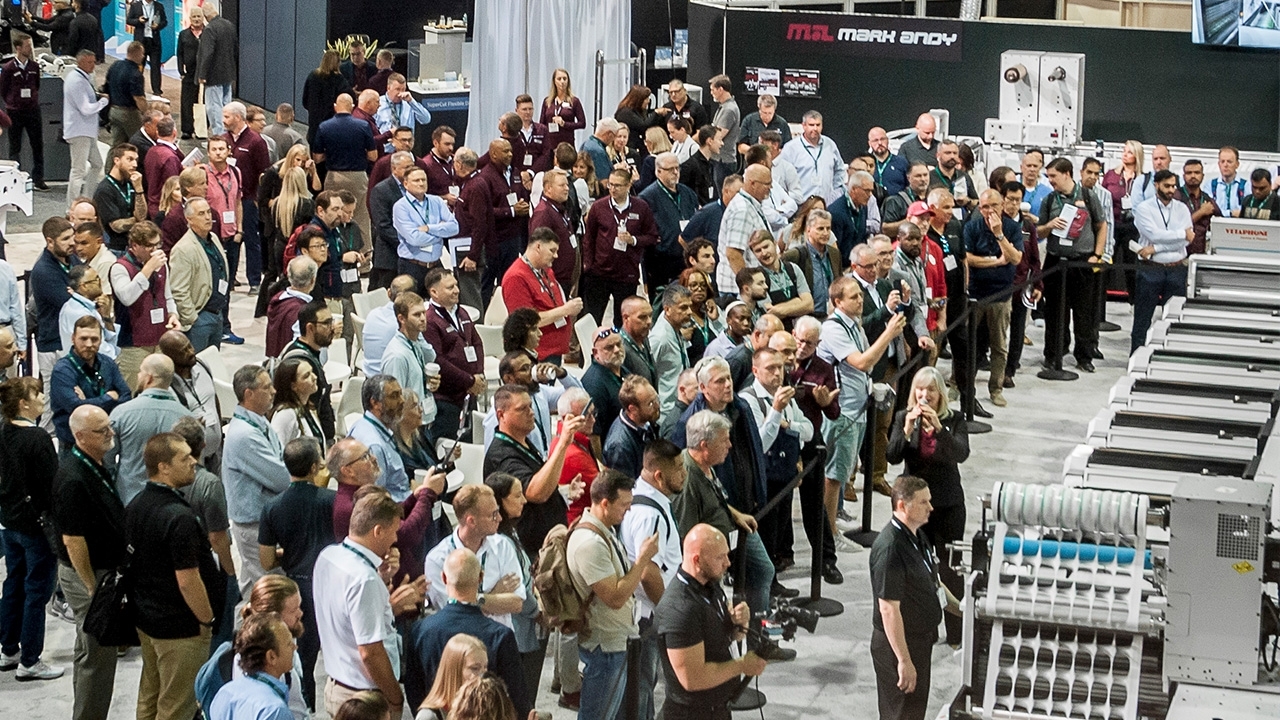
When looking back on the last 35 years of writing about the printing industry, certain things stand out as landmark events.
To name a few: the first fully automatic plate change on a Komori offset press in 1990; the first Indigo E-Print and Xeikon DCP-1 (badged Agfa Chromapress) at ipex 1993; the first close-up sight of a servo drive in action on a Nilpeter FB330S in 2005.
I thought about these landmarks on the Nilpeter stand at Labelexpo Americas 2024, watching a 670mm (26in)-wide FA-26 ramp up, whisper-quiet, from makeready to full speed of 250m/min (820ft/min) and back down again without the operator touching the press. Web tension and pressure were adjusted automatically, and registration was controlled by a newly developed color-based camera system. Just to prove the point, the press was deliberately thrown out of registration and automatically recovered.
Because the press was using extended color gamut inks, the only changeover in roll-to-roll format (assuming no roll change) was exchange of plate sleeves, carried out in a matter of minutes, then hands off.
Memory lane
Seeing this degree of automation and precision on a machine of this width, even given the ‘ideal’ conditions of a trade show, took me back to my first encounters with flexo presses in the 1990s. To change over an 8-color 13-in/330mm 8-color press took a sizeable press crew most of the morning. Laborious washdown; tools required to disassemble and reassemble printing group components; the need for constant manual adjustment of print pressure, registration and tension throughout the print run, requiring time-served professional operators; the quality gap between flexography and letterpress/offset.
Quite understandably, we tend to focus on the extraordinary technological innovation that has driven digital from a rather flaky start to full-blown industrial strength, both toner and inkjet.
But watching that FA-26 demo forcibly reminded me of the extraordinary strides flexography has made over the same period.
This has happened across the entire flexographic ecosystem. Not only increased automation but the continual development of new photopolymer materials, better screening and film/plate imaging systems, and new anilox coatings and engravings, all of which brought flexo quality ever closer to offset.
Along with increased press stability, this also allowed extended color gamut ink systems to migrate from offset to flexography - a tougher ask for flexo because of the greater number of variable factors involved from dot gain, to double-sided tapes, non-standardized inks and anilox. Now, ‘digital color’ is here to stay for flexographic printers, allowing easier color matching with digital presses and eliminating the need to wash down the press between jobs.
Flexo has been driven down this road by many factors: firstly, by the looming threat of extinction for even medium run lengths at the hands of digital printing. Secondly, by the increasing difficulty in finding skilled, time-served flexo press operators, which required that as many manual processes as possible be automated. The increasing availability and ubiquity of servo-drive technology over this period allowed flexo presses to be increasingly robotized.
“Labelexpo Americas also demonstrated how far flexographic presses can be integrated into modern factory workflows”
Mid-web presses are where we see the pinnacle of automation, and of course, it is not only Nilpeter on this road. At Labelexpo Americas 2024, Mark Andy launched its own highly automated 26in press, the Performance S9 – expect a full review of that machine in a future edition of L&L – and Lombardi was showing a print group from its own Invicta mid-web press, which displays equally high degrees of automation and versatility.
Labelexpo Americas also demonstrated how far flexographic presses can be integrated into modern factory workflows, reporting production data in real-time back to a Cloud-based server and with the ability to store and recall press settings for rapid set-up on repeat jobs. The next stage has to be the development of open-standard press operating systems to allow direct download of job data from an MIS, avoiding the need to double key at the press console.
Digital integration
Another aspect of digital integration shown by both Nilpeter and Lombardi at Labelexpo Americas is the ‘digital twin’ or ‘digital shadow,’ a real-time animated model of the press that records all aspects of job set-up, running and changeover. These recordings can be re-run for training, process optimization (think slow-motion replays for sports coaches), and real-time remote monitoring.
The benefits of flexo automation have flowed down in different degrees, even to entry-level machines. Also – very importantly – to the new generation of hybrid inkjet-flexo presses. The ability to automate flexo print and converting modules reduces the time the digital engine is idle, reduces waste during makeready and reduces the need for skilled operators.
This has indeed been an extraordinary journey for flexography.
Stay up to date
Subscribe to the free Label News newsletter and receive the latest content every week. We'll never share your email address.