Partnership strengthens plastic pallets for the printing industry
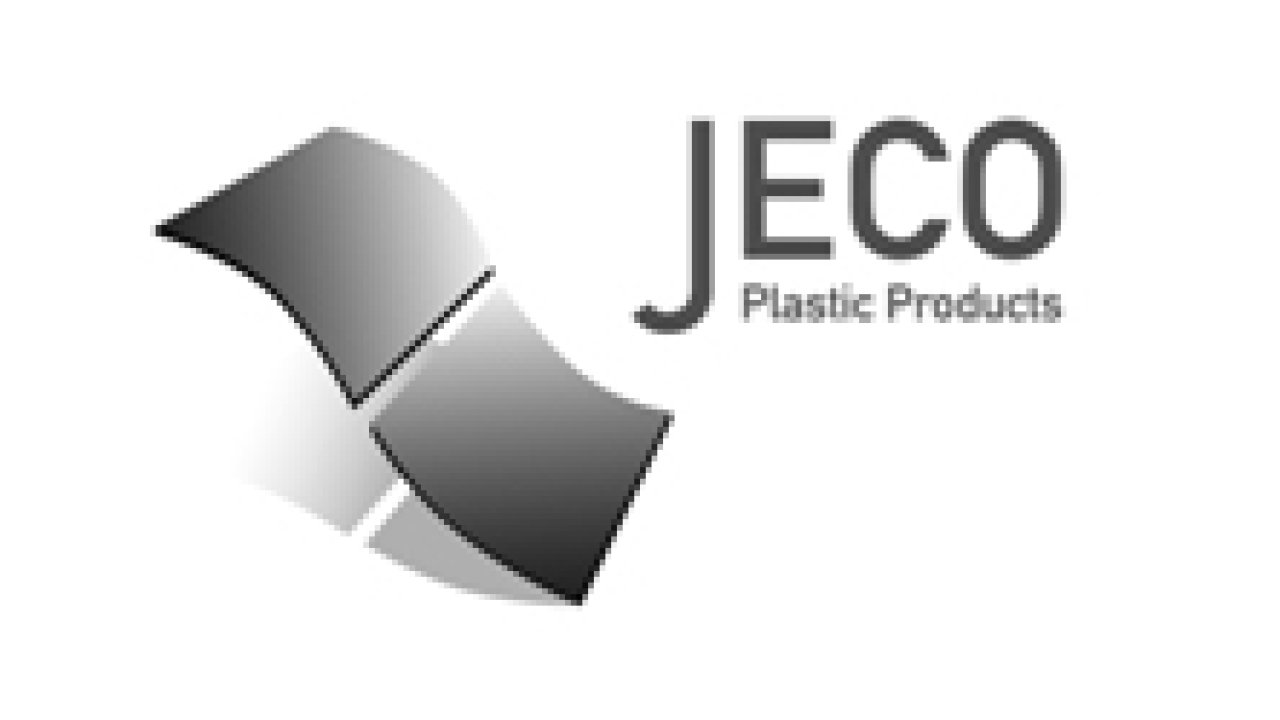
Jeco Plastic Pallets, a US designer and manufacturer of plastic pallets and containers for the worldwide printing industry, has worked with Indiana’s Purdue University and the US National Digital Engineering and Manufacturing Consortium (NDEMC) to show the performance characteristics of plastic pallets, and make structural changes to strengthen an existing pallet design.
Jeco designs and manufactures durable pallets and containers for the worldwide printing and automotive industries, as well as other industries handling heavy product which must be protected from damage. The printing markets Jeco serves include sheet-fed, web offset and roll printing, with solutions tailored for a number of press manufacturer technologies, including Komori, Heidelberg, Bobst, KBA and manroland. Jeco production facilities include rotational plastic molding and thermoforming capabilities unique in North America, while Jeco said its designers employ complex plastic compounds to impart dimensional stability and structural integrity to its products.
The collaboration between the plastic pallet designer, Purdue University and NDEMC allowed Jeco access to powerful computers that were used to perform stress calculations and demonstrate to customers that plastic pallets can perform as effectively as metal pallets in many situations. Jeco was also able to significantly strengthen an existing pallet design by making structural changes as a result of detailed analysis.
Jeco Plastic Products chief executive officer Craig Carson said: ‘Our work with Purdue University and NDEMC put powerful tools in our hands and enables Jeco, a relatively small company, to differentiate ourselves and demonstrate that our products are superior to those made of metal in many cases.
‘Jeco plastic pallets are stronger and last significantly longer than wooden pallets. They are much lighter in weight than metal pallets, and can be designed to hold much larger loads than would seem possible. The calculations we now can do enable us to develop plastic structures for a wide variety of applications.’
Stay up to date
Subscribe to the free Label News newsletter and receive the latest content every week. We'll never share your email address.