Breaking the UV barrier
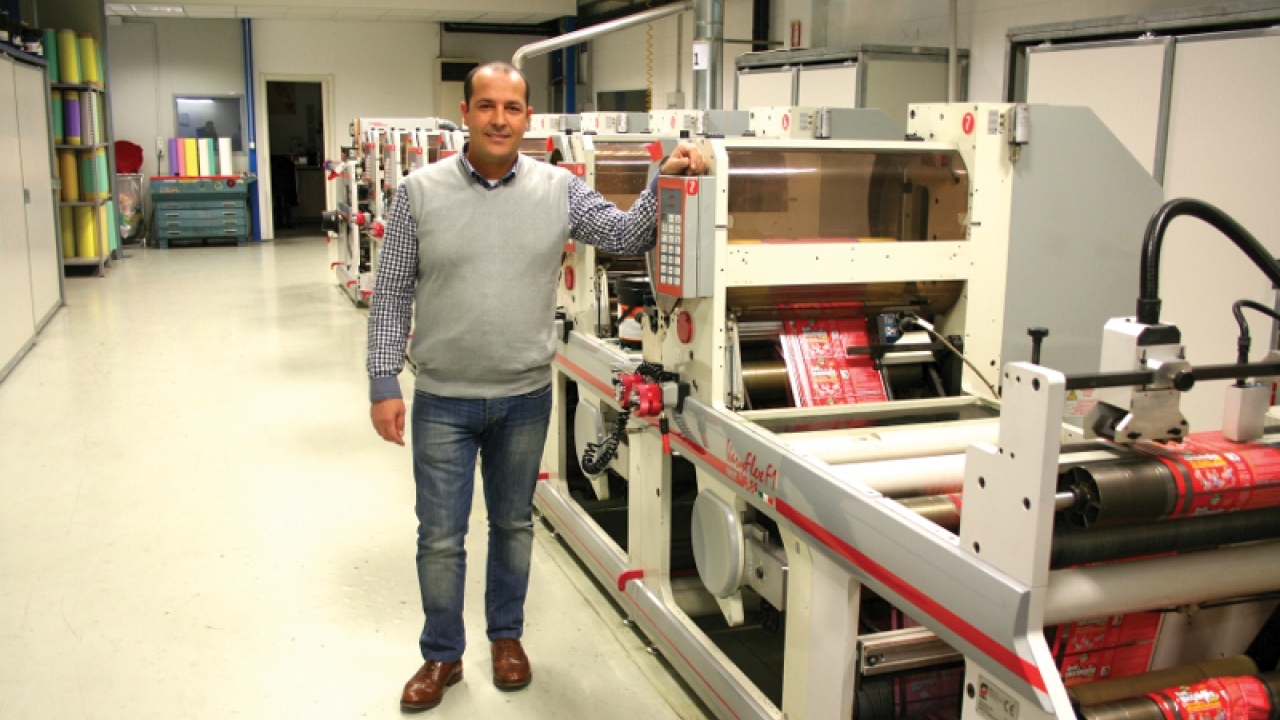
From a small business in the transport sector, to pioneer of UV printed flexible packaging, the story of Massimo Raffaele’s ACM is an impressive one. Andy Thomas reports
Printing food packaging with UV inks is one of the most challenging applications a converter can consider. Many end users in the food sector will not consider UV, and the sector is dominated by wide web CI flexo or gravure presses using solvent or water-based inks.
However, as the run lengths of flexible packaging have come down, there is increasing interest in producing shorter runs on narrow/mid web presses where the benefits and techniques of UV curing technology are well understood – indeed, they are the dominant mode of production.
Italian converter ACM, located in Cremosano, near Milan, has built its business around convincing end users that UV printing of flexible packaging and film labels holds no more risk of migration, odor or contamination than the solvent and water-based inks they normally specify.
ACM takes on not only the printing and lamination of flexible packaging materials, but also handles all necessary testing to guarantee that the printed product is suitable for the food sector – which has extremely demanding compliance requirements.
Massimo Raffaele, managing director of ACM, says he is the first UV flexo printer in Italy to specialize in flexible packaging for the food sector. ‘Up to now, nobody before ACM has used UV for food contact applications and guaranteeing the result – it is that simple.’
Around 95 percent of the company’s work is for the food industry, and includes flexible packaging, sachets, pouches, aluminium lids, wraparound labels and shrink and stretch sleeve labels. Some 80 percent of jobs are carried out directly for end users and 20 percent for contract packers.
‘The global economic crisis meant everyone started looking for short run solutions,’ says Raffaele. ‘Short runs with more variations are what our competitors cannot do. ACM can turn any job around without any problem, from receipt of artwork, including print, lamination and delivery, within one week.’
What are the benefits of UV for flexible package printing? ‘UV printing provides higher quality and the inks are very bright and high quality compared with the competition,’ says Raffaele. ‘It is also more environment friendly not to use solvent inks, and this is a major selling point for us.’
Continues Raffaele: ‘Back 15 years ago there were big problems for UV in food applications, but we have invested a lot of money in demonstrating it is safe.
It has not been hard to convince our clients of the quality, which they can take for granted, but it has been hard to prove that this material can be safe. We have collaborated with outside companies and spent a lot of time and money developing the present testing procedures, which are very strict.’
A lot of the major brands in Italy and abroad have already moved from solvent to UV flexo printing with ACM.
A very important element of customer confidence is ACM’s BRC/IOP hygiene accreditation, which is emerging as the key global standard for food hygiene at label and packaging converting plants.
As well as flexible packaging, ACM has successfully taken on short and medium run shrink sleeve label work. ‘We have reached remarkable results even in such a case, which has been appreciated by the large brands commissioning the job.’
ACM has also carried out its own product development concerning re-sealable packs with a patented system, which combine pressure-sensitive and laminating technologies.
UV partnership
To carry the UV flexo project through, ACM developed a close working partnership with press manufacturer Omet and ink supplier Flint Group, ‘because they had a deep understanding of the issues in UV printing,’ according to Massimo Raffaele.
ACM purchased a 7-color 530mm wide Omet Varyflex F1 UV flexo press configured with a web cleaner, corona treater, UV lamps with progressive power adjustment and chill drums, as well as Omet’s automatic register control system which subsequently keeps register without operator intervention.
‘The Omet is a great machine – high quality and easy to set up,’ says Raffaele. ACM prints with laser engraved plates.
The Varyflex has successfully printed films down to 12 microns, as well as some carton work which takes advantage of the machine’s capability to handle boards up to 300 microns.
After printing, all materials are laminated off-line on Comexi Nexus Evo and Dual solventless laminators, so there is never any direct contact between UV inks and foods. The laminated rolls are stored at 25°C to allow the glue to dry, which takes around 24 hours, and then sent for migration tests.
ACM has successfully tested the recyclability of PE materials printed with UV inks. ‘This is no problem, but no customer is interested at this stage,’ says Massimo Raffaele. ACM also has a ‘bio’ materials range, which is a sustainably sourced paper laminated to a clear film.
Having established its reputation in mid-web UV flexo, ACM now plans to expand its capabilities into the wide web, long run sector with the installation of a 1200mm-wide UV CI flexo press by the end of this year. ‘A lot of our customers for shorter run flexible packaging products started to make enquiries about at least 900 mm web width to eliminate production waste – but always printing short runs.’
The company is also constructing a new 1,500 sqm production building, which will consolidate its production facilities on one site, greatly increasing productivity.
Pictured: Massimo Raffaele with Omet Varyflex F1 UV flexo press
This article was published in L&L issue 3, 2011
Stay up to date
Subscribe to the free Label News newsletter and receive the latest content every week. We'll never share your email address.