Etipress enjoys Colombian cosmetics boom
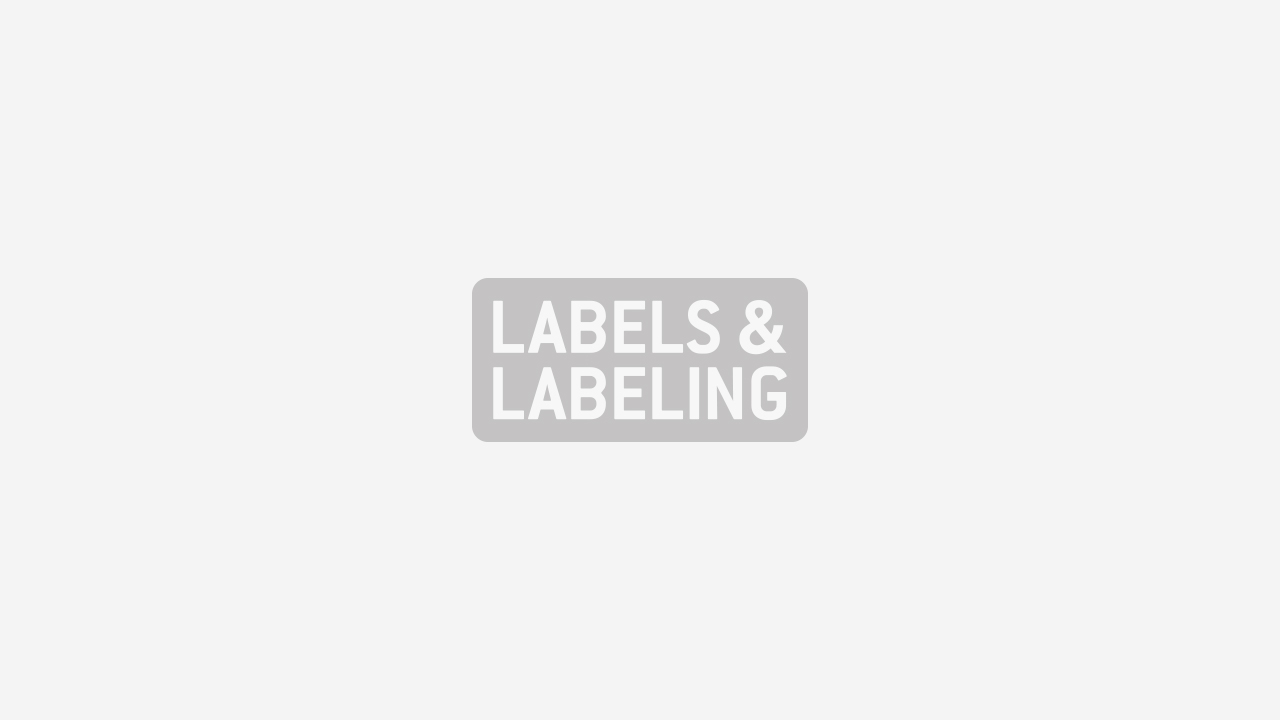
Colombian converter Etipress reports strong growth in cosmetics and pharmaceuticals, but is cautious about the impact on local industry of the new free trade agreement with the US. James Quirk reports
Colombian label converter Etipress, based in the capital Bogota, reports strong growth in the cosmetics and pharmaceutical sectors as the country’s label industry continues to benefit from rising local consumption.
Colombia is one of the region’s recent success stories thanks to a burgeoning middle class, increased political stability, and strong GDP growth stimulating internal demand. Foreign direct investment increased by 500 percent between 2001 and 2011. The economy has seen annual growth of four to six percent in recent years and is closing in on Argentina as South America’s second largest.
A free trade agreement with the United States came into force in June 2012, a move widely interpreted as positive for Colombia’s economic growth. Though Etipress general manager Jorge Pabon expects material prices to be reduced as a result, he also expresses a word of caution, believing it could lead to a decrease in the number of products being manufactured – and therefore labeled – locally.
‘More finished products will be imported,’ he says, ‘instead of being manufactured and labeled locally. We need more local industry, whose products we can label, instead of importing so much.’
He cites the example of a Unilever body cream which used to be manufactured in Colombia, for which Etipress printed the labels. Handing the account led the company to install an Omet Flexi 330 UV flexo press in 2004 so it could provide the screen printing and coldfoil effects desired by the client. But production was later moved to Mexico, so Etipress lost the business.
Pabon, who used to work for Unilever, is more optimistic about rising local consumption, and he sees growth across a number of end user sectors including food and beverage, pharmaceutical, cosmetics and lubricants.
Pharmaceuticals and personal care are two of the key end user sectors for the company, each taking roughly 30 percent of production, and the latter making up the bulk of its shrink sleeve production. Lubricants, food and beverage fill the remaining 40 percent.
‘Growth in the personal care and pharmaceutical sectors has stimulated the company’s progress,’ reports production director Hernan Saldarriaga.
Etipress produces 190,000 sqm of self-adhesive labels and 1.3 tons of shrink sleeves a month. Its 106 employees are housed in a 3,200 sqm factory in Bogota, with sales offices located in the cities of Cali and Medellin.
Around 10 percent of production is exported to the likes of Costa Rica, Ecuador, Panama and Venezuela. Jorge Pabon says there is potential for this to increase, particularly in Central America, the Caribbean and Venezuela.
Production
Founded in 1992, Etipress began printing labels with a 5-color Ko-Pack letterpress with inline priming. A second – this time of six colors – was installed in 1995 and a third, a 9-color press, arrived in 2002. In between Ko-Pack installations, Etipress added a flexo press from Focus Label Machinery and a Galaxie Screen printer from Smag.
The 8-color Omet press, installed in 2004, is equipped with screen and coldfoil units and produces both self-adhesive labels and shrink sleeves, for which the company runs equipment from Karlville. The press is described by Pabon as a ‘reliable and cost-effective machine’.
A second Flexi 330, of the same specifications, was added in 2010, but not before the company had branched out into digital printing with an HP Indigo ws4500 and AB Graphic Digicon finishing machine. ‘We saw an interesting opportunity to cater to the short run market and variable data printing,’ explains Pabon.
Further offline finishing equipment includes two Rotoflex inspection rewinders, a laser cutting system from SEI, a hot stamping machine from Newfoil, and two rewinders from Converting Equipment International with BST inspection.
Letterpress platemaking takes place on equipment from Anderson & Vreeland. Photopolymer plates for UV flexo printing are supplied externally, but the company intends to bring this in-house in the future.
Pabon reports that Bogota’s local government is becoming more demanding with regards to environmental sustainability. Etipress has achieved two of the four steps in the local government’s PREAD program of local environmental excellence, but Pabon says that the main motivation to be more sustainable comes from within the company itself. ‘The clients also appreciate it,’ he says, ‘even if they don’t necessarily demand it.’
Waste is separated and taken away for recycling by authorized companies. No solvents are used, and certification to ISO 14001 is planned as the next step in increasing Etipress’ environmental sustainability.
Pabon reports that the company is considering investment in offset printing technology in 2013, citing its quality and suitability for inline combination printing.
Pictured: A view across the production floor at Etipress’ factory in Bogota
This article was published in Labels & Labeling issue 1, 2013
Stay up to date
Subscribe to the free Label News newsletter and receive the latest content every week. We'll never share your email address.