Liners in focus
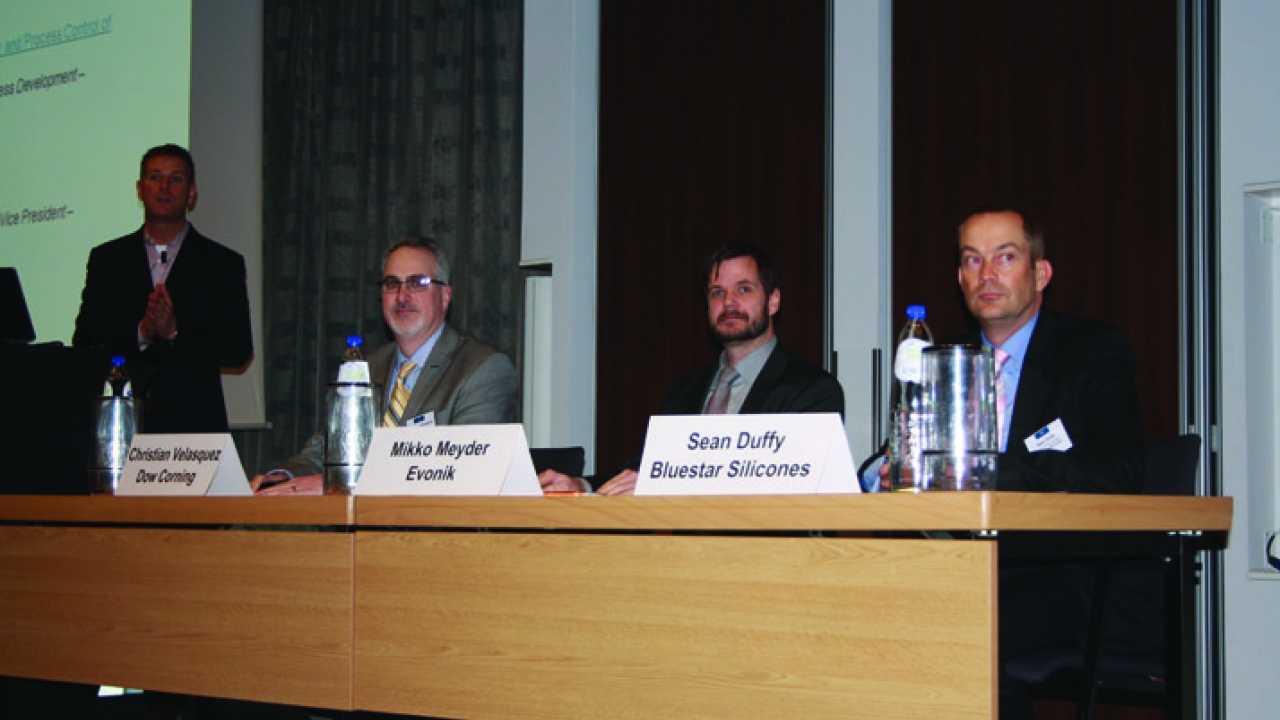
The latest developments and trends in the release liner market were discussed at AWA’s annual release liner conference. Carol Houghton reports
Despite the economic uncertainty facing the world economy, the release liner industry is expecting worldwide growth in 2012 to average between three and 10 percent. According to the latest research into the sector from industry consultants Alexander Watson Associates, the strongest long term growth prospects are seen in the emerging markets of Eastern Europe, Latin America and Asia-Pacific. Indeed, while North America and Europe each account for just under one third of world liner volume, Asia Pacific already consumes 28.6 percent.
At the same time, AWA’s research shows continued consolidation across the release liner supply chain, not just in Europe and North America, but also in developing markets, while raw material costs have increased dramatically along with energy, labor and transport costs. These increases are expected to continue through 2012, though at a reduced level.
Carsten Lange, managing director release liner, coatings and consumer packaging at Mondi, told delegates that the release liner industry needs to do better at supplying good statistics. Many suppliers are now part of groups which do not report, and there is very little comparable data for raw materials, said Carsten: ‘At best, pulp price is an indication.’
He cited GDP growth issues in Southern Europe as a main concern for the industry, as well as challenges for the Eurozone as a whole, which accounts for 25 percent of the global economy.
‘We should organize ourselves to be stronger for growth opportunities and take care of the future – and it is possible it could be a negative one,’ he warned.
Application specific
Corey Reardon, president and CEO, Alexander Watson Associates (AWA) looked at the segments where release liner is experiencing its highest growth – particularly labels, tape and hygiene. ‘The results are skewed by the label market,’ he said. ‘We could have a whole conference on that!’
In terms of materials and markets, glassine/calendared kraft papers still represent a solid 41 percent of the overall release liner market, with film currently taking 12 percent. Pressure-sensitive labelstock remains the largest segment, at 51 percent. Reardon predicted that, ‘In this market, 40-60 percent of liner usage for primary product labeling will migrate to film in the next five years.’ He added that variable information print – itself representing 50 percent of the label market for release liner –- will, however, always remain paper-based.
Mikko Meyder, Evonik agreed there will be an increase in the use of filmic materials, driven by the ability to produce lower gauges. Sean Duffy, Bluestar Silicones added, ‘People are beginning to look at the feasibility of film liner in terms of recyclability, sustainability and cost as well as the possibility of UV curing.’ But Duffy believes the evidence does not support the idea that film will overtake paper. ‘Paper still has a decent future.’
Peter Sandkuehler, group leader, TS&D, performance plastics, for Dow Chemical Company, identified a trend for experimenting with LDPE for release liner stock. However, stiffness and optical balance requirements present a challenge here.
Sustainability
Jackie Marolda, senior consultant and vice president AWA, looked at issues surrounding sustainability. ‘Recent innovations include the downgauging of PET to create lighter weight rolls. We can also expect to see paper-based thin liners as well as substitution trends such as linerless.’
She continued, ‘Linerless doesn’t work for everything – but it has found its opportunity and is creating value there.’ Linerless offers numerous benefits: eliminating the cost of buying and disposing of siliconized liner; allowing use of butt-cut label formats; more labels per roll – meaning fewer changeovers – as well as more material per pallet which reduces shipping costs.
However, it does have limitations in terms of materials – facestocks, adhesives and printable silicone coatings – application machinery and application speeds. Marolda says the industry is developing hybrid application equipment to apply both linerless and traditional PS labels. There is also a problem with label shape as complex curves cannot be die cut. However, ‘We can print a shape on a square clear film label to create the same effect,’ she explained.
Marolda also identified a major change in value chain relationships, with raw material suppliers beginning to pair with machinery suppliers, such as Innovia Film’s collaboration with Ravenwood Packaging on linerless labels. Sean Duffy, Bluestar Silicones agreed: ‘Collaboration is key to making the industry more efficient.’
Mark Macaré, public affairs/issues and recycling manager at Finat, looked at European Union directives affecting packaging and packaging waste, as well as corporate drivers. Walmart, for example, is looking to reduce packaging by five percent by using supplier sustainability assessments. Macaré said that 70 percent of all brand owners now identify ‘sustainability’ as a competitive advantage.
Macaré identified recycling bottlenecks for both PET/PP and paper liner. ‘Used liner is generated downstream in a “fragmented chain” causing logistical problems in addition to a lack of awareness and urgency at the end user. There is also a problem with pan-European ownership. We have seen a limited number of success stories and lack of volume.’
Pictured: The panel session: (L-R) Corey Reardon, president and CEO, AWA; Christian Velasquez, Dow Corning; Mikko Meyder, Evonik and Sean Duffy, Bluestar silicones
This article was published in L&L issue 2, 2012
Stay up to date
Subscribe to the free Label News newsletter and receive the latest content every week. We'll never share your email address.