Uflex develops new film for blister packaging laminates
The Films division of Uflex has launched a polyester film that can replace the top and bottom substrates of the conventional cold formed Alu–Alu laminate in blister packaging.
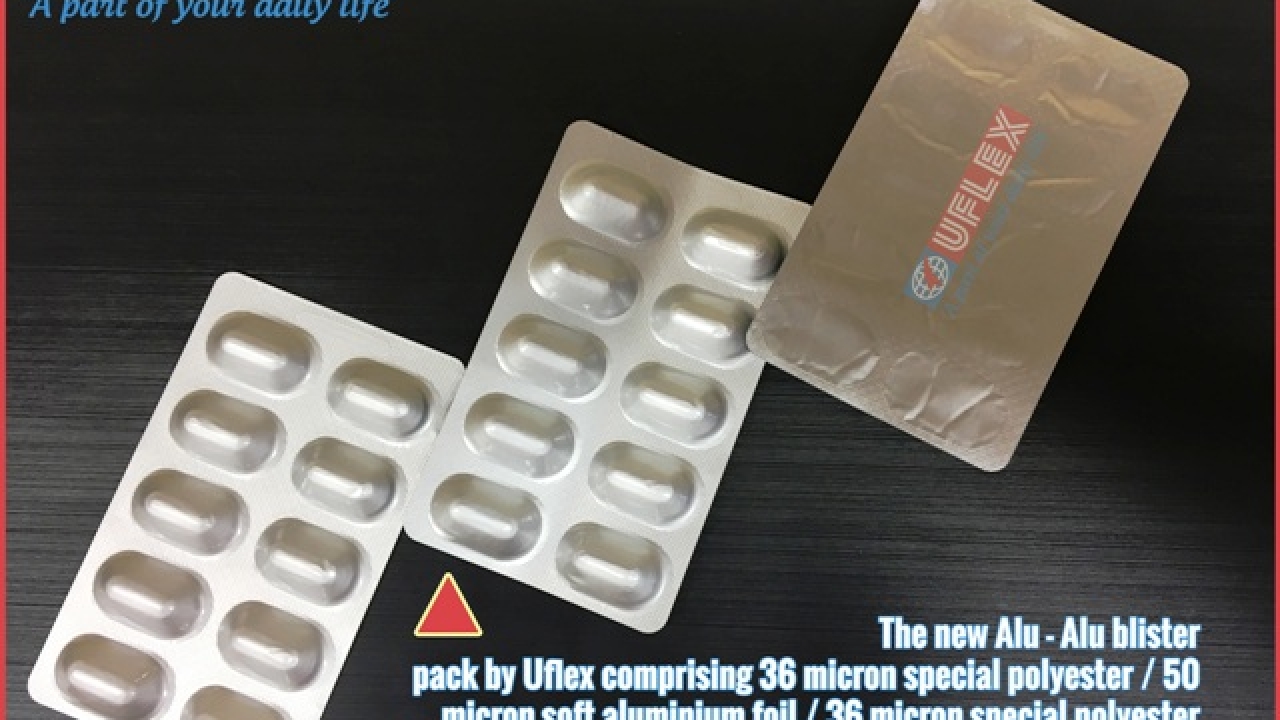
This specialty film can be laminated on both sides of the aluminum foil. Uflex engineers have utilized metaphase morphology to form the film in Z direction, which is a pre-requisite for blister packaging. The new structure is comprised of 36 micron special polyester, 50 micron soft aluminum foil and 36 micron special polyester.
Dr Sudhir Naik, senior general manager, corporate technical services, Films at Uflex, said: ‘Getting better functionalities as compared to the Alu-Alu laminate structure comprising BOPA, aluminum, foil and PVC, this film will have significant and substantial benefits for the converters catering to pharmaceutical brands. BOPA (BON) is imported in to India from countries like China, Korea and Taiwan. Convertors are left with no option other than managing varied inventories of BON and PVC films separately. With the introduction of specialized polyester film that will now be laminated on both the sides of aluminum foil, the logistical hassles for convertors will surely go down. The dependency on import of BOPA will also go down as the converting industry gradually switches over to this film for cold forming the blister packs. This film therefore makes a strong case for import substitution in India.’
Speaking of the technical characteristics of the new polyester film, Pramod Sirsamkar, president of technical and new product development in the Films division at Uflex, said: ‘The moisture absorption of this specialized polyester film is as low as 0.8 percent working out to almost 92 percent less than that of nylon, which is a big advantage. Aluminum foil offers negligibly low oxygen and water vapor transmission rates. Such high barrier may not really be required by the drug packed inside. We are, therefore, also working towards offering high barrier yet thinner specialty polyester films as an alternative to aluminum foil that may further lead to the reduction in overall weight of the ensuing laminate. The introduction of specialized polyester film in Alu-Alu blister packaging has also opened up avenues for us to come up with biodegradable and oxo-degradable variants further minimizing carbon footprints.’
Amitava Ray, executive director and head of packaging and converting business at Uflex, added: ‘There is also a yield benefit in the case of the new laminate structure but with no compromise on functionalities whatsoever. This lightweighting of the laminate equates to lesser energy consumption at the three critical stages of the flexible packaging lifecycle, namely manufacturing, transportation and disposal. The reverse printing on the special substrate has further opened up the avenue for enhanced brand visibility. We also stand in good stead to offer specialized and technologically advanced anti-counterfeiting features for the new Alu-Alu laminate. We are ready with the product and are working with leading pharmaceutical companies for the commercial rollout.’
Ashok Chaturvedi, chairman and managing director, Uflex, concluded, ‘This is innovation with value added differentiation at its purest that addresses the shortcomings of both BON and PVC films faced by convertors catering to the pharmaceutical companies. This film is a great product for the pharmaceutical packaging industry that will raise the bar for competition both in India and overseas thereby being a gamechanger. When the bar for competition is raised, the flexible packaging industry as a whole stands to benefit both in terms of quality as well as technology.’
Stay up to date
Subscribe to the free Label News newsletter and receive the latest content every week. We'll never share your email address.