Reversing the trend
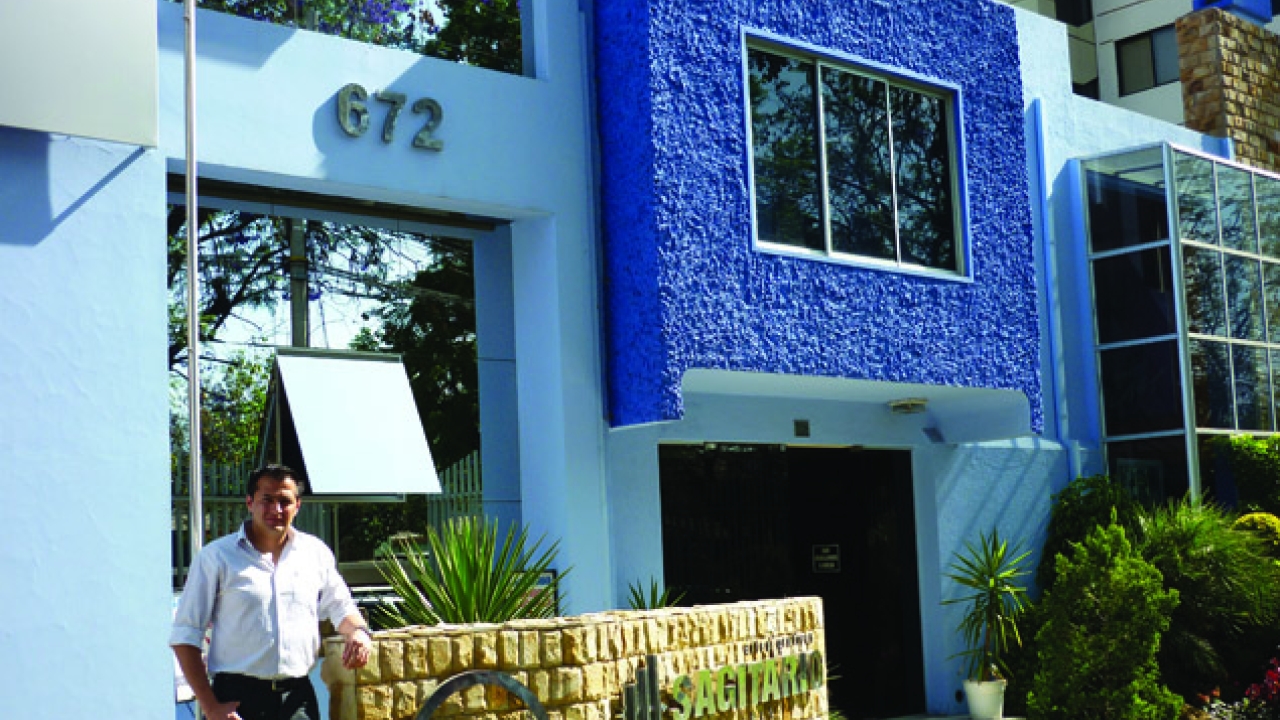
Bolivian end users are used to importing their labels from abroad. Now, the country’s first narrow web converter is taking advantage of the gap in the market. James Quirk reports
The foundation of Bolivia’s first dedicated narrow web label converter – and its subsequent investment in machinery from Gallus, Nilpeter, Rotoflex and Karlville – is a story representative of three major trends in some of Latin America’s lesser developed label markets: the creation of local label converting operations to serve brands owners accustomed to importing labels from abroad; the increasing installations of top quality machinery; and the desire to export.
Brazil, Mexico, Argentina and Chile may dominate the headlines – all four boast local label converting operations that compare favorably in technology and quality with Europe and the USA’s finest. But the smaller markets of Bolivia and Peru – even Ecuador and Paraguay – are increasingly attracting high quality machinery as local companies seek to reverse the trend of end users importing labels from abroad.
In Peru, Kuresa, the country’s leading producer of prime labels and adhesive tapes, has just invested USD 23 million US dollars in a new facility. Grupo Fibrafil, a manufacturer of agricultural netting and twine in the same country, will shortly open a dedicated label division housing two new Nilpeter FB presses. In Bolivia, packaging supplier Industrias Ravi is on the point of establishing a local label converting operation in cooperation with Argentine printer Artes Gráficas Raal. You can read about all three of these stories in upcoming issues of L&L.
These smaller Latin American markets have traditionally imported the majority of the labels used on locally sold goods. But now, companies in these countries are increasingly taking advantage of the gap in their local markets.
Bolivian brands historically import their labels from more developed industries such as Argentina and Colombia, and before just four years ago, there was no dedicated narrow web converting operation in the country.
This changed with the foundation in 2007 of Flexo Print, a Cochabamba-based offshoot of offset printer Sagitario, located in La Paz. In its short lifespan, the company has reaped the benefits of investment in advanced technology that has made it unique in its local market.
Unique offering
‘Bolivia is something of a virgin country when it comes to the label industry,’ says Juan Carlos Zamorano, general manager of Flexo Print, which employs 29 people. It was six years ago that Zamorano’s father and namesake, who founded Sagitario’s in 1986, decided to move into narrow web printing, encouraged both by the end users served by Sagitario’s offset operation, and by the presence among the company’s staff of a former press operator from German label converter Pago.
Through this link, as well as the local presence of Heidelberg in Bolivia, the company began conversations with Gallus and purchased an 8-color EM 280 press with hot stamping and two silkscreen units in 2007 to inaugurate its dedicated label division, Flexo Print. The machine was initially destined for La Paz, but concerns over the city’s altitude – at 3,650m it is the highest administrative capital in the world – meant the operation was set up in Cochabamba, a centrally located city where Sagitario already ran a sales office.
Investment has continued in the last 12 months with the company achieving impressive growth of 40 percent. An 8-color Nilpeter FA-4 press for shrink sleeve and wraparound label production was installed at the beginning of the year, along with two Karlville shrink sleeve converting machines and a second Rotoflex finishing machine – a VLI 440E – which joined a Rotoflex VSI 330E installed in 2009.
Other recent installations include a Karlville heat shrinking machine for the production of proofs, plate mounting equipment from Systec Converting and a Toyobo Cosmolight plate making system which was installed by Argentina-based Leftech, the Japanese company’s Latin America distributor.
Cochabamba’s 2,500m altitude can still pose challenges. Plates can sometimes bubble, so Flexo Print has worked with Toyobo to pass all plates through an altitude simulation to ensure there are no problems.
The equipment is housed in Flexo Print’s modern facility in Cochabamba, with a sales office for Sagitario also located onsite. The synergy between the separate operations is clear, with a number of Sagitario’s packaging clients also now being supplied with labels by Flexo Print.
According to Juan Carlos Zamorano, Flexo Print’s reputation for quality in the local market has led its brand owner customers to call for the company to further diversify into flexible packaging production, which he cites as an opportunity for the near future.
‘We are known in the market for our quality,’ he says. ‘The installation base of wide web machines in Bolivia is quite old, and we are the first narrow web converter in the country, so our clients are looking for us to be a one-stop shop for all their packaging needs.’
The company’s investment in advanced printing and converting equipment has been crucial to its success. In Bolivia, says Zamorano, local companies are often reluctant to invest, and Flexo Print ‘has reaped the benefits of taking the plunge’. ‘It’s a great strategic advantage to be able to offer added-value technology such as silkscreen and hot stamping, for example. Bolivian infrastructure can make it difficult and costly to import, so to be able to supply brands locally – with lower manufacturing costs and closer service – is a big advantage.’
Bolivia, says Zamorano, bore no impact of the global recession, with internal growth remaining strong. ‘In the last five years, never have taxes been so cheap and credit so readily available in Bolivia, so the timing of the investment has been ideal. Everything has come together perfectly.’
Shrink growth
At the time of L&L’s visit, Flexo Print was 100 percent dedicated to self-adhesive label production, with shrink sleeves and wraparound label production just beginning. Zamorano believes that shrink sleeves, particularly, represent an excellent opportunity for growth and could end up accounting for 50 percent of production in the future.
Local end users have shown a great deal of interest, he says, and the use of the Karlville machine for proof production has provided further encouragement.
Edgar Tejada, Flexo Print’s regional manager who takes charge of day-to-day operations at the Cochabamba site, cites the example of Coca-Cola, which approached Flexo Print with examples of shrink sleeve labels imported from Peru for its new energy drink, Burn, and offered the company the chance to compete for the work. Flexo Print produced proofs and, on the day of L&L’s visit, these had been sent back to Coca-Cola. With the labels’ notable improvement in color quality and contrast, Tejada and Zamorano were confident of encouraging the brand to opt for local service.
Household goods, pharmaceutical, personal care and beverage are the company’s major end user sectors, with Flexo Print seeing particular potential for shrink sleeve production for household goods and beverages. There also remains strong potential in the beverage sector for self-adhesive labels, with boutique wines and promotional campaigns on beer bottles both seeing increased self-adhesive label consumption.
The pre-press department, described by Edgar Tejada as ‘the company’s heart’, plays its own part in educating brand owners about what can be achieved with flexo printing technology, meaning that some design work also takes place in-house. An internal workflow system based on SAP, meanwhile, is currently being developed and will be installed by the end of the year.
Tejada emphasizes the importance of charismatic leadership and credibility in the market, philosophies he has worked hard to implement in the company. ‘In last two years, we have absorbed 90 percent of our competitors’ work,’ he says. ‘Cutting-edge technology has been the key. Combine credibility with good quality and a good price, and you can’t lose.’
Future plans
Flexo Print takes seriously the training of its staff. The company’s rising profile in the Latin American marketplace has led to it receiving multiple visits from leading industry suppliers with bases in the region. Flexo Print takes advantage of this flow of expertise, requiring them to give presentations to staff as part of the education process. Employees have also been sent to Denmark for workshops in staff care and environmental sustainability thanks to a B2B program organized by the Danish embassy in Bolivia.
The company is also preparing itself for future environmental sustainability legislation, which it says is likely in Bolivia in the future. The environmental credentials of the Toyobo Cosmolight system, which uses no solvents, was cited as an important factor behind the purchasing decision. Water is filtered and reused, consumables are recycled where possible and employees have also been sent on sustainability education courses run by Fundes Bolivia, an organization that assists with training and implementation of sustainability programs. ISO certification is also currently underway, also in cooperation with Fundes Bolivia, while Flexo Print is in talks with two local companies who are interested in using its liner waste in dry walls.
Flexible packaging is named as a potential area for future growth, but Zamorano says that the company won’t try to compete with long run work handled by wide web companies, rather target the short run flexible packaging market.
Security products are also an area of interest; Flexo Print currently imports certain security products but does not yet manufacture them in-house. Landlocked Bolivia has extensive borders with Peru, Chile, Argentina, Paraguay and Brazil, and contraband represents a big problem in the country. Counterfeit goods and illegal imports often line supermarket shelves, says Zamorano, making it hard for local companies who are adhering to the law.
To border so many countries brings its own advantages, however. Bolivia’s central location and large number of neighboring markets, combined with the fact that it is one of the cheapest nations in the region, provides great potential for export. Edgar Tejada cites northern Chile and southern Peru – both far from their respective capitals and industrial bases – as regions which Flexo Print intends to target.
Flexo Print’s impressive growth since its foundation shows that in Bolivia, the trend of end users importing their labels is changing. The company is not only clawing back its local market – bringing its customers a level of quality previously only available abroad – but will soon reverse the trend and win work from markets that used to serve its own.
Rotoflex sees increasing quality demands
Flexo Print’s investment this year in a second Rotoflex finishing machine is a positive endorsement of the company’s willingness to invest in top quality technology. For Rotoflex’s Latin America sales manager, Francisco Soto, it is further proof of the increasing buying power of the region’s converters and demands for higher quality from end users.
Soto estimates the total installation base of Rotoflex machines in Latin America to be more than 650, with sales consistently strong over the last two years and particular interest in the company’s V series of equipment, which includes the VSI and VLI finishing machines.
‘I have seen a vast improvement in the technological requirements in the region,’ he says. ‘It has been very rewarding to sell high quality machines into a market that remains price-sensitive and where political and cultural challenges are present on a daily basis. Our customers in the region have really embraced the technology, understanding that it can help them to gain a competitive edge. Rotoflex represents superior technology and workmanship that will ultimately reflect in the quality of the finished product, which helps them to expand and grow their businesses.’
Countries such as Brazil and Mexico have traditionally been strong, but Soto sees a trend towards companies from the region’s smaller markets increasingly investing in advanced technology. ‘There has been a great deal of growth in countries such as Peru and Venezuela, while the fact that we now have two Rotoflex machines in Bolivia also shows that these smaller markets are making significant progress.’
According to Flexo Print’s Juan Carlos Zamorano, the decision to invest in a second Rotoflex finishing machine was not a difficult one. ‘We’d already had a good experience with the first machine, and the local support offered by the company – crucially, in Spanish – as well as the machine’s easy maintenance, made it an easy decision,’ he says. ‘Technical support is crucial in the investment decision.’
Pictured: Juan Carlos Zamorano outside Flexo Print’s factory in Cochabamba, Bolivia
This article was published in L&L issue 6, 2011
Stay up to date
Subscribe to the free Label News newsletter and receive the latest content every week. We'll never share your email address.