Revolutionary inkjet CtP set to change label platemaking
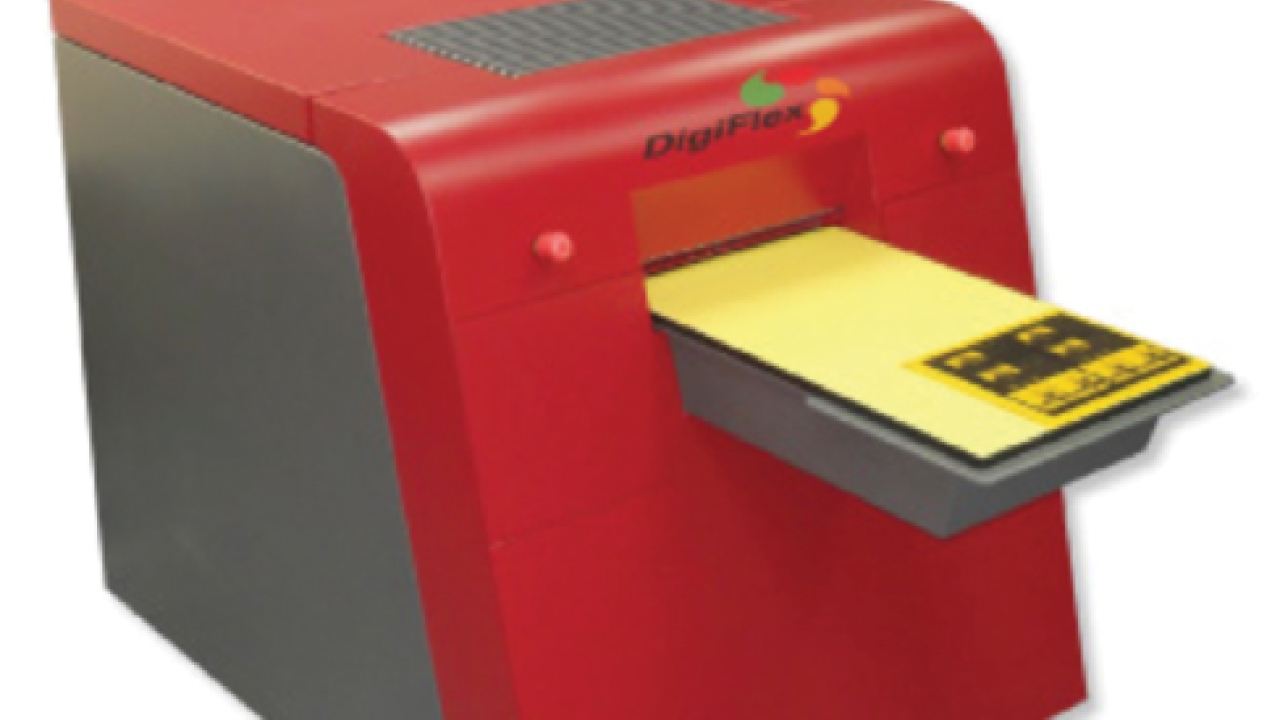
A new computerized inkjet platemaking system offers label converters a new solution for high quality printing plates with amazing dot shapes, at an affordable price. Mike Fairley visits DigiFlex in Israel to review the technology and assess progress to-date
Plate imaging and processing for the label industry has undergone numerous changes over the years, from conventional camera, film and plate processing to the newer technologies using some form of computerized system. Certainly, both computer-to-film and computer-to-plate technologies have had their devotees in recent years for the production of flexo, letterpress and dry-offset printing plates.
Computer-to-film systems utilize UV beams passing through a film mask to change the surface characteristics of a plate surface prior to a mechanical washout process, drying and plate hardening; Computer-to-plate systems based on laser ablation use a laser beam to write an image on to a pre-coated plate surface, in the process destroying the surface coating of the image areas, again enabling mechanical washout, drying and hardening.
Now a new computerized plate-making system has come to the market. Shown at Labelexpo and drupa – where they commenced worldwide sales – the DigiFlex inkjet computer-to-plate system has already created considerable interest for the excellent quality and high performance of plates produced, for the speed of processing, for fast make-ready, and for being an environmentally friendly process.
What’s more, it enables label converters to move up from a negative film system to the new technology at an affordable price. This latest CtP solution eliminates films and the film exposure process, yet offering higher quality results – but still uses the same, affordable analogue plates as before. It also provides an excellent alternative to laser ablation technology.
Distributors have already been established through Jet Europe BV – the second biggest distribution group in Europe, with distributors in some 36 countries – and most recently through Anderson & Vreeland for the USA and Canada.
So how does DigiFlex technology work? In simple terms, it’s based on a unique, patented, ink technology which is designed to enable extremely high print quality (initial tests have shown a higher quality result than HD flexo) to be produced from a flexo, letterpress or dry-offset plate and, now, in a new development, from rotary screen process stencils as well.
Creation of the image area on the plate is achieved using a special bi-component (reactive) ink which is inkjet-printed to produce a UV opaque mask onto a polyester film substrate – using appropriate software and a modified Epson printer as the system’s engine – and which chemically reacts instantly with a second reactant on top of the plate to freeze the ink droplets without any time for ink spread. The outcome is a high resolution, with zero dot gain on the plate, and the capability of achieving a two percent dot on the press. Currently the minimum dot-size is 23 microns, but a complementary technology still to be launched is planned to go even smaller in the future, with a dot size approaching 10 – 15 microns.
The reactive layer is then transferred from the polyester substrate to the top of the plate using a lamination process. The primer layer, which has no reaction with the plate surface, is washable during the plate development process and can be used with all standard water-washable plates, with solvent washable plates, with rotary screen pates and with Cosmolight plates. Effectively, after the image has been created on the plate, the rest of the plate-making process remains unchanged, so providing minimal adaptions to an already familiar workflow.
The resultant DigiFlex plate dots are flatter than dots produced by computer-to-plate laser ablation, enabling easier set-up on the press and better ink capture. Under magnification, the DigiFlex dots are perceived to be sharper and more solid when compared to laser ablation produced dots, which appear more cloudy and gray: results that can truly be said to revolutionize the label plate-making process – and at an affordable price for a quality computer-to-plate-making system installed in-house.
Certainly the ability to keep the full plate-making process in-house results in savings in time and money, provides total control over the plate-making process to be achieved, and enables the converter to create opportunities to take on board more jobs of a higher quality – all better serving their customers.
Based on patented technology developed over several years by a group of scientists and technologists with an excellent printing industry track record and semi-conductor vision for growth gained at companies that include Scitex, Kodak, Creo, Agfa Graphics and Applied Materials Israel, Digiflex offers the label converter a novel system for producing high quality, high throughput, affordable and easy-to-use plates.
Hezy Rotman, CEO of DigiFlex told Labels & Labeling, ‘Our inkjet CtP system commenced worldwide sales at drupa and we already have extensive distributorships established to enable us to rapidly grow the market; a market that has rapidly realized the excellent quality and superior cost-of-ownership our solution brings to producing high quality printing plates with amazing dot-shapes for label and tag printers.’
There seems little doubt that after drupa, and a further showing at Labelexpo Americas on the booth of Anderson & Vreeland, much more will be heard about DigiFlex and the way in which it is revolutionizing label platemaking in the year to come.
US distributor strengthens global network
In August, DigiFlex appointed Anderson & Vreeland as its distributor in the USA and Canada. The company’s Flexojet1725 inkjet computer-to-plate system was shown in the A&V booth at Labelexpo Americas.
Hezy Rotman, CEO of DigiFlex, commented: ‘We are delighted to have A&V as our partner for North America, and are certain that it will enhance our market presence.’
Darin Lyon, VP and general manager of Anderson & Vreeland, added: ‘The unique technology of DigiFlex immediately attracted our attention. A careful technical examination proved excellent performance. We are excited to bring this solution to our customers.’
This follows the announcement last year that Jet Europe would distribute DigiFlex technology in Europe. That agreement covered the sales, marketing and technical support of the FlexoJet 1724 as well as the associated DigiFlex ink and DigiFlex coating sheets.
Harry Heesen, managing director of Jet Europe, commented: ‘This FlexoJet 1724 computer-to-plate system serves as a great motivation to replace the low quality film solution and will bring the CTP world to everyone. It will also complete our product portfolio.’
Pictured: The Digiflex inkjet Computer-to-Plate system
This article was published in L&L issue 5, 2012
Stay up to date
Subscribe to the free Label News newsletter and receive the latest content every week. We'll never share your email address.