Making your label stand out from the crowd
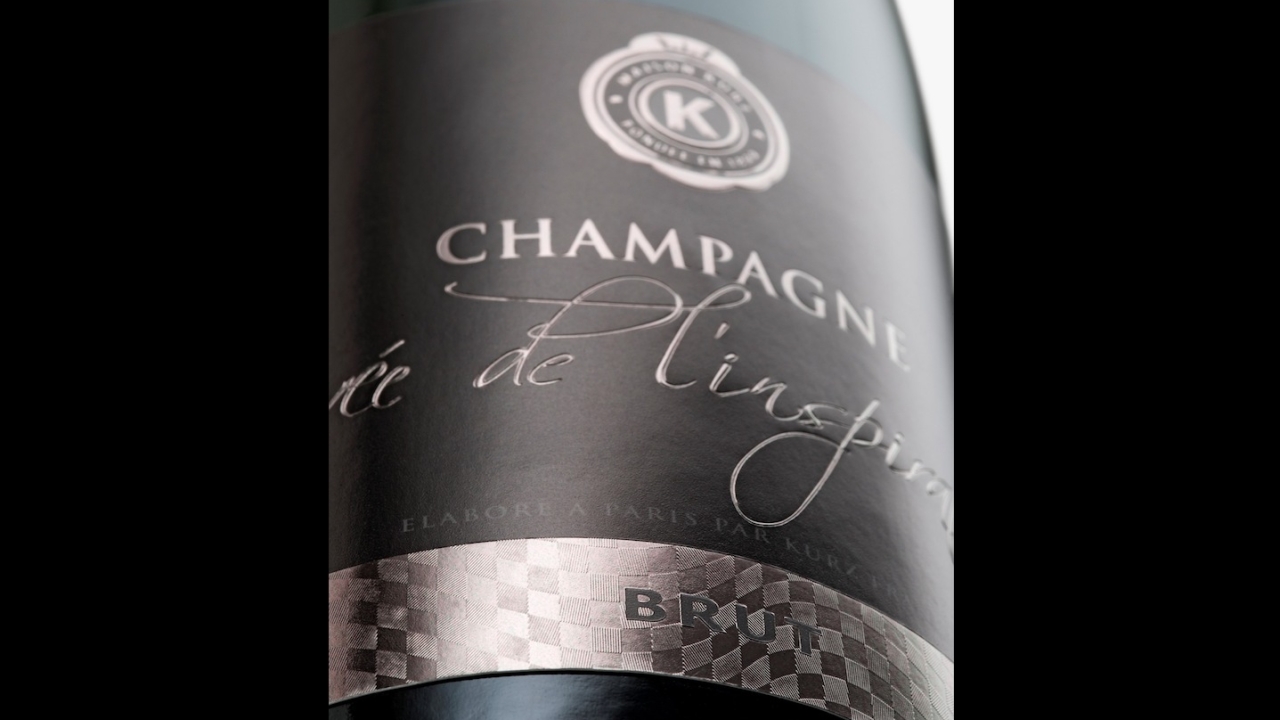
In this article, we hear from three companies very much involved in helping label converters to achieve that little bit extra when it comes to adding value to the label. We will see that foiling can add that extra sparkle to the label, embossing can give the label depth and micro-embossing can add a layer of security to expensive products. Finishing can project a product from the ‘also rans’ to the exceptional.
Has flatbed got the answer?
The market for high value consumer goods such as wine and spirits requires more and more highly embellished label designs. Contemporary approaches range from exquisite single foil to complex multi foil designs which result in labels which attract buyers’ attention and assign a high value to the underlying product. This means that they are an essential cornerstone for the success of the brand owner. With the efficiency and versatility of flatbed technology, converters are provided with a powerful tool to offer outstanding labels for high-quality consumer goods at a low additional cost.
Rotary hot and cold foil stamping are well established in the self-adhesive label industry. Rotary in-line stamping achieves satisfactory results on closed surfaces. When it comes to open substrates as those used for wine and spirits, the disadvantages are obvious. Cold foil adhesive is absorbed by the material; hot foil stamping is considerably slowed down on rough materials. If relief embossing is carried out subsequently, part of the gloss is lost and the relief height is comparatively limited. Finally, attaching several foils requires several machine runs.
The solution is flatbed embossing. For foil transfer from carrier tape to substrate, the contact time is more than seven times longer with flatbed stamping systems than with rotary and even more with semi-rotary systems. The energy utilization increases, and less expensive and slower transferring foils can be used. Providing a revolvable head is used, flatbed systems can also place several foils across the web. A robust in-line flatbed stamping system such as the Pantec Rhino achieves high relief height, extraordinary brilliance and perfect register accuracy of the embossing relief.
Multi-foiling and registered foils for outstanding designs
Lenses, 3D spatial effects and holographic foils are among the latest developments in label and packaging design. These unlock completely new design possibilities but only work if applied in perfect register. Multi-stroke systems allow the application of several foils in one machine run in perfect register. Pantec’s Rhino for example enables the application of different foils in register using one tool. It‘s even possible to emboss the substrate itself or only the foil to enhance its effect. These are some of the effects that can be used to gain the consumer‘s attention.
With holographic foils and their subsequent optical effects, labels will stand out even more. The transparent design of the lenses makes it possible to superimpose image motifs, colors or logos with a unique holographic depth. In order for the optical effects provided by these new technologies to have an influence on the packaging or label, the lenses must be positioned exactly in register above the motif.
For brand owners, embellishment is an invaluable opportunity to better position their products on the supermarket shelf. Nevertheless, they are often quite hesitant if these refinements entail substantial additional costs.
The only objection that can be levelled in this case is ‘at only extra cost’, as propagated for example by Pantec. This is made possible by systems that work with efficient materials (= foils), cost-efficient flatbed tools, which can be integrated into existing processes without restrictions according to speed or job change time.
In 2010, Pantec turned the label world upside down with the introduction of the Rhino flatbed system. A high-stroke frequency system suddenly opened up in-line label finishing and gave high-end converters an incredible productivity boost.
The Rhino S is capable of running at up to 30,000 strokes per hour and fully capable of operating in-line with printing presses dedicated to producing labels with a high degree of embellishment. Today, more than 150 systems are operating worldwide, mostly in an in-line configuration.
The Rhino E completes the Pantec narrow web portfolio and is optimized for less complex labels and the refining of digitally printed labels.
Hot stamping
Hot stamping offers a diversity of design options for ensuring the attractive presentation of products through appealing packaging. The continuing trend to maximize design possibilities is evident in the ever-increasing number of products that are finished with stamping foils.
The unique color effects originate primarily from the various coatings on the stamping foil. These effects, in particular metallic and holographic, are not easily achieved with other printing methods which use printing inks or lacquers. How else could realistic representations of metals such as gold, silver, copper, brass, bronze, stainless steel, chrome, anodized aluminum with a mirrored, polished, brushed satin, sand blasted, matte, satin-gloss or extremely matte finish be achieved?
Holographic hot stamping foils exhibit three-dimensional effects, allow virtual animations to be created, and produce color movement effects as the direction of the viewing angle changes.
Further design possibilities are offered by hot stamping foils with bronze/metallic effects, pearlescent effects, transparent or transparently-colored, high gloss finishes, or plain opaque color effect foils with an elegant matte surface.
The ability to overprint stamping foils in multiple colors using translucent inks in a subsequent printing process, whether by offset, flexographic, silk-screen or gravure printing, creates further design possibilities as can the stamping die.
Flat hot stamping is the most widely prevalent form of hot stamping, and the one in which the purely visual effect of the hot stamping foils is shown to the greatest advantage. In the example shown pictured the transfer appears to lie in the same plane as the print substrate, but is always slightly recessed due to the required stamping pressure.
In addition to the flat transfer of stamping foil, it is also possibleto three-dimensionally crimp the substrate by means of relief embossing. This not only enhances the viewer’s perception in a purely visual sense, but also achieves an additional communication element on account of its tactile facility. Tactile sensations have the second highest intensity, after visual stimuli, in the selection process involved in human perception.
In addition to the tactile effect, detail-rich reliefs become highly attractive design elements, for example when Kurz metallic Luxor/Alufin hot stamping foils are used. The high metallic luster of Kurz stamping foils also highlights the different height levels and interplay of the relief structures.
Very fine structures in the stamping die distort the foiled surface of the stamping substrate and create impressive reflective effects. Micro embossing is mostly achieved without a counter die and can be combined with all types of stamping dies (flat, emboss, and combination dies).
Nano embossing, the most recent development of Hinderer + Mühlich, enables the creation of 40 percent finer textures than micro embossing. This opens up almost endless design possibilities, such as matte/glossy combinations, satin finishes, crystal clear flip flop effects, improved security features, real brushed designs, and photographic effects.
With the stamping die manufacturing technologies available today, it is possible to implement any combination of the effects described above in a single stamping die.
Adding value to the label
As we have seen, there are number of enhancements which converters can add to labeling and packaging to provide decorative value and functionality to the surface of a label.
Nowadays the most common forms of label embellishment are hot foiling, embossing, and special effects with inks, varnishes and many others.
The flat foil stamping process is a premium process that can be used on printed labels to add the perception of luxury. Italy-based Cartes has historically been producing finishing machines for this process for the reel-to-reel label market, typically the GT360 series of machines.
The Cartes flatbed hot stamping unit is mainly used for the dry printing process which uses heat, foil and pressure to transfer the image from the foil by means of a metal (brass, copper, magnesium) die onto a label substrate. Foil stamping is an incredibly versatile process that allows the converter to explore imaging on different surfaces where conventional printing techniques cannot be applied.
Thanks to the multi-foil feeding systems (two in transversal and one in longitudinal direction) and multi-step regulation, the printing/embossing process can be done at full speed, in a single pass. If the design is properly structured, the hot stamping process can be combined with embossing, even with multiple foil colors (different finishes and effects like imitation leather, wood grain, marble, holograms, pigments, matte and gloss foils).
Sometimes no foil is used for the actual embossing process to produce an embossed or de-bossed element on the label surface. The process involves the application of high pressure, which forces the male relief image into the female recessed image on the face side of the label substrate and is regulated by four centesimal gauges to ease the pressure set-up.
In addition to cold embossing, the hot foiling process can be combined with the application of a metallic foil over a special varnish to achieve a new and unique relief effect, which is also known as metallic doming.
To achieve a raised tactile effect, a varnish is applied using a flat silkscreen printing unit followed by curing using a powerful UV curing unit. A thermo-active metallic foil is then laminated over the relief image With the silkscreen printing unit it is also possible to achieve very elegant simple decorative effects with the use of gloss or matte varnishes on any type of paper or film surface.
Cartes’ GT360 is a fully modular and versatile machine which can be equipped with hot foil stamping, embossing, silkscreen printing, flexo varnishing, laser converting and semi-rotary or flatbed die-cutting. The machines are equipped with a Multi Head Positioning System (MHPS) which automatically corrects the position of each operating unit to ensure the best possible registration. Other applications which can be added to the GT360 include the possibility of printing Braille and metallic doming, hologram application and UV lamination, among others.
Cartes can add laser die-cutting to its inventory of modular devices, more recently the Invisible Laser Cutting (ILC) technique, which when cutting labels printed in dark colors avoids the unsightly ‘white edge’ result. The ILC system offers very few limitations when processing extremely thin liners including films or linerless materials such as in-mold labels. The mechanical strength and adjustments available on each machine, guarantees high precision on the most complex and elaborate jobs and make it possible to obtain high quality labels.
All these techniques mentioned are the most cost-effective ways of adding a distinctive elegance and additional value to any label substrate.
Stay up to date
Subscribe to the free Label News newsletter and receive the latest content every week. We'll never share your email address.