Indian film giant continues expansion
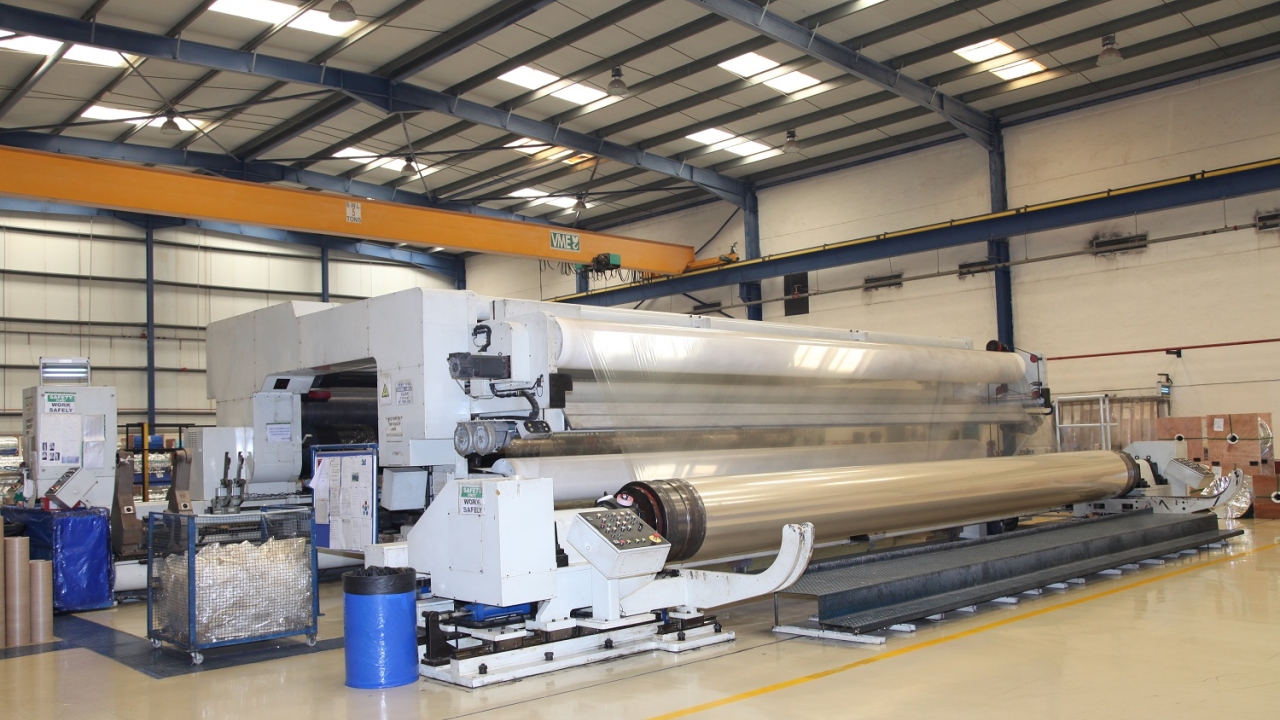
Indian multinational company Uflex has commissioned its aseptic liquid packaging material manufacturing plant in Sanand, Gujarat. Built with an investment of 580 crore INR (approximately 85 million USD), this plant has been set up in an area of 914,760 sq ft (21 acres) within a 72 acre plot of land. The remaining land has been bought for any future expansion.
Anantshree Chaturvedi, vice chairman and chief executive officer of Flex Films International, a division of Uflex, says that India is beginning to see an influx flexible packaging materials. ‘If we look at the organized flexible packaging market in India comprising both polymeric films and flexible packaging products, it is pegged at around eight billion USD,’ he reveals.
‘This market has been growing between 15 to 17 percent per annum over the last few years. Given the fact the per capita packaging consumption in India is just about 4.3kg as compared to 42kg and 19kg in Germany and Taiwan respectively, there is a huge potential for the industry to grow at around 20 percent hereafter. The use of labels is less than one sqm per capita, which is still miniscule when compared to the usage patterns in the mature markets. Thus the potential is huge.’
He predicts that private label enterprises will lead this growth in India, while in the other developing economies ‘the traditional food and beverage companies have far too many legacy investments plaguing them. Therefore such companies will take time to switch to new formats.’
A recent study by AWA Alexander Watson Associates estimates the Indian label market has been growing by 10 percent every year. Glue-applied labels still dominate the market with a 57 percent share. Pressure-sensitive labels account for approximately 31 percent, while sleeve labels and other unidentified labels each take a six percent share.
In this growing market, Chaturvedi believes that digital will stand the test of time. ‘I can clearly see the Indian market trending towards more customized and bespoke offerings, many players, shorter turnaround times and more ecologically sustainable solutions,’ he says. According to industry estimates, the number of operational digital label presses in India had reached 22 by the end of March 2017.
However, he points out that India is a cost-sensitive market. ‘The current per unit cost – primarily due to the cost structure of per click cost – makes this model difficult to scale in large populous markets such as India. The best segments for this technology in developing nations are short-run urban markets which supply higher-priced luxury goods to a limited niche segment of the market, for example, organic foods or high-end gelato.’
Green policies and products
Flex Films, a global film manufacturing arm of Uflex with polymeric film manufacturing plants in India, UAE, Egypt, Mexico, USA and Poland, is committed to the environment with its reduce, reuse and recycle policy. ‘These are the pillars that help us consume most of the polymers we make in-house so we reduce our overall carbon footprint. Along with that we offer a wide variety of post-consumer-recyclate and green source based PET.’
The company reduces at source and its research and development team works towards downgauging polymeric substrates, which leads to light-weight laminates. ‘We have successfully developed plain or heat sealable BOPP films as thin as eight micron; BOPET films with 6.5 micron thickness and heat sealable 12 micron metallized BOPP films that are suitable for printing and lamination. These films possess comparable machinability parameters to conventionally thicker films and provide significant reduction at source. These films have much lower carbon footprint than the films they replace,’ Chaturvedi explains.
Products engineered by Uflex includes green PET films using PTA (Purified Terephthalic Acid) manufactured from the oxidation of p-xylene, 9.5 micron PET ALOx transparent film with WVTR and OTR both significantly less than one, and green MEG (Mono Ethylene Glycol) manufactured from ethanol obtained from agro-based sources.
The company also manufactures rPET film which contains post-consumer recycled PET resins obtained from re-processing waste such as used PET bottles which otherwise would have been consigned to landfill. rPET films are USFDA and EU compliant for direct food contact, having the same properties as films made from virgin PET resins.
A special patented biodegradable polymeric film, Flexfresh, keeps freshness intact for fresh fruits, vegetables and flowers and works on the principle of Active Modified Atmospheric Packaging (AMAP) technology.
‘Flex Films sees downgauging as a natural trend that offers significant throughput benefits to convertors while at the same time reducing material usage and wastage on both ends of the product conversion,’ says Chaturvedi. ‘We use renewable resources and maximize post-consumer recyclate usage, reduce production waste, reuse all-production waste, use all non-recyclable waste to produce energy and progressively optimize energy consumption. We have developed a technology for reprocessing the waste arising from production of various flexible packaging products. This helps in reduction of material waste at landfill, underscoring the importance that we ascribe to environment and sustainability.’
He concludes by assuring that law makers in India are creating single stroke policies that provide quantum leaps towards sustainable practices. ‘I feel the world will be a very different place by 2020 when it comes to sustainable practices and legislation.’
The consolidated revenue of Uflex stood at 65,294 million INR (approximately 1 billion USD) in the 2016-17 financial year, of which its international business accounted for approximately 50 percent. The revenue of Flex Films for 2016-17 financial year stood at 543 million USD, constituting 57 percent of the total consolidated revenue of Uflex for the period.
Stay up to date
Subscribe to the free Label News newsletter and receive the latest content every week. We'll never share your email address.