Raising the image
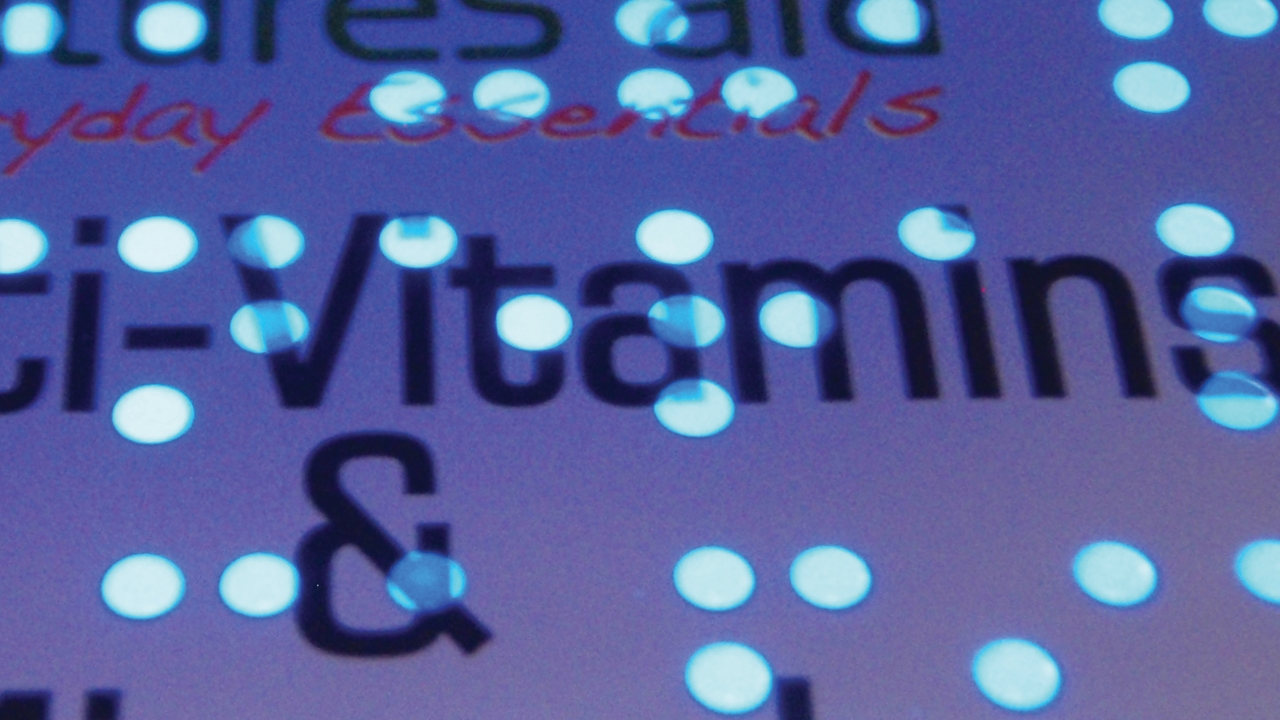
L&L technical editor Barry Hunt suggests changes in Braille usage for pharmaceutical products may have wider consequences
Converters supplying the pharmaceutical and healthcare industries are used to working within legally binding guidelines. Sometimes changes or extensions to existing legislation may involve a revamp of production methods. In a few instances they may have implications for the industry beyond the initial application. This could be the case with the recent changes to the European Union's legislation in respect of using printed or embossed Braille to allow blind or partially-sighted people to identify medicine names and dosages. Changes effective from October 2010 now include a uniform representation of Braille alphabetical characters, including a standard height. They apply to small folded cartons, labels, leaflets, extended text labels and booklet labels for pharmaceutical products.
The EU amendments had been flagged up well in advance, and encouraged some specialist suppliers to adopt new approaches to Braille printing. Other companies have introduced new types of off-line inspection technologies, as well as electronic proof-reading software and Braille verification tools for use by pharmaceutical companies. The influence of the EU's pharmaceutical legislation is not necessarily restricted to the European member states. In North America, for example, the voluntary Can-Am Braille set of guidelines and recommendations resemble those used in Europe.
Of course, this type of technology is also used for producing labels or packaging that warn blind people about potential hazards, such as household bleaches. Similar tactile labels are also found on certain grocery products to mark 'best-before' dates, and are used to signify alcoholic strength on labels for wines and spirits. One area of potential growth is the Braille labeling of veterinarian products.
Marking techniques
Braille embossing using male and female dies remains the prime method of identifying folding cartons, usually combined with cutting and creasing as part of a sheet-fed process. Developments include the AccuBraille embosser from Bobst for high volume applications, which moves the process further down the production line to the folder-gluer. Similarly, Cava UK offers the servo-driven RotoBraille system, which positions the embossing plates accurately across the carton blank. It can apply Braille embossing on one to four panels, as required, with precise control over the dot height at full folder-gluer speed. Available as an OEM or retrofit, Cava says the system offers a cost effective alternative to buying new converting equipment.
Carton printers often use micrometer calipers to measure the tactile quality of embossed Braille dots. Machine-vision inspection systems potentially offer greater accuracy and take less time. An example is the DotScan from in-situ, a Munich-based firm, which uses a ‘shape-from-shading’ technique to evaluate Braille dot patterns. The formation of each Braille dot is measured by analyzing gradual shading variations across captured gray-level images. Four blue LED lamps illuminate the flattened sample sheets in the DotScan unit from four directions to create 3-D shapes of a raised dot. In-situ also supplies a PDF reader to ensure the accuracy of Braille content at the pre-press stage.
When it comes to printed Braille, the usual method is to use rotary screen printing as a narrow web combination process. Screen is ideal for laying down thick layers of ink or a colorless varnish in a single pass to form the raised dots within precise limits, before ‘fixing’ them with UV curing. One well proven application is for tactile warning labels printed on a clear filmic labelstock for free positioning on a pre-printed primary label, booklet or pack. This method does not impair the readability of the underlying graphics or text by sighted people. The two principal rotary screen suppliers offer media grades intended for printing Braille: Stork Prints with its RSI print units and RotaMesh nickel screens, and Gallus's Rotascreen units and Screeny plates. A small-run alternative is flat screen printing on slower stop-start web-fed presses.
The inkjet effect
The development of digital inkjet as a Braille printing technique is a direct effect of the legislation mentioned earlier. The pharmaceutical industry already uses this non-impact process as part of its manufacturing logistics. In a wider context, converters are becoming more familiar with the technology's finer points within the short-run digital printing scene. Flexibility is a major benefit since inkjet integrates well with most web-fed presses or off-line platforms, including booklet label lines and overprint/inspection machines.
This applies to the current examples of Braille inkjet, although the printheads and software-based controllers differ from inkjet's conventional drop-on-demand, piezoelectric techniques. Printing raised dots with a clear varnish introduces several issues in respect of viscosity and surface tension levels. This in turn affects ink flow from the nozzles, which must deposit the right drop sizes at a realistic printing speed. One answer is to generate drops of pressurized ink using a form of microvalve or mechanical valve technology of the type used for low resolution, low frequency carton printing.
For example, the printheads for Atlantic Zeiser's Braillejet system use microvalve technology developed by its technology partner Gyger. They print two lines of Braille characters simultaneously at up to 36 m/min (118 ft min). Up to eight Braillejet modules (or any conventional printheads) are automatically controlled and monitored using an Alis-Jet Controller from Nikka Research. On-screen simulation of printer fonts includes Braille dot spacing in different orientations. UV curing is via an air-cooled Sensecure UV curing module. Braillejet can also include BrailleVision, an in-line camera control system which incorporates specially calibrated optical camera filters and adjustable illumination. A monitor displays the camera's software settings and Braille characters. Both units can form part of third-party roll-fed or sheet-fed modular platforms, as recently demonstrated by Prati.
Packages could also include AZ's Omega 36 HD inkjet encoding units. Interestingly, they were among the first to employ LED-based curing in the form of the company's Smartcure ink curing system. Low energy and long life LED lamps are available on a few single-pass inkjet platforms, but the present level of curing performance is generally considered unsuitable for printed Braille. An exception is Roland DG’s VersaUV LEC-330. The 29-inch wide (762mm) roll-fed inkjet printer and cutter lays down clear and white ink, as well as CMYK, using LED-cured ECO-UV coatings. The range of textured finishes and special effects includes Braille, obtained with multiple passes.
An interesting example of dedicated inkjet technology is the BrailleMaker One from Convertec Graphic Technics in Sweden. It first appeared at Labelexpo in 2007 billed as a stand-alone digital Braille printer for pharma labels, leaflets and booklets. The latest Version 4 has upgraded software that meets the new EU directive. It prints at up to 35 m/min and comes in widths of 150mm and 335mm.
The company says it has 20-plus installations in Europe and Canada including the pharma label divisions of CCL, Reynders Etiketten, Chesapeake, New Era, and Schfer-etiketten. Peter Nobelius, managing director, said interest is coming from other sectors: 'We talked recently at a trade show with a label producer in Kenya who actually had a demand to produce Braille on labels for canned green beans. So the interest is increasing from all kinds of areas and the legislation will eventually affect us all in the label world.'
Off-line operation increases the machine's flexibility and set-up, says Nobelius. 'Braille printing requires a constant machine speed to ensure uniform-sized dots. Constant web tension is also vital to avoid web stretching and displaced dots. In-line modular presses tend to require 12 printheads or more on a 335mm wide press with four labels across, whereas six to eight printheads are normal on a corresponding off-line unit.' He adds that users can mix luminescence pigments into the clear varnish to help with inspection.
The latest development incorporates a BrailleMaker One into an automatic label line. This was developed for a Danish pharmaceutical label printer to process large volumes of short-run jobs with overnight turnarounds. The line includes an EFI Jetrion 4830 CMYK inkjet press, working in tandem with a Spartanics dual-beam laser cutter with multiple unwinds and rewinds. A customized FleyeVision camera-based system from ABG International verifies the Braille printing. A barcode scanner is included to differentiate individual jobs produced as a single master roll. (A full description of this installation will appear in the next edition of L&L).
Convertec offers a cost calculation spreadsheet that compares an off-line BrailleMaker One with a Stork Prints RSI rotary screen module mounted on a flexo press. It involves 25 data points covering machine operation costs, job/run lengths, set-up and changeover times. An order for 25,000 labels, printed three across the web at a top speed of 32 m/minute, or 104 ft/min, would cost 295 euros (US$390) using a BrailleMaker One unit and 1,006 euros (US$1,329) for screen-printed Braille, according to Convertec’s calculations.
Fault-free production
Achieving zero-defect production through 100 percent web inspection is a vital component of pharmaceutical label production. These systems usually employ three-chip color line cameras to scan a web's entire width line by line, rather than area scanning to 'sample' images as with conventional video web viewing. Inspecting raised dots formed by transparent varnishes in real time demands a different approach. The main criteria is verifying dot positions and determining accurate relief height. Nikka Research recently introduced a dedicated Braille module for its Alis-L2 system to decode, verify and check the quality of raised images. It supplements Nikka's existing luminescent-based system for decoding and inspecting screen-printed Braille in multiple rows. AVT also offers a Braille inspection module as part of the PrintVision/Helios UV series.
ABG sales director Tony Bell says the company has tried several inspection methods to check the correct positioning of Braille dots on its FleyeVision: 'They all have worked to varying degrees of satisfaction, but the chosen method involves using white light illumination. Basically, each dot forms a shadow. Someone has likened the effect to a person standing up in a cinema and seeing their head on the screen.' Comparing inkjet to rotary screen for relief printing, Bell notes that screen can introduce air bubbles in the dot because of the agitation of the ink in the rotary screen head. Static may also cause mis-shaped dots.
EyeC from Hamburg offers a Braille inspection option for its off-line Proofiler, which gives pre-press file-to-file comparisons for converters and their customers. Tactile height, contents errors and other flaws on embossed or printed cartons and labels are inspected from the front side, rather than the back. The Braille characters are also decoded and displayed on a monitor.
In conclusion, it is unlikely we will see the demise of rotary screen printing for Braille and similar tactile printing. The use of embossing will also remain a mainstay of carton production, while further developments for printed matter is entirely possible. The progress being made with inkjet printing of Braille dots and other raised images does, however, represent a significant technical step. Besides warning labels, anti-counterfeiting and other security-related applications are technically feasible given the long-standing availability of security inks and coatings. We can expect further improvements to Braille printing software, perhaps with a variable data input. The leading suppliers of drop-on-demand inkjet technology have yet to become seriously involved, but anything is possible in this fast-moving world.
What is a Braille character set?
Louis Braille, a blind Frenchman, devised the Braille system in 1821. Embossed or printed raised dots are arranged in a basic grid of two columns of three dots each to form character sets for reading and writing. This simple but effective form of digital writing makes it possible to represent up to 64 alphanumeric characters and other symbols. Some parts of character sets are common between countries, whereas other parts differ; for example between Latin Braille alphabets and accented letters and the versions used in Japan, China and other Asian countries.
The guidelines on Braille requirements for pharmaceutical labeling and packaging recommend using an alphabet system conforming to the Marburg Medium font. Designers must ensure the chosen Braille character set is appropriate for the country concerned and packaging suppliers must check all Braille artwork for accuracy and relevance to comply with the procedures of international drugs authorization bodies. With multilingual packs, the correct character sets should be included and clearly identified in the artwork.
This article was published in L&L issue 1, 2011
Stay up to date
Subscribe to the free Label News newsletter and receive the latest content every week. We'll never share your email address.