Iggesund Swedish mill becomes self-sufficient with new recovery boiler
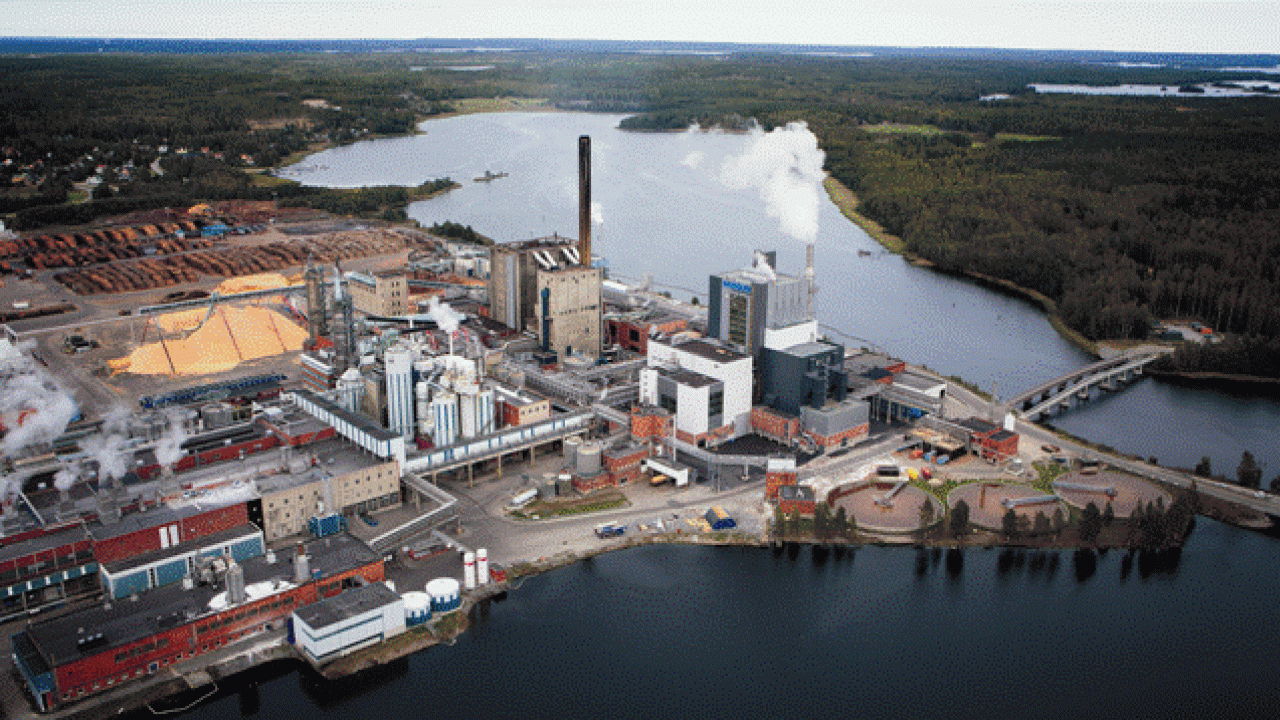
- Construction took two years and cost €240m
- Iggesund Mill to operate on 100 percent biofuel and be energy self-sufficient
Iggesund Paperboard has inaugurated a new recovery boiler at its mill in Sweden, enabling the facility to operate on 100 percent biofuel.
Construction of the recovery boiler at the Iggesund Mill took two years and cost SEK2.3 billion (€240 million).
Workington Mill
The company is also building a biofuel boiler at its mill in Workington, England. That investment, for the production of the paperboard Incada, will cost SEK1.1 billion (€123 million) and involves a radical change of energy source from today’s fossil natural gas to bioenergy.
The new biofuel boiler at Workington is scheduled for completion in the spring of 2013.
The ceremony was conducted by Lars G Sundblad, who was managing director of the company at the end of the 1950s, when the decision was made to begin manufacturing paperboard.
Biofuels
The new recovery boiler makes it possible for Iggesund to increase production of its paperboard Invercote, and also enables the mill to operate on 100 percent biofuel and be self-sufficient in energy, both thermal and electric.
The Invercote family consists of a range of products customised for different end-user applications. Invercote is a multilayered solid bleached board (SBB), made from chemical pulp produced by the sulphate pulping method.
The use of virgin fibre and the sulphate pulping method ensures a hygienic and odour and taint neutral product. All materials used in the making of Invercote are approved for food contact according to current regulations.
Read more on Iggesund here
Read more about packaging substrates here
Read more about green initiatives in the packaging industry here
Read more news from across Europe here
Stay up to date
Subscribe to the free Label News newsletter and receive the latest content every week. We'll never share your email address.