Epson installs first SurePress in North America
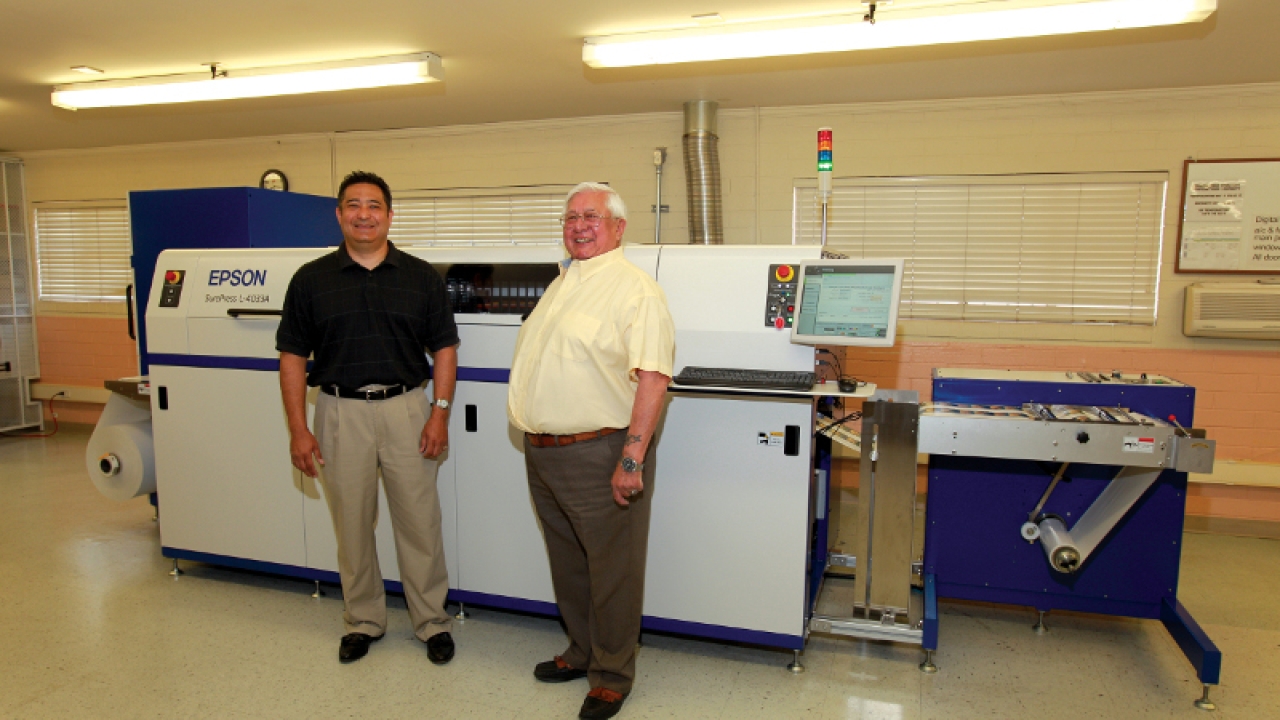
Danielle Jerschefske reports from Epson’s first digital label press customer in California
Tape and Label Converters (TLC), located in Santa Fe Springs, California, supplies brands like Boeing, Whole Foods, Pepsi-Cola, Miller and Disney with custom labels and manufactures personalized carton seal tapes, aerospace and military ID tapes.
Its broad customer base has a variety of needs. Vice president of sales and marketing at TLC, Mas Crawford, says, ‘Our run quantities are coming down, turnaround times are shorter and shorter. Clients send an order in and expect to see the product in two days, and don’t want to hold label inventory. Versatility and flexibility is the way the industry is moving.’
TLC installed the Epson SurePress digital inkjet machine to more effectively accommodate smaller quantities and provide shorter lead times for its customers. It was the official Beta site for the SurePress L-4033A, which utilizes the Epson micropiezo inkjet technology, is 13 inches wide and runs at 16 feet/min.
Already TLC has produced pharma and nutraceutical labels, and promotional materials for Disney on the digital machine. ‘Customers enjoy the quality of the SurePress. Epson’s technology has helped us jump start projects we simply couldn’t tackle before. We are able to give our customers the highest quality at a competitive price. The technology lends itself to open capability.’
Mark Elsbernd, North American region sales manager, Epson SurePress, notes, ‘While image quality, versatility and overall machine performance are a given, we are very proud of the relationship that we have been able to build with the team at Tape & Label Converters. Our service and support teams have a particular focus on the daily needs of the customer so questions such as press utilization, label applications and converting options are discussed on a regular and ongoing basis.’
He adds, ‘Our ability to listen, learn and adapt our methodology has been key in developing a mutually-beneficial environment and a positive digital experience for Tape & Label Converters. Epson is currently seeking other qualified printers in North America, like TLC, where SurePress can serve as a competitive, high-quality digital printing solution.’
Epson supplies a specially formulated industrial grade six-color water-based ink set called SurePress AQ. The hexochrome system offers a wide color gamut using orange and green plus CMYK to produce color close to PMS. The supplier has partnered with Wasatch, X-Rite and EskoArtwork to drive RIP workflow controls and color management tools capable of producing ICC profiles for consistency and repeatability in its digital label solution.
SurePress can run on standard self-adhesive label stocks and films (no pre-coating required) semi-gloss, gloss, matte paper stock, BOPP and PET without adhesion issues and TLC says there’s no need to corona treat material in advance. Since the ink is water-based there are no curing issues. ‘The durability is excellent,’ says Crawford. ‘The print is consistent. We’ve done a number of re-runs and the first and third run look the same.’
Crawford estimates that it can take only ten minutes from pre-press to the first saleable label and likes the complexity digital removes from the process. The converter’s average run can be from hundreds of feet to 3,000 feet or so, rather short for the time as the implementation is still in its infancy. Finishing the digital labels is easy with a Mark Andy 2200 fitted with a Rotary Technologies Servo 3000 re-registration unit. The converter can use existing dies.
The Epson piezo heads can drop various sized dots on the substrate that leave a finer printed gradation to zero. Crawford says, ‘the technology produces a very high resolution. It’s true photographic quality. The fade out and gradations are much better than with basic flexography.’
Crawford is the most trained operator on staff. From a business perspective, the converter felt that because he was going out to sell the product it would be best that he understand what the press is capable of. TLC is now in the process of cross training other associates to run the machine.
Nozzle maintenance is one of the most critical aspects to digital inkjet print consistency. The SurePress has an internal self-cleaning system and should go through a daily maintenance process. ‘The shut down time is reasonable,’ says Crawford.
Brand education
It’s critical that converters educate brands as much as possible about the technology advancements in the label industry and the benefits to them – quality, response time, sustainability and inventory control.
Crawford feels similar to other early digital adopters in the label industry. He says, ‘The toughest part about gaining adoption is getting customers, or anyone from outside the industry to understand. Their budgets are tight and they want justification for the step-up in cost.
‘Once they see how vibrant the colors are, the intensities of green, orange, blue and yellow and that the process gives them the vibrancy they’re looking for, the response is positive.’
So far TLC has switched about 20 percent of its flexo work over to digital production. The rest of the capacity is being filled by new business. The converter expects to increase the number of customers it switches from conventional as knowledge of the technology and its capabilities rises.
Crawford believes that the label industry is headed towards digital, ‘we want to be at the forefront and grow stronger as the technology becomes more commonplace. The SurePress is an excellent fit today for the short run label environment; we look forward to working with Epson in the future.’
Pictured: (l-r) Mas Crawford, VP sales and marketing, and Robert Varela Sr, president
This article was published in L&L issue 3, 2011
Stay up to date
Subscribe to the free Label News newsletter and receive the latest content every week. We'll never share your email address.